在机器人技术向高精度、高负载、高动态性能持续迭代的进程中,关节模块的轻量化与可靠性始终是制约机器人运动效能的核心瓶颈。近期,一种基于聚醚醚酮(PEEK)复合材料的谐波减速器技术突破,为机器人关节设计开辟了全新路径。该技术通过材料创新与结构优化,在重量、传动效率与耐久性三大维度实现跨越式提升,或将成为人形机器人、协作机器人及工业机械臂等领域的标准配置。
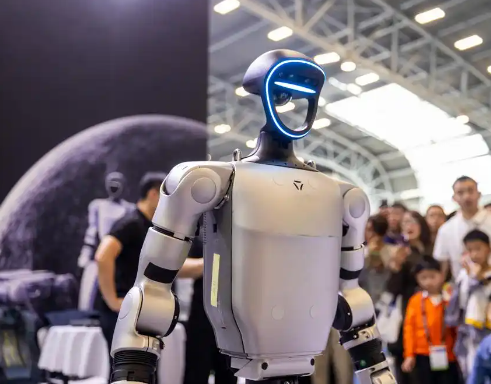
材料革新:PEEK复合材料突破传统金属局限
传统谐波减速器多采用铝合金或钛合金制造,尽管金属材料具备高刚性优势,但其密度高、减震性能差的问题在机器人关节应用中日益凸显。PEEK作为一种特种工程塑料,凭借其密度仅为铝的一半、单位重量强度是铝的5-7倍的特性,成为替代金属的理想选择。通过与碳纤维复合,材料的抗冲击强度可达180MPa,同时保持与人体骨骼相近的弹性模量,显著降低关节运动时的冲击载荷。
在实际应用中,某型号PEEK复合材料谐波减速器通过高分子复合材料轴承与弹性中空滚柱一体化架构,将轴承组件重量降低61%,扭矩/重量比提升74%。这种设计不仅优化了关节的功率密度,还通过阻尼特性提升传动平稳性,使机器人在高速运动时仍能保持无振动传动。
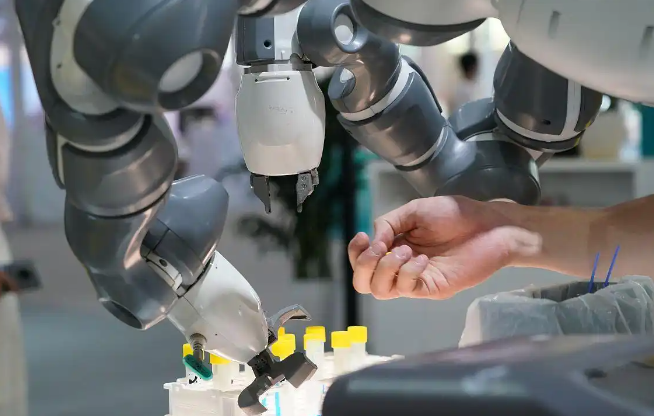
结构突破:集成化设计实现性能跃升
新一代谐波减速器的核心创新在于对传统结构的颠覆性重构。通过将内齿轮与交叉滚子轴承集成设计,该技术减少了50%以上的传统金属组件,同时采用波浪形离散接触技术解决螺栓应力集中难题。实验数据显示,在20N·m负载、2000rad/min转速的额定工况下,复合材料减速器的柔轮与刚轮接触齿数达52对,较金属基材料提升47%,啮合面积增加使承载能力提升30%以上。
更值得关注的是,该技术通过模块化设计实现与90%以上伺服电机的适配,装配效率提升50%。在某协作机器人手臂测试中,采用此技术的关节模块使整机重量降低10公斤,运动速度提升25%,能耗降低18%,同时满足20000小时免维护运行要求。这种性能提升对于需要高动态响应的工业场景或人形机器人灵巧操作具有战略意义。
产业化前景:技术迭代催生百亿级市场
随着特斯拉、波士顿动力等企业加速推进人形机器人量产,关节模块的轻量化需求呈现爆发式增长。据测算,单台机器人PEEK用量约6.5公斤,若2027年全球人形机器人年产量达500万台,对应材料需求将超3万吨,市场规模突破150亿元。目前,国内企业已突破PEEK材料量产技术,成本较进口产品降低60%,为大规模应用奠定基础。
在技术迭代方面,3D打印与激光直接成型(LDS)技术的结合,使PEEK部件能够实现复杂曲面一体化成型,进一步缩短研发周期。例如,某企业通过激光直接成型技术,在PEEK减速器外壳集成5G天线,推动机器人关节向微型化、智能化方向发展。
挑战与展望:成本与工艺仍需突破
尽管技术优势显著,但PEEK复合材料减速器的产业化仍面临挑战。当前材料成本仍为铝合金的3-5倍,且低温脆性问题需通过碳纤维含量优化解决。此外,高精度注塑模具与微米级CNC加工设备的国产化率不足30%,导致产能扩张受限。
不过,随着氟酮等核心原料产能扩张,以及日本某企业建成全球首个PEEK化学循环产线,材料成本有望在未来3年内下降10%-15%。行业专家预测,到2030年,PEEK复合材料减速器将在机器人关节市场占有率突破40%,成为推动智能制造升级的关键基础设施。