在高端制造领域,碳纤维增强复合材料凭借其卓越的力学性能与轻量化特性,已成为航空航天、汽车工业及新能源装备的核心材料。模压成型工艺作为其主流加工技术之一,通过温度、压力与时间的精准控制,实现了复杂结构件的高效制造。该工艺结合了碳纤维的高强度特性与模压成型的规模化生产优势,为复合材料的大规模应用提供了技术支撑。
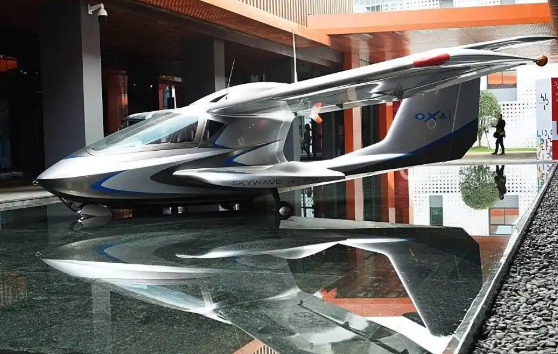
工艺特性与核心优势
碳纤维模压成型工艺的核心特性体现在材料性能与成型效率的协同优化。碳纤维与树脂基体的复合结构赋予制品极高的比强度和比模量,其密度仅为钢材的1/4,但抗拉强度可达3500MPa以上。模压成型通过三维铺层设计与热压固化,可实现复杂曲面的整体成型,如飞机翼肋、汽车电池箱体等结构,尺寸精度可达±0.2mm。该工艺的自动化程度较高,从预浸料裁剪到热压成型均可集成于生产线,单件生产周期可缩短至10分钟以内,显著优于传统手糊工艺。
工艺的环保性同样突出,碳纤维废弃物可通过热解回收实现95%以上的材料再利用,符合循环经济要求。在新能源汽车领域,某企业采用该工艺生产的电机端盖,较金属材质减重42%,同时耐温等级提升至200℃以上,展现了材料性能与工艺效率的双重突破。
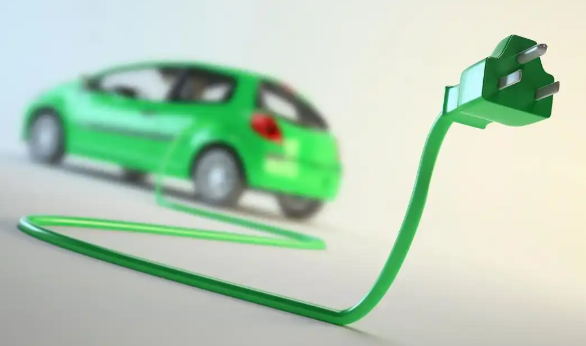
标准化生产流程解析
生产流程始于原材料的精细化处理。碳纤维预浸料需在恒温恒湿环境中保存,树脂含量控制在38±2%以确保流动性。模具设计采用CAD/CAE一体化技术,通过有限元分析优化流道结构,某航空部件模具的排气槽设计使气泡残留率降低至0.5%以下。铺层工序中,自动裁剪机按预设角度切割预浸料,机器人手臂以±1°的精度完成层叠,并施加0.3MPa压力排除气泡。
热压成型阶段采用油电混合压力机,温度控制精度达±2℃。某汽车零部件生产线数据显示,180℃×8MPa×15分钟的工艺参数组合,可使制品孔隙率稳定在1.2%以下。冷却过程采用梯度降温策略,先以5℃/min速率降至120℃,再自然冷却至室温,有效抑制了残余应力。脱模后制品需经三坐标测量仪检测,某风电叶片根部的尺寸合格率通过此流程提升至99.3%。
关键工艺参数控制
模压温度是决定固化质量的核心参数。实验表明,当温度低于130℃时,树脂交联密度不足,制品层间剪切强度下降25%;而超过170℃则易引发暴聚,导致表面焦化。压力控制需兼顾填充性与纤维损伤阈值,某研究机构发现,当压强超过12MPa时,碳纤维束出现断裂,制品弯曲强度降低18%。时间参数方面,3mm厚制品的保压时间需≥8分钟,每增加1mm厚度需延长2分钟,以确保固化深度达标。
质量控制体系贯穿全流程。在线监测系统通过红外热像仪实时捕捉模具温度分布,某生产线据此将温度不均匀度控制在3℃以内。力学性能检测采用超声波C扫描,可探测出直径0.5mm以上的内部缺陷。某航空企业通过建立工艺参数数据库,将制品合格率从87%提升至96%,单条生产线年产能达12万件。
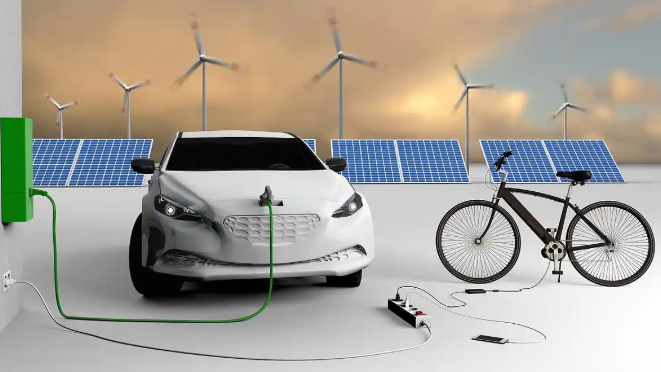
常见缺陷与解决方案
未充满缺陷多由加料不足或压力偏低引起,某案例显示,将加料面积增加20%并提升至10MPa后,边缘填充率从85%提升至99%。鼓泡问题常与树脂挥发分有关,通过预抽真空工艺可将气体残留量降低80%。翘曲变形则需优化模具温差设计,某汽车部件通过将上下模温差控制在5℃以内,使翘曲量从3.2mm降至0.8mm。
表面质量缺陷方面,针孔问题可通过增加排气槽数量解决,某风电部件模具改造后针孔密度从15个/m²降至2个/m²。裂纹缺陷多源于固化收缩应力,采用低收缩率树脂体系可使裂纹发生率降低90%。粘模现象则需加强模具表面处理,某企业通过镀铬工艺将脱模力降低60%,模具使用寿命延长至2万次以上。
这项工艺的成熟应用,不仅推动了复合材料制造技术的进步,更通过工艺参数的精准控制与质量保障体系的完善,为高端装备的轻量化与高性能化提供了可靠解决方案。随着智能制造技术的融入,模压成型工艺正朝着更高效、更环保、更智能的方向发展。