在航空领域,材料科学的每一次进步都深刻影响着飞行器的性能与可持续发展能力。近年来,先进热塑性复合材料(TPCs)凭借其独特的性能优势,正从传统热固性复合材料的"补充角色"跃升为航空结构设计的"核心选择"。这种转变不仅体现在材料用量的指数级增长——空客A350XWB的复合材料占比已达53%,波音787的碳纤维增强塑料(CFRP)使用量较上一代机型提升40%,更在于其颠覆性的制造工艺与全生命周期管理潜力。
一、材料性能的革命性突破
热塑性复合材料的核心优势源于其分子链结构特性。与热固性材料固化后不可逆的化学交联不同,TPCs的线性聚合物链在加热时可熔融重塑,这种特性赋予材料三大核心优势:
可修复性:通过局部加热,裂纹部位可重新熔合,修复时间较传统铆接工艺缩短40%;
可回收性:德国DLR实验室证实,采用超声波焊接的Z型纵梁部件回收率达70%,碳排放较铝合金部件降低42%;
加工效率:荷兰Fokker公司将CF/PPS焊接技术应用于湾流650公务机尾翼,成型周期较热固性材料缩短80%。
在极端环境适应性方面,TPCs展现出传统金属难以企及的性能。赛峰集团LEAP-3发动机的高压涡轮工作叶片采用碳化硅陶瓷基复合材料(CMCs),使热端部件耐受温度提升至1500°C,较镍基合金提高150°C,燃油消耗率降低3%。波音787-X验证机引入的石墨烯纳米增强复合材料,通过原子层沉积技术将石墨烯片层均匀分散于树脂基体,舱门结构在减重80千克的同时,拉伸强度提升18%。
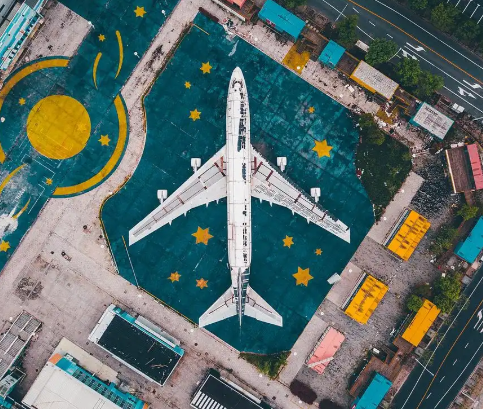
二、制造工艺的范式重构
热塑性复合材料的普及,催生了多项颠覆性制造技术:
连续纤维增强拉挤成型:北京化工大学开发的熔融拉挤工艺,实现50%纤维体积含量的高效渗透,较传统手糊工艺生产效率提升300%;
超声波焊接技术:德国弗劳恩霍夫协会在"多功能机身演示器(MFFD)"项目中,通过自动化定位系统将8米长的CFRP半壳连接,每个面重量和成本节省10%;
原位聚合工艺:瑞士EMS公司采用PA12反应注射技术,在精确控制温度与压力的条件下,解决高粘度树脂浸渍难题,纤维分布均匀性提升40%。
这些工艺突破不仅体现在实验室阶段。空客A320机型的热塑性复材用量已达50%-60%,其机身部件采用连续碳纤维增强PEEK预浸带制造,较传统铝合金结构减重30%。在军用领域,洛克希德·马丁公司的"暗星"高超声速侦察机,要求材料在马赫数6的飞行条件下耐受1500°C高温,陶瓷基复合材料(CMCs)因此成为核心解决方案。
