在智能制造浪潮的席卷下,复合材料制造领域正经历从传统工艺向数字化、智能化转型的关键阶段。碳纤维缠绕-注塑一体化技术作为典型代表,将高强度碳纤维的力学优势与注塑工艺的精密成型能力深度融合,在航空航天、汽车轻量化、机器人结构件等领域展现出巨大潜力。然而,这一技术的推广应用高度依赖掌握跨学科技能的复合型人才,而现有操作工培养体系与产业需求之间的脱节,已成为制约行业发展的瓶颈。本文从技术融合特征出发,探讨如何构建适配碳纤维缠绕-注塑一体化装备的操作工培养体系。
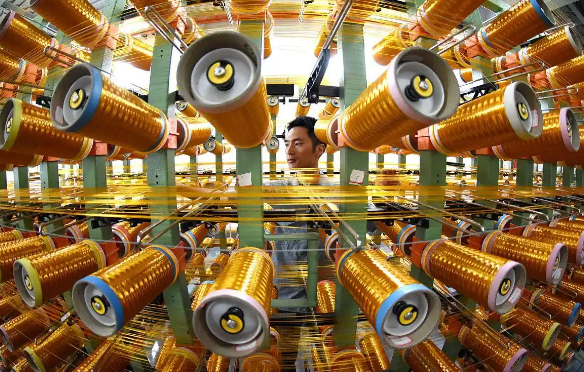
一、技术融合特征与人才需求
碳纤维缠绕-注塑一体化技术涉及纤维缠绕、树脂传递、注塑成型三大核心环节。纤维缠绕工艺通过精确控制纤维角度和张力,实现结构件的定向增强;注塑工艺则通过高温高压将热塑性树脂注入模具,完成复杂形状的填充与固化。该技术要求操作工同时掌握材料力学、热力学、自动化控制等多领域知识。例如,在机器人机械臂制造中,需通过缠绕工艺实现碳纤维的轻量化承载设计,再利用注塑工艺完成关节部位的精密成型,操作工需具备实时调整纤维张力、优化注塑参数的能力。
二、现有培养体系的三大短板
知识体系碎片化
传统培养模式将缠绕、注塑工艺割裂教学,导致操作工缺乏跨工艺协同意识。例如,某院校实验数据显示,仅接受单一工艺培训的操作工在处理缠绕-注塑复合结构时,产品合格率比接受融合培训者低28%。
实操场景脱离生产
现有实训设备多为单机模拟器,无法还原真实产线的纤维张力波动、树脂流动不均等复杂工况。某企业调研显示,新员工在真实产线上的调试周期平均长达3个月,设备损耗成本增加40%。
智能制造要求操作工掌握PLC编程、传感器数据采集、AI算法优化等技能。但调查显示,仅12%的操作工能独立完成缠绕路径的智能规划,注塑工艺参数的机器学习优化能力更是普遍缺失。
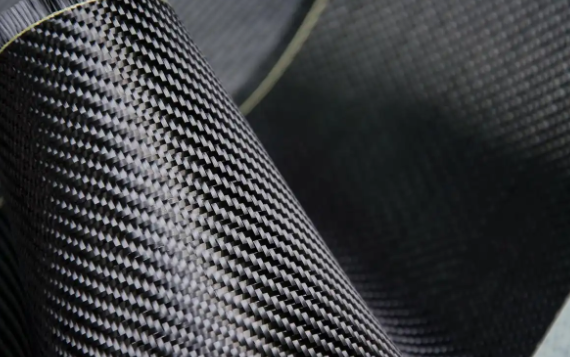
三、培养体系重构路径
(一)构建“双螺旋”课程体系
以“材料-工艺”为纵向主轴,设置《碳纤维复合材料学》《热塑性树脂流变学》等课程;以“智能-制造”为横向主轴,开设《工业机器人编程》《数字孪生技术》等模块。例如,在教授缠绕工艺时,同步引入纤维角度对注塑流动影响的仿真实验,使学生理解工艺参数的耦合关系。
(二)搭建虚实融合实训平台
虚拟仿真层
开发包含缠绕张力控制、注塑熔体前沿预测等功能的数字孪生系统,支持操作工在虚拟环境中完成工艺参数优化。某平台测试显示,通过虚拟调试可将实际产线调试时间缩短60%。
物理实训层
配置具备张力传感器、视觉检测系统的真实产线,设置纤维断裂预警、注塑缺陷诊断等典型故障场景。例如,通过压力传感器实时监测缠绕过程中的纤维张力波动,培养操作工的异常处理能力。
(三)实施“三阶段”能力进阶
基础技能阶段
通过缠绕张力标定、注塑温度梯度控制等标准化实验,掌握设备操作规范。例如,要求学员在规定时间内完成特定角度的纤维缠绕,并确保张力误差不超过±5%。
工艺融合阶段
开展缠绕-注塑复合结构件设计项目,如机器人关节外壳的轻量化设计。学员需完成纤维铺层优化、注塑模具设计、缺陷预测等全流程任务,考核指标包括结构强度达标率、生产效率提升率。
智能运维阶段
引入AI算法优化课程,要求学员通过机器学习模型预测树脂固化时间、优化缠绕路径。例如,某教学案例中,学员通过训练神经网络模型,将注塑缺陷率从8%降至2.3%。
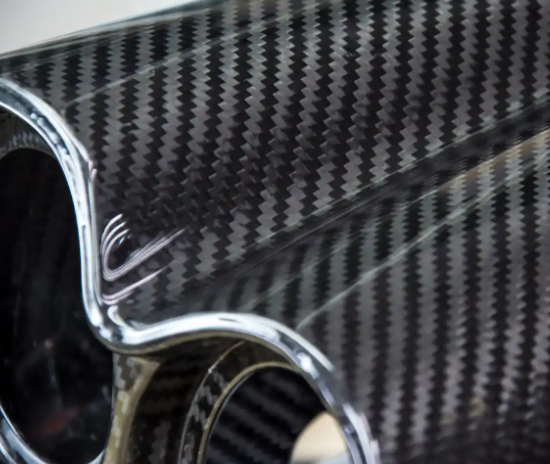
四、质量评估与持续改进
建立“三维评估模型”:
知识维度:通过在线测试评估材料性能、工艺参数等理论掌握度;
技能维度:利用虚拟仿真系统考核工艺协同操作能力;
创新维度:以项目答辩形式评估缺陷诊断、工艺优化等创新能力。
根据评估结果动态调整课程权重,例如,若某批次学员在缠绕-注塑接口强度控制上得分偏低,则增加该模块的实训课时。
结语
碳纤维缠绕-注塑一体化技术的推广,本质是智能制造范式在复合材料领域的具象化。通过构建“双螺旋”课程体系、搭建虚实融合实训平台、实施“三阶段”能力进阶,可系统性提升操作工的跨工艺协同能力与数字素养。这一培养体系的落地,不仅能为行业输送适配智能制造需求的复合型人才,更将推动复合材料制造从“经验驱动”向“数据驱动”的范式跃迁,为高端装备制造提供核心支撑。