在全球能源结构深度转型的浪潮中,风电产业正以每年18%的装机增速重塑清洁能源版图。当叶片直径突破130米、单机功率迈向20兆瓦级,传统玻璃纤维材料在强度、重量与成本之间的矛盾愈发尖锐。在此背景下,碳纤维复合材料凭借其独特的力学性能与轻量化优势,成为推动风电产业迈向“更大、更轻、更高效”的核心驱动力,一场由材料革命引发的产业升级正在悄然展开。
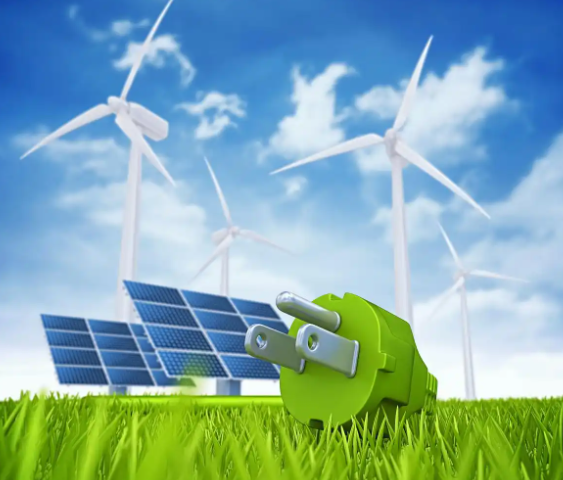
一、材料特性重构叶片设计范式
碳纤维复合材料的性能突破为叶片设计打开了全新维度。其密度仅为钢材的1/4,但拉伸强度可达3500MPa以上,较玻璃纤维提升3倍,这种“以柔克刚”的特性使叶片在保持结构刚性的同时,重量减轻30%-40%。以某122米叶片为例,采用碳纤维主梁后,整体重量从58吨降至42吨,风能捕获效率提升12%,年发电量增加300万千瓦时。更关键的是,碳纤维的疲劳强度达到抗拉强度的70%-80%,在20年设计寿命周期内,可承受超10亿次交变载荷,使叶片断裂风险降低85%。这种性能跃迁不仅延长了设备寿命,更使深远海风电项目的运维成本下降40%。
二、制造工艺突破推动成本下行
技术迭代正在重塑碳纤维的经济性曲线。拉挤成型工艺的成熟使碳纤维主梁的生产效率提升5倍,材料利用率从65%提高至92%。通过干喷湿纺48K大丝束技术,碳纤维生产成本从2018年的20美元/公斤降至2025年的12美元/公斤,逼近玻璃纤维的1.5倍价格区间。某研究机构开发的碳玻混杂增强技术,在叶片前缘等关键部位采用碳纤维,非承力区使用玻璃纤维,使综合成本降低25%,同时保持90%的碳纤维性能优势。这种“精准用材”策略使100米级叶片的碳纤维用量占比从70%降至45%,推动行业进入规模化应用临界点。
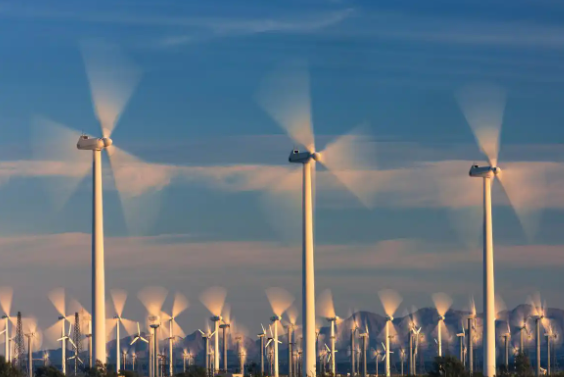
三、系统级优化释放产业价值
碳纤维的轻量化效应在整机层面产生链式反应。叶片减重使塔筒高度可增加20%,捕获更高空域优质风能,发电效率提升8%-10%。某131米陆上风电项目数据显示,采用碳纤维叶片后,塔筒直径从4.8米缩减至4.2米,基础混凝土用量减少15%,整体LCOE(平准化度电成本)下降0.03元/千瓦时。在深远海领域,碳纤维叶片的抗腐蚀性能使运维周期从6个月延长至18个月,结合漂浮式平台技术,使海上风电开发水深突破60米,可开发资源量增加3倍。这种从部件到系统的全面优化,正推动风电产业从“千瓦时成本竞争”转向“全生命周期价值创造”。
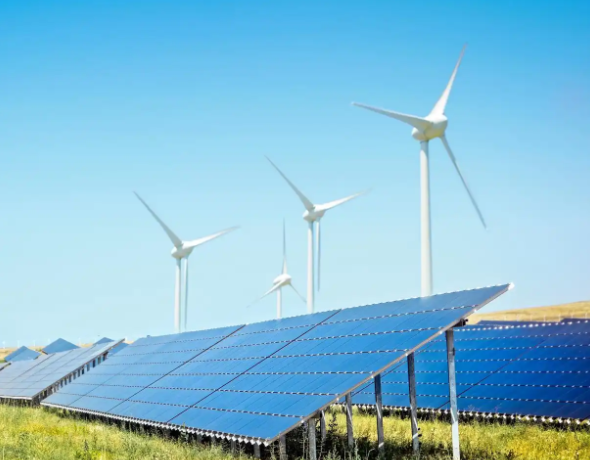
四、技术融合催生产业新形态
碳纤维与智能技术的融合正在创造新的产业形态。嵌入光纤传感器的碳纤维叶片可实时监测3000余个应力点,结合数字孪生系统实现叶片健康度预测,故障预警准确率达95%。某15兆瓦海上机组通过碳纤维-钛合金复合主轴设计,将传动链重量降低40%,配合智能偏航系统,使风能利用率提升至52%。更值得关注的是,碳纤维叶片的回收技术取得突破,通过热解工艺可回收90%的碳纤维,用于制造汽车零部件或储能设备,构建起“材料-产品-再生”的循环经济链条。
当碳纤维的轻量化革命与风电产业深度耦合,一场跨越材料科学、制造工艺与能源系统的变革正在发生。从陆地到海洋,从千瓦级到兆瓦级,碳纤维不仅重新定义了叶片的性能边界,更在推动风电产业向“更高发电效率、更低度电成本、更优环境效益”的方向进化。随着碳纤维产能突破25万吨/年,成本持续下探,以及材料基因工程、智能制造等技术的赋能,风电产业将真正迈入“叶片即能源载体”的新纪元,为全球能源转型注入澎湃动力。