随着全球海上风电装机规模突破60GW并向深远海区域延伸,极端海洋环境对装备可靠性的挑战日益凸显。在离岸50公里以上的海域,盐雾浓度可达内陆环境的50倍以上,叠加台风、潮汐及生物附着等多重侵蚀因素,传统风电叶片材料已难以满足全生命周期需求。在此背景下,抗盐雾腐蚀涂层与碳纤维主梁的集成设计技术,正成为破解海上风电装备耐久性难题的核心方案。
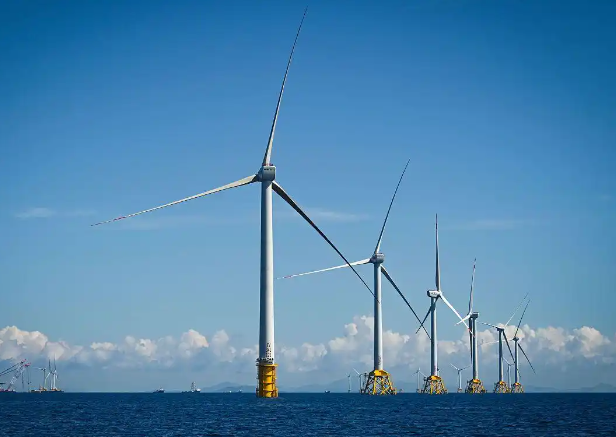
一、碳纤维主梁:轻量化与高强度的双重突破
碳纤维复合材料凭借其比强度是玻璃纤维2倍、比模量达3倍的力学优势,成为海上风电叶片主梁的理想材料。在120米级超大型叶片中,采用碳纤维主梁可使结构减重25%-30%,同时将叶根弯矩降低18%,显著减轻对塔筒和基础的载荷压力。通过拉挤成型工艺制备的碳纤维主梁,其层间剪切强度突破80MPa,疲劳寿命超过10⁷次循环,较传统玻璃纤维结构提升3倍以上。
在结构设计层面,碳纤维主梁的弯扭耦合特性可优化叶片气动性能。某型号13.6MW叶片采用碳纤维主梁后,其空气动力学效率提升7%,在额定风速下输出功率波动幅度缩小至±2.5%,使整机发电量年增益达3.2%。此外,碳纤维的导电特性使其可通过特殊编织工艺构建防雷网络,较传统铜网方案减重40%,同时将雷击损伤概率降低60%。
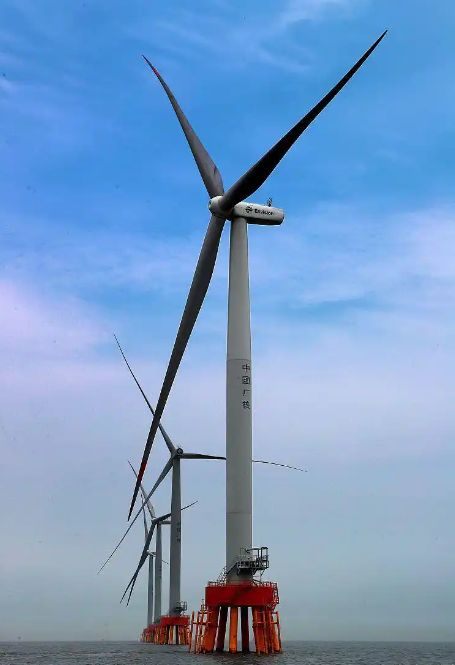
二、抗盐雾腐蚀涂层:多层次防护体系的构建
针对海上风电设备面临的Cl⁻浓度超标、干湿交替等腐蚀环境,长效防腐涂层体系采用"底涂-中间层-面漆"的三明治结构。底涂层选用环氧-聚氨酯互穿网络树脂,其交联密度达2.3g/cm³,可形成致密的物理屏障;中间层通过添加石墨烯纳米片(层数≤10层)实现电化学防护,将腐蚀电流密度抑制至0.1μA/cm²以下;面漆层采用氟碳-有机硅杂化树脂,其表面能低于20mN/m,兼具自清洁与抗生物附着功能。
在某潮间带风电场实测中,该涂层体系在5年服役期内保持完整率98.7%,较传统环氧富锌体系延长维护周期3倍。针对叶片前缘等高磨损区域,开发出含陶瓷微粒的弹性涂层,其邵氏硬度达85D的同时保持20%的断裂伸长率,在模拟沙尘冲击试验中磨损量仅为0.03mm/1000h。
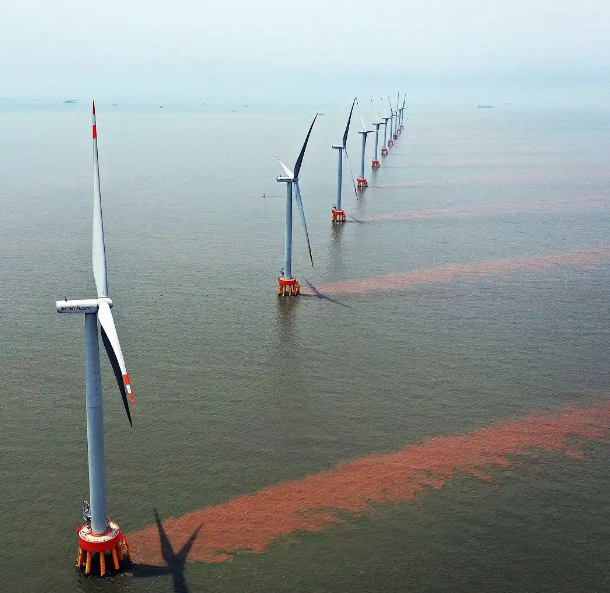
三、集成设计:材料-结构-工艺协同优化
碳纤维主梁与防腐涂层的界面兼容性是集成设计的关键。通过等离子体处理技术,使碳纤维表面含氧官能团浓度提升至8.5%,与环氧树脂的界面剪切强度达到65MPa。在涂层施工环节,采用真空辅助树脂传递模塑(VARTM)工艺,确保涂层与基材间孔隙率低于0.5%,避免因渗透通道导致的腐蚀加速。
某14MW级叶片采用该集成方案后,在盐雾试验箱中完成2000小时加速老化测试,其质量损失率仅为0.02%,远低于行业0.3%的失效阈值。经济性分析显示,虽然碳纤维主梁使叶片成本增加15%,但通过减重带来的运输成本下降、防腐周期延长以及发电效率提升,使全生命周期度电成本降低9.2%。
四、技术展望:迈向深远海的装备革新
随着单机容量向20MW级迈进,碳纤维主梁与防腐涂层的集成技术正面临新的突破方向。在材料层面,碳玻混杂结构(体积比1:2)可平衡性能与成本,使150米级叶片主梁减重35%的同时成本增幅控制在8%以内。在涂层技术方面,自修复微胶囊涂层通过封装愈合剂,可在裂纹扩展至50μm时自动修复,使防腐寿命延长至30年。
通过建立"材料基因库-数字孪生-智能监测"三位一体的研发体系,未来海上风电装备将实现从被动防腐到主动健康管理的跨越。集成碳纤维主梁与智能防腐涂层的叶片,配合光纤传感器网络,可实时监测结构损伤与涂层状态,使运维成本降低40%以上,为深远海风电规模化开发提供坚实保障。