在全球资源约束趋紧与碳中和目标双重压力下,热塑性纤维复合材料(TPFC)正以独特的可循环特性重塑材料工业格局。这种兼具高性能与可重塑性的新型材料,通过分子链的物理交联实现"使用-回收-再利用"的闭环循环,为航空、汽车、风电等高耗能产业提供了绿色转型的技术路径。从波音777的客舱内饰到大众ID.3的电池箱体,TPFC的产业化应用正在构建循环经济的物质基础,其技术突破与模式创新深刻影响着全球制造业的可持续发展进程。
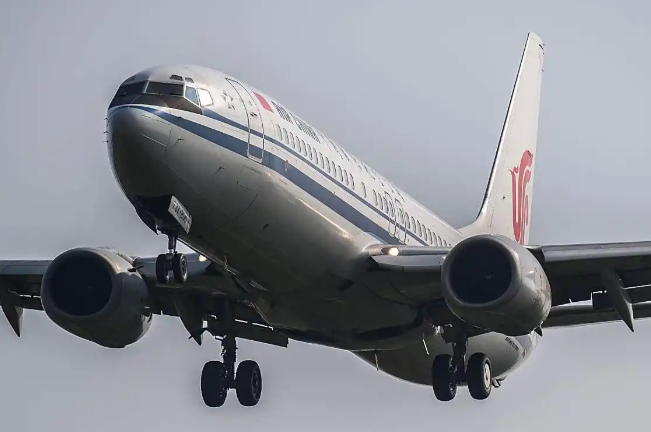
一、材料特性:循环经济的物质基础
热塑性纤维复合材料的核心优势源于其可逆的物理交联特性。与热固性树脂的化学交联不同,TPFC的聚醚醚酮(PEEK)、聚苯硫醚(PPS)等基体在加热条件下可反复熔融重塑,这种特性使其具备98%以上的理论回收率。德国弗劳恩霍夫研究所的研究显示,采用连续纤维增强热塑性复合材料(CFRTP)的汽车部件,在报废后可通过热压成型实现100%材料再利用,较传统金属材料节省83%的能源消耗。更关键的是,TPFC的加工温度窗口宽(260-350℃),允许在注塑、挤出等常规塑料工艺中直接成型,设备改造成本较热固性工艺降低60%。
在性能维度,TPFC展现出惊人的材料潜力。碳纤维增强PEEK复合材料的比强度达350MPa/(g/cm³),较铝合金高4倍;玻璃纤维增强PPS在150℃环境下的蠕变性能优于钛合金。这种"轻量化-高强度-耐高温"的组合特性,使其在替代金属材料时既能保证结构性能,又能实现30-50%的减重效果。挪威风电巨头Equinor的实证数据显示,采用TPFC叶片的5MW风机年发电量增加12%,全生命周期碳排放减少40%。
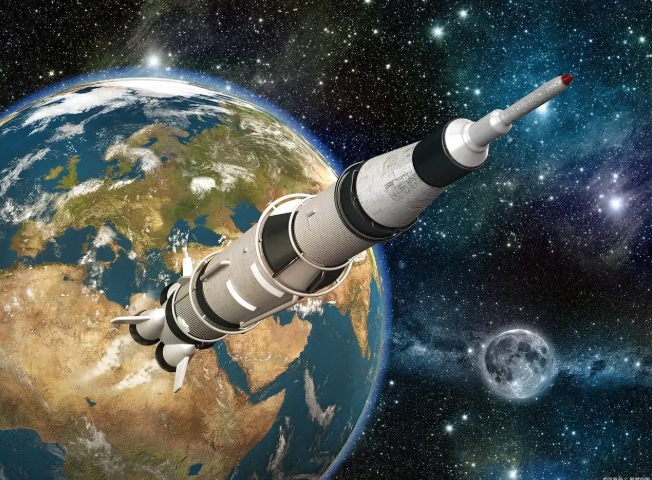
二、应用突破:从实验室到产业化的跨越
在航空航天领域,TPFC的产业化应用取得里程碑式进展。空客A350的货舱地板采用碳纤维增强PEI材料,较传统铝材减重42%,且在200℃环境下仍保持90%的原始强度。更激进的"热塑性翼盒"项目验证了超大型结构的整体成型能力,其25米长的碳纤维翼梁在热压罐中一次成型,加工周期从72小时缩短至8小时。这种技术突破使单架飞机减重2.3吨,对应每年减少1200吨二氧化碳排放。
