在船舶制造业中,玻璃钢(也称为玻璃纤维增强塑料,GFRP)因其轻质高强、耐腐蚀、易成型等特性,逐渐成为制造小型到中型船舶的首选材料。而真空导入成型(Vacuum Infusion Molding, VIM)工艺,作为玻璃钢船舶制造中的一项关键技术,更是以其高效、环保、成本效益高等优点,引领了玻璃钢船舶制造技术的革新。
真空导入成型工艺的基本原理
真空导入成型工艺是一种结合了树脂传递模塑(RTM)和真空袋成型技术的先进制造工艺。其基本原理是,在模具内铺设好预先裁剪好的玻璃纤维布或毡,然后注入含有催化剂和固化剂的树脂体系。通过真空泵产生的负压,树脂被均匀地吸入模具内的纤维结构中,并在真空状态下完成固化,形成具有高强度和良好表面质量的玻璃钢制品。
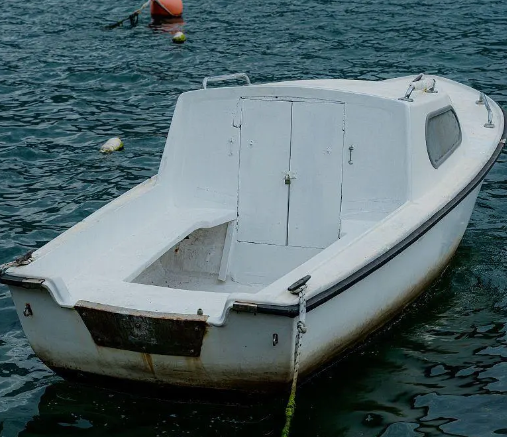
技术创新点
-
高效节能:真空导入成型工艺利用真空负压驱动树脂流动,无需外部压力设备,大大节省了能源消耗。同时,由于树脂在真空状态下固化,减少了气泡和空隙的产生,提高了制品的密实度和强度。
-
环保低污染:相比传统的手糊或喷射成型工艺,真空导入成型减少了树脂的挥发和浪费,降低了有害气体的排放,更加符合现代制造业的环保要求。
-
成本效益:虽然初期模具和设备投资较高,但真空导入成型工艺能够实现大规模生产,且制品质量稳定,减少了废品率和返工成本。长期来看,该工艺具有更高的成本效益。
-
设计灵活性:真空导入成型工艺适用于复杂形状和结构的制品制造,为玻璃钢船舶的设计提供了更大的自由度。设计师可以创造出更加流线型、美观且功能性的船体结构。
-
质量控制:通过精确控制树脂的注入量和固化条件,真空导入成型工艺能够确保制品的一致性和可靠性,提高了玻璃钢船舶的整体性能。
应用前景与挑战
随着玻璃钢船舶市场的不断扩大和技术的不断进步,真空导入成型工艺的应用前景十分广阔。特别是在游艇、快艇、渔船等小型到中型船舶领域,该工艺已成为主流制造技术之一。然而,面对日益严格的环保法规和市场对高性能船舶的需求,如何进一步优化工艺参数、提高生产效率、降低成本,以及开发更加环保、高性能的树脂体系,仍是当前玻璃钢船舶制造业面临的重要挑战。
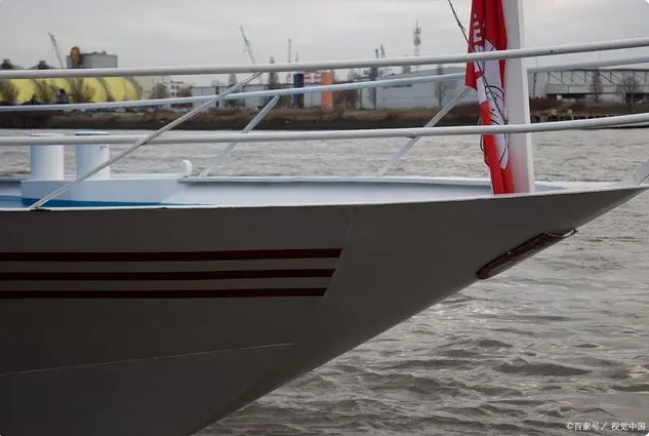
玻璃钢船舶的真空导入成型工艺以其独特的优势和创新性,为船舶制造业带来了革命性的变化。未来,随着技术的不断发展和完善,该工艺将在玻璃钢船舶制造领域发挥更加重要的作用。