在船舶制造业中,玻璃钢(玻璃纤维增强塑料,简称GFRP)作为一种轻质、高强度、耐腐蚀的材料,已广泛应用于各类船舶的建造。随着技术的不断进步,玻璃钢船舶的制造工艺也在不断创新,其中真空导入成型工艺(Vacuum Infusion Process, VIP)凭借其高效、环保、质量可控等优势,逐渐成为玻璃钢船舶制造领域的一项关键技术。本文将深入解析玻璃钢船舶制造中真空导入成型工艺技术的创新点及其在实际应用中的优势。
真空导入成型工艺概述
真空导入成型工艺是一种结合了复合材料成型与真空技术的先进制造工艺。它通过在模具内部铺设预浸渍的玻璃纤维布或毡,并注入树脂,然后在模具外部施加真空,利用真空产生的负压将树脂均匀渗透到玻璃纤维中,完成固化成型。该工艺不仅实现了树脂与玻璃纤维的充分浸润,还大大减少了气泡和空隙的产生,提高了产品的整体强度和耐久性。
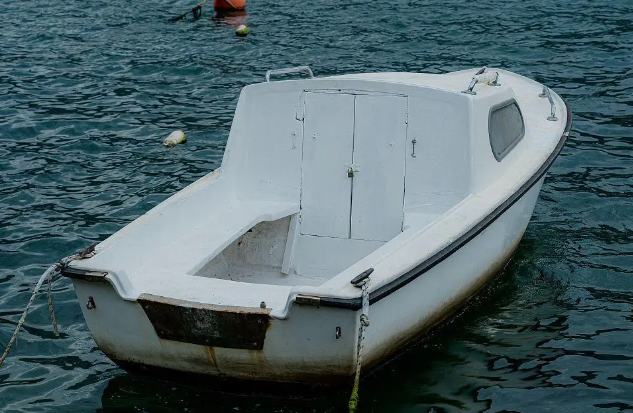
创新点解析
-
精准控制树脂用量:真空导入成型工艺通过精确计算树脂的用量,并在注入过程中严格控制,避免了传统手工糊制过程中树脂的浪费和过量使用,既降低了成本,又减少了环境污染。
-
提高产品质量:由于真空导入成型工艺能够确保树脂均匀渗透到玻璃纤维中,且避免了气泡和空隙的产生,因此制得的玻璃钢船舶具有更高的强度和更好的耐腐蚀性,延长了船舶的使用寿命。
-
实现复杂结构制造:真空导入成型工艺能够轻松应对复杂形状的模具,使得玻璃钢船舶的设计更加灵活多样,满足了不同用户对船舶外观和性能的需求。
-
环保节能:该工艺在树脂注入和固化过程中无需加热,减少了能源消耗,同时,由于树脂用量的精准控制,也减少了有害气体的排放,符合绿色制造的理念。
应用优势
-
提高生产效率:真空导入成型工艺实现了自动化生产,大大提高了生产效率,缩短了船舶的制造周期。
-
降低成本:通过精准控制树脂用量和减少浪费,以及提高产品质量和延长使用寿命,真空导入成型工艺有助于降低玻璃钢船舶的制造成本。
-
增强市场竞争力:采用真空导入成型工艺制造的玻璃钢船舶,凭借其优异的性能和环保特性,在市场上更具竞争力,能够满足用户对高性能、环保型船舶的需求。
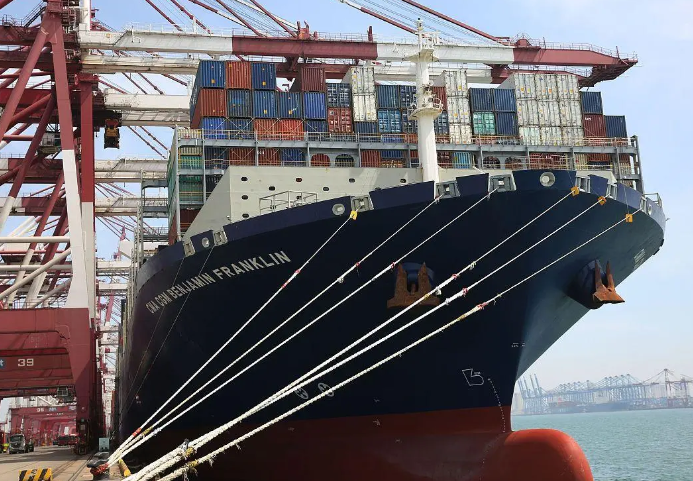