汽车工业的转型更具革命性。宝马i3的碳纤维增强塑料(CFRP)乘客舱采用注塑工艺,将生产节拍从120分钟压缩至8分钟,成本降低35%。更先进的"热塑性电池箱体"技术,通过玻璃纤维增强PPS实现与金属箱体等效的碰撞安全性,同时重量减轻58%。这种材料革新使电动车续航里程提升15%,充电循环次数增加2000次,全生命周期成本降低23%。
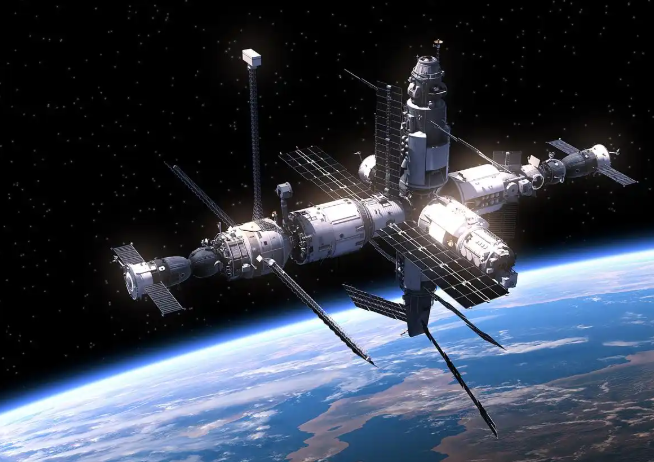
三、回收体系:构建闭环经济的关键环节
热塑性复合材料的回收技术已形成物理法与化学法两大技术路线。物理回收通过粉碎-熔融-挤出工艺,可将报废部件转化为再生粒料,其性能保持率达85%以上。荷兰Thermoplast复合材料公司的实证数据显示,再生TPFC在汽车内饰件中的应用,较原生材料成本降低40%,碳排放减少72%。化学回收则通过溶剂解或热解技术实现纤维与基体的分离,德国CARBIORE项目成功将回收碳纤维的强度保持率提升至92%,且纤维长度可控在50-200mm区间。
在标准建设层面,ISO 20763:2019《热塑性复合材料回收规范》的出台,为材料认证与流通提供了技术依据。欧盟"循环经济行动计划"更将TPFC纳入关键原材料清单,要求2030年前实现85%的回收利用率。这种政策驱动使全球TPFC回收市场规模预计在2025年达到120亿美元,年复合增长率达18.7%。
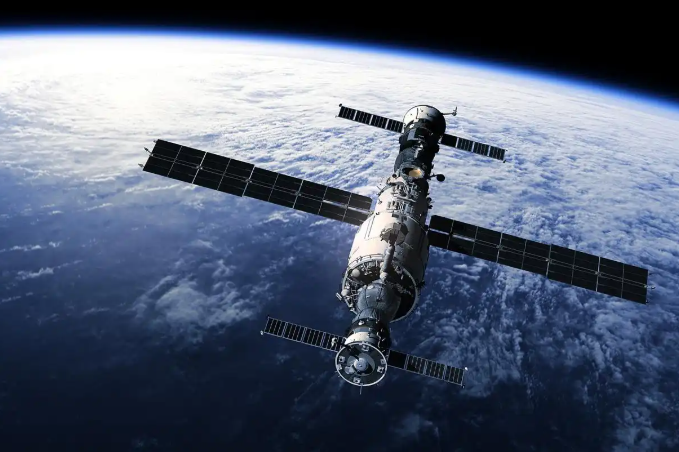
四、产业化挑战与未来趋势
当前TPFC的规模化应用仍面临三重瓶颈。原材料成本方面,碳纤维增强PEEK的价格是玻璃钢的12倍,限制了其在大众消费品中的普及。设备投资方面,热塑性预浸机价格是传统热固性设备的3-5倍,且需要配套超高温成型系统。更关键的是标准缺失,全球尚未形成统一的TPFC回收等级划分体系,导致再生材料市场流通受阻。
技术创新正在突破这些限制。连续纤维3D打印技术使复杂结构的一次成型成为可能,其加工精度达0.1mm,较传统模压工艺提升50%。纳米改性技术通过石墨烯掺杂,使PPS基体的热导率提升至5W/(m·K),较原生材料提高20倍。更前沿的"自修复TPFC"通过微胶囊技术实现裂纹自动愈合,使材料使用寿命延长至传统材料的3倍。
这场材料革命的本质,在于重构制造业的价值链。当TPFC与物联网、人工智能深度融合,未来的智能工厂将实现"设计-生产-回收"的全流程数字化管理。从可重复使用的火箭整流罩到可降解的风电叶片,热塑性复合材料正在书写循环经济的工业诗篇,其技术突破与模式创新,将为全球制造业的绿色转型提供决定性支撑。