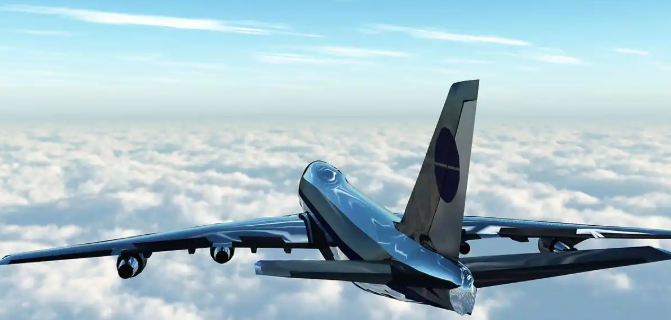
三、全生命周期的绿色闭环
热塑性复合材料的环保优势贯穿设计、制造到回收的全周期:
原料端:江苏长海复合材料股份有限公司开发的玻纤增强热塑复合材料,以30%亚麻纤维替代碳纤维用于客舱隔板,碳足迹降低55%的同时,天然纤维的吸声特性使客舱噪音下降2分贝;
制造端:激光粉末床熔融(LPBF)技术制造镍基高温合金复杂冷却结构,通用电气采用该技术使燃烧室冷却效率提升25%,材料用量减少40%;
回收端:波音公司南卡罗来纳州工厂的自动化回收线,将退役部件的碳纤维回收率提升至92%,再生纤维拉伸强度保持率达95%,已用于次级结构部件制造。
这种闭环模式正在重塑航空产业的成本结构。普惠公司开发的金属粉末循环利用技术,通过真空蒸馏与等离子体提纯工艺,使3D打印剩余的钛合金粉末杂质含量低于0.005%,实现10次以上重复利用,材料成本降低45%。
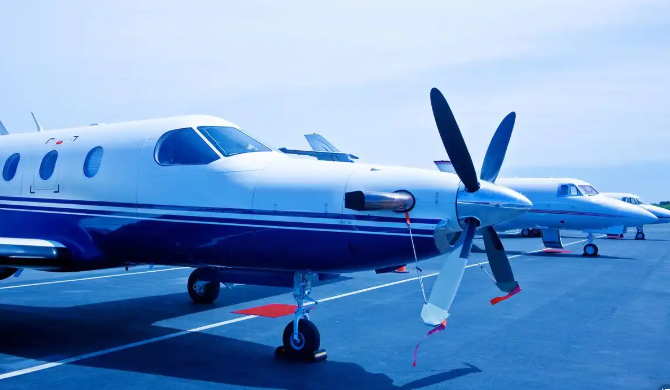
四、未来技术的多维演进
当前研究正从三个方向突破材料极限:
纳米工程化:德国巴斯夫开发的石墨烯增强环氧树脂,通过原位聚合工艺实现纳米片层均匀分散,导热系数提升300%;
自修复体系:3M公司推出的微胶囊型自修复复合材料,当裂纹扩展至0.3毫米时,内置的氰基丙烯酸酯修复剂可在24小时内完成损伤自愈,疲劳寿命延长22%;
多材料集成:德国EOS公司的M400-4X设备实现Inconel 718高温合金与氧化铝陶瓷同步打印,为复杂热防护系统提供解决方案。
人工智能与量子计算的融入,正在加速材料研发进程。DeepMind开发的GraphNet算法,通过分析超过1200万组材料数据集,建立合金成分-微观结构-力学性能的多维度预测模型,将新型镍基高温合金的研发周期从5年缩短至18个月。IBM的量子计算团队则通过量子蒙特卡洛模拟,成功解析石墨烯-碳纤维界面的范德华力作用机制,为设计界面结合强度超过80MPa的下一代复合材料提供理论依据。
站在2025年的技术节点回望,热塑性复合材料已从"高端替代"走向"主流应用",从结构减重走向功能集成,从线性制造走向循环再生。当碳纤维复合材料在飞机结构中的用量突破50%,当陶瓷基复合材料使发动机热效率突破60%,当增材制造实现"设计即制造"的一体化流程,材料科学正成为驱动航空产业变革的底层逻辑。正如NASA材料研究中心主任Dr.Emily Zhou所言:"在航空航天领域,材料的极限即是人类探索的边界。当我们学会在原子尺度上操纵物质,天空将不再是技术的终点,而是新边疆的起点。"