航空发动机作为现代工业“皇冠上的明珠”,其性能突破高度依赖于材料科学的创新。在追求更高推重比、更低油耗和更长使用寿命的目标驱动下,全球航空材料领域正经历着革命性变革。本文将系统解析当前最具革命性的四类新材料体系,揭示其如何重塑航空发动机的技术边界。
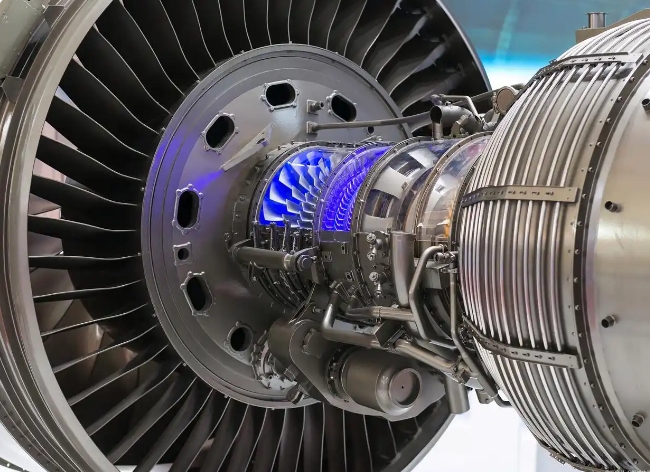
一、碳/碳复合材料:耐高温领域的颠覆者
碳/碳复合材料以碳纤维增强碳基体的独特结构,实现了密度低于2.0g/cm³且在1650℃以上仍能保持优异力学性能的突破。这种材料在1000-1300℃区间展现出反常的温度-强度正相关特性,成为涡轮导向叶片等热端部件的理想选择。其核心挑战在于400℃以上有氧环境中的氧化问题,当前采用纳米级涂层技术已实现1800℃环境下的长效防护。值得注意的是,C/C基复合材料在发动机尾喷管的应用已实现减重40%的同时,将工作温度提升至2200℃级别,为推重比15以上发动机的研制提供了物质基础。
二、高温合金:持续突破的性能边界
作为航空发动机的基石材料,高温合金已形成镍基、钴基、铁基三大体系。其中第四代单晶高温合金通过定向凝固技术,将承温能力提升至1100℃以上,较第二代材料提升50℃。粉末冶金工艺的应用解决了合金元素偏析难题,使涡轮盘用高温合金的疲劳寿命延长3倍。特别值得关注的是氧化物弥散强化(ODS)合金的突破,通过纳米级Y₂O₃颗粒的均匀分布,在1250℃下仍能保持600MPa的屈服强度,为燃烧室部件提供了革命性的材料解决方案。
三、陶瓷基复合材料(CMC):轻量化的终极答案
SiC纤维增强SiC基体复合材料(SiC/SiC)的出现,标志着航空发动机材料进入超高温时代。这种材料密度仅为镍基合金的1/3,却能在1650℃环境下保持结构稳定性,其断裂韧性较传统陶瓷提升两个数量级。自愈合陶瓷基复合材料(SHCMC)通过引入硼硅酸盐玻璃相,实现了高温氧化环境下的裂纹自主修复,在1200℃疲劳测试中寿命延长22倍。当前研发重点已转向SiC/SiC-B₄C多元体系,目标是在2000℃极端环境下实现稳定服役。
四、钛铝系金属间化合物:高温轻量化的新范式
针对600-800℃温区,TiAl和TiAlNb基合金展现出革命性的性能组合:密度4.0g/cm,较镍基合金降低30%,而1000小时蠕变强度保持率达85%。通过电子束选区熔化(EBSM)增材制造技术,已实现复杂空心叶片的一次成形,较传统锻造工艺减重25%。特别值得关注的是阻燃钛合金的突破,通过添加稀土元素铈,使材料在800℃下的燃速降低至0.1mm/min,为高压压气机提供了安全保障。
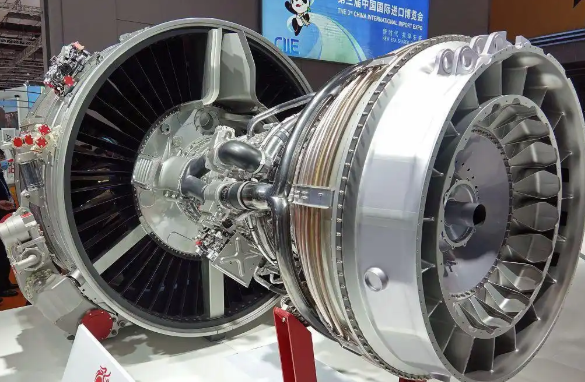
五、材料工艺融合:增材制造的赋能效应
3D打印技术正在重塑材料应用模式。激光粉末床熔融(LPBF)工艺实现了镍基高温合金晶粒结构的精准调控,在涡轮叶片制造中,通过逐层扫描策略优化,将热疲劳寿命提升40%。陶瓷基复合材料的立体光刻成型技术(SLA)已能制备直径500mm的燃烧室衬套,较传统工艺减重60%。更值得关注的是多材料梯度打印技术,实现了从钛合金到陶瓷基复合材料的平滑过渡,为整体式燃烧室设计开辟了新路径。
六、表面工程技术:性能跃升的关键增量
热障涂层(TBS)技术已发展至第三代稀土锆酸盐体系,在1300℃环境下热导率低至0.6W/m·K,较传统YSZ涂层降低40%。环境障涂层(EBC)通过硅基-铪基复合涂层设计,实现了对水氧腐蚀的双重防护,在模拟海洋环境下腐蚀速率降低至0.02mm/年。物理气相沉积(PVD)技术的突破,使涂层与基体的结合强度提升至70MPa,为高温部件提供了可靠防护。
当前航空发动机材料研发正呈现三大趋势:材料基因组技术加速新材料研发周期,多尺度计算模拟使合金设计效率提升5倍;智能材料系统集成温度自适应功能,通过形状记忆合金实现涡轮间隙的主动控制;生物启发的仿生结构设计,使复合材料抗冲击性能提升3倍。这些创新正在推动航空发动机向2500K级涡轮进口温度、20以上推重比的目标稳步迈进,为下一代高超声速飞行器奠定技术基础。