在碳纤维复合材料领域,编织与纺织工艺作为两种核心制造技术,对预浸料的性能表现产生着根本性影响。这两种工艺在纤维排列方式、结构特性及最终应用场景上均呈现出显著差异,其技术路线选择直接关系到复合材料制品的力学性能、热稳定性及工艺适配性。本文将从工艺原理、性能参数、应用场景三个维度展开对比分析,揭示两种技术路线的核心特征与发展趋势。
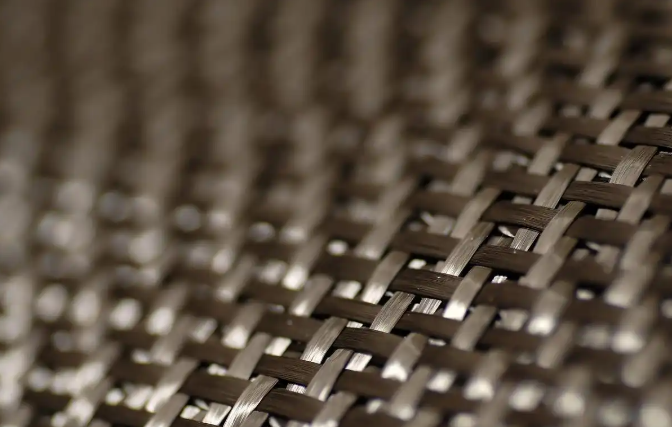
一、工艺特性与结构差异
编织工艺通过经纬向纤维的交织形成特定纹理结构,其典型代表包括平纹、斜纹与缎纹组织。这种工艺能够构建三维多向纤维架构,如1×1、1×2、1×3编织结构,实现纤维在空间中的多轴向分布。以三维五向编织为例,通过在轴向加入非编织增强纤维,可使复合材料的拉伸强度提升20%,初始模量与二次模量实现翻倍增长。这种结构特性使得编织工艺在承受复杂应力载荷时表现出色,其纤维体积比可达60%以上,表面编织角控制精度直接影响材料的力学各向异性。
纺织工艺则采用机织、针织或无纺布形式,形成更为均匀的纤维分布网络。真空袋工艺作为典型代表,通过抽真空加压实现树脂的均匀渗透,其树脂流动度控制精度可达±3%。在航空级预浸料制备中,热熔两步法已成为主流工艺,通过树脂膜制备与预浸处理,可实现树脂含量偏差低于0.8%的精密控制。这种工艺更适合制造大面积曲面结构,如飞机机翼蒙皮与卫星承力筒,其孔隙率控制能力尤为突出。
二、核心性能参数对比
在拉伸性能维度,编织工艺展现显著优势。三维五向编织复合材料在(0/90°)方向拉伸测试中,缎纹结构初始模量可达22.3GPa,较平纹结构提升近100%。而纺织工艺在(±45°)方向剪切性能上表现更优,平纹复合材料面内剪切破坏载荷较编织结构高15%-20%。这种差异源于纤维排列方式的本质区别:编织工艺的交织结构增强了纤维间的机械互锁,而纺织工艺的均匀分布特性有利于应力在更大范围内的分散。
热稳定性方面,编织工艺的立体结构赋予其更优的高温性能。碳-碳复合材料在2760℃极端温度下仍能保持结构完整性,其热膨胀系数较金属材料低80%。纺织工艺则通过树脂基体改性提升耐温性,如环氧树脂体系在150℃环境下仍能维持80%的原始强度。值得注意的是,编织结构在热循环测试中表现出更小的尺寸变化率,这对需要经受剧烈温度变化的航天器部件尤为重要。
在工艺适配性上,编织工艺的设备复杂度较高,三维编织机价格是传统纺织设备的3-5倍,且单件生产周期较长。纺织工艺则具有更高的生产效率,真空袋工艺可实现每小时3-5平方米的预浸料制备速度,更适合大规模工业化生产。这种差异导致编织工艺更多应用于高端军工领域,而纺织工艺在民用航空与汽车工业中占据主导地位。
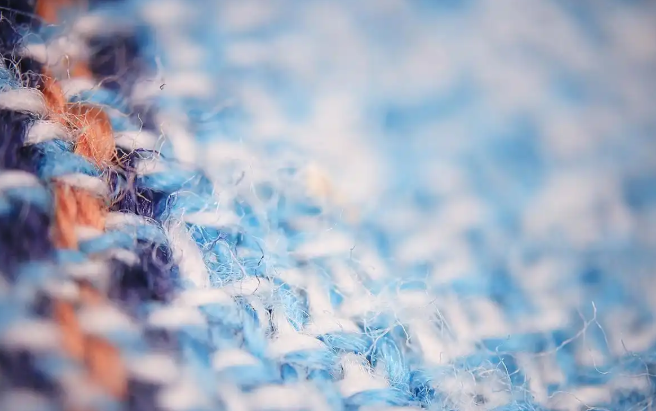
三、典型应用场景分析
在航空航天领域,编织工艺的三维整体成型特性使其成为导弹弹体结构的首选方案。某型高超音速导弹采用碳纤维增强环氧树脂预浸料,通过1×1×2/5F编织结构实现弹体减重30%的同时,抗冲击性能提升25%。而纺织工艺在卫星结构件制造中表现卓越,国际空间站的蜂窝面板采用真空袋工艺制备,其孔隙率控制在0.3%以下,有效提升了材料的空间辐射耐受性。
汽车工业的应用呈现差异化特征:编织工艺在传动轴等轴向受力部件中实现突破,某型电动车采用干式碳纤维传动轴,较铝合金部件减重42%,扭矩传递效率提升18%。纺织工艺则主导车身覆盖件市场,宝马i3的碳纤维增强塑料(CFRP)乘客舱通过机织预浸料制造,在保证安全性的前提下实现车身减重50%。
四、技术挑战与发展趋势
当前两种工艺均面临关键材料依赖的瓶颈。航空航天级碳纤维的全球产能集中于日本东丽、美国赫氏等少数企业,供应链安全已成为行业痛点。在工艺创新方面,混合制造技术展现出巨大潜力,通过外层编织增强与内层纺织均匀化的复合结构,可在保持轻量化的同时提升损伤容限。某型无人机机翼采用该技术后,疲劳寿命延长至传统结构的2.3倍。
界面改性技术的突破正在重塑工艺边界。采用聚乙烯亚胺(PEI)接枝处理的碳纤维,其与环氧树脂的界面剪切强度提升38.9%,弯曲强度提升36.7%。这种分子级设计为两种工艺的性能优化提供了新路径,预示着未来碳纤维预浸料将向更高维度、更精细节点的方向发展。
这场工艺革命的本质,在于对碳纤维性能潜力的深度挖掘。当编织工艺的立体架构遇上纺织工艺的精密控制,碳纤维复合材料正在突破传统材料的物理极限,为从深空探测器到新能源汽车的各类装备注入革命性性能提升。随着多尺度调控技术与智能化制造的深度融合,碳纤维预浸料的性能边界将持续扩展,引领材料科学进入全新发展阶段。