一、变形原因分析
树脂与硬化剂混合比例不当
树脂与硬化剂的混合比例是影响玻璃钢制品质量的关键因素之一。比例不当会导致树脂固化不完全或过快,产生内部应力,使模具表面在固化过程中发生变形。
固化温度控制不当
固化温度对树脂的固化过程至关重要。温度过高会导致树脂过快固化,产生内部应力;温度过低则会导致固化不充分,制品软弱易变形。
压力分布不均匀
在层压过程中,压力的均匀分布对避免变形至关重要。如果某些区域受到的压力大于其他区域,树脂流动会不均匀,从而在固化过程中形成内部应力和变形。
模具设计与制作质量不佳
模具的设计和质量直接影响玻璃钢产品的最终形状和质量。设计不当或制作质量差的模具无法承受固化过程中的温度和压力,导致制品在制作过程中发生变形。
材料质量低劣
树脂和玻璃纤维的质量直接影响玻璃钢制品的性能。低质量的材料可能含有杂质或不均匀,导致固化过程中的不均匀性,进而引发变形。
固化时间不足
固化时间不足会导致产品未完全固化就被移出模具,从而在后续处理和使用过程中发生变形。
后固化处理不当
后固化是玻璃钢制品制作过程中的重要环节,但处理不当,如温度控制不精确、时间把握不准或环境湿度未达标准,都可能使已初步固化的制品在后续阶段因残余应力释放不均而再度变形。
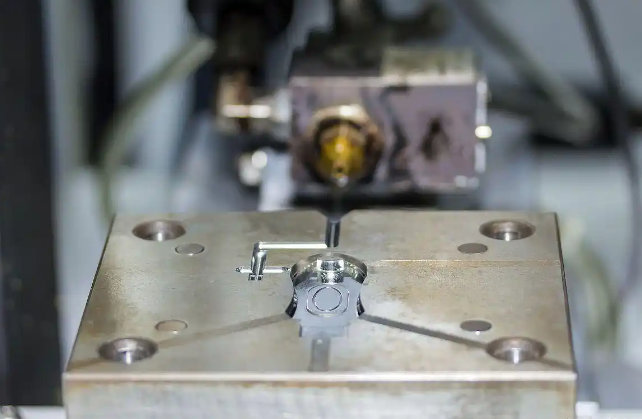
精确控制树脂与硬化剂比例
严格按照制造商推荐的混合比例进行树脂与硬化剂的混合,确保固化过程均匀且完全。
精确控制固化温度
选择适宜的固化温度,并严格控制温度波动,使用高精度温控设备,确保固化过程稳定。
优化压力分布
确保层压过程中压力的均匀分布,通过调整压力设备和模具设计,使压力在各个区域均匀分布。
优化模具设计与制作质量
加强模具结构,提高模具的强度和刚度,确保模具能够承受固化过程中的温度和压力。同时,优化模具设计,减少分型面,保证合缝严密。
选择高质量材料
选择高质量、经过质量检验的树脂和玻璃纤维,确保材料均匀、无杂质,减少固化过程中的不均匀性。
确保充足的固化时间
遵循制造商推荐的固化时间,并使用计时器或其他监控设备确保固化时间的准确性。
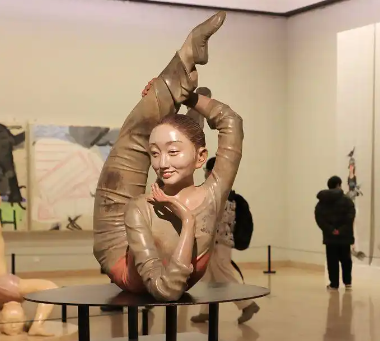
优化后固化处理
精确控制后固化温度和时间,确保环境湿度达到标准。在高温后固化过程中,确保模具内无承重,由模具支撑部件以防自身重量造成变形。同时,在最初固化三天内进行后固化处理,以达到最佳效果。
通过上述优化解决方案,可以有效减少玻璃钢模具表面变形的风险,提高产品的质量和性能。在实际操作中,应根据具体情况进行灵活调整,并结合科学分析、合理设计、严格管理以及技术创新,从根本上解决这一问题,推动复合材料制造行业向更高质量、更高效率的方向发展。