随着汽车制造业的不断发展,新车型的开发周期越来越短,对产品质量的要求也越来越高。在这个背景下,汽车功能主模型作为新车型开发中的重要检具,其有效运用对于缩短产品开发周期、提升产品质量具有重要意义。
传统的汽车功能主模型多采用铝合金材料制作模拟块,但铝合金材料密度较高,为了增强模拟块强度而加厚部分壁厚,以及为了方便拆装零件而设置的结构布置,导致模拟块重量远超实际零件产品。安装到实车后,由于重量过重,易引起偏差,限制了其在实车上的应用。
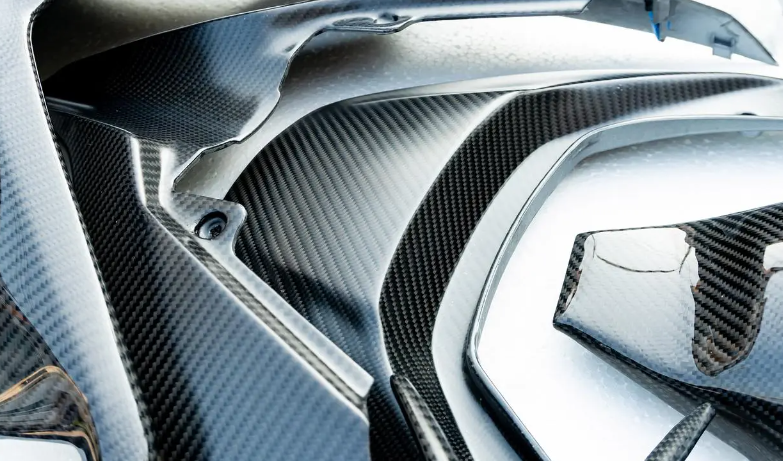
为了解决这一难题,本文发现碳纤维在强度、刚性、密度等方面均满足要求。使用碳纤维制作的模块,既适用于汽车功能主模型,也可安装到实车进行实车匹配分析。这种材料的引入,无疑为汽车制造业带来新的可能性与突破。
碳纤维作为一种高性能材料,具有轻质高强、耐腐蚀、耐高温等优点。使用碳纤维制作汽车功能主模型,不仅可以降低模拟块的重量,提高其刚性和强度,还可以提高零件的耐磨性、抗冲击性和耐疲劳性。此外,碳纤维还具有优异的电磁屏蔽性能,可以有效地保护车辆内部的电子元件免受电磁干扰。
在汽车功能主模型中应用碳纤维材料,不仅可以提高模型的精度和稳定性,还可以提高产品的质量和性能。同时,这种材料还可以降低生产成本和提高生产效率,为汽车制造业带来更多的经济效益和社会效益。
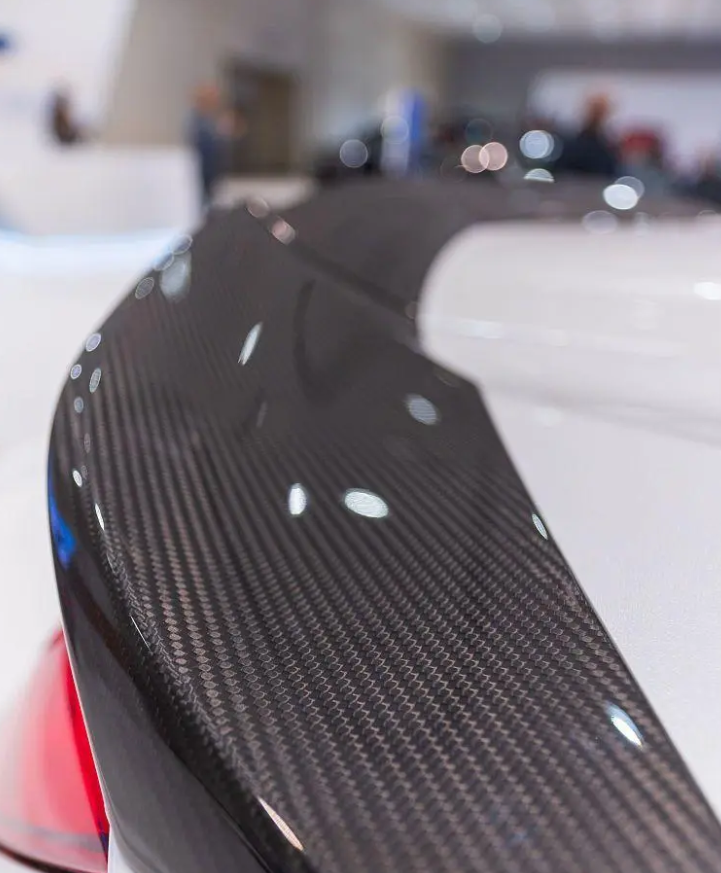
总之,随着碳纤维技术的不断发展,其在汽车制造业中的应用前景越来越广阔。相信在不久的将来,碳纤维将成为汽车制造业中的重要材料之一,为汽车功能主模型的应用和发展带来更多的可能性与突破。