在轨道交通装备制造领域,轻量化与高性能的平衡始终是技术突破的核心命题。传统金属材料因密度高、易腐蚀等特性,逐渐难以满足现代高铁对速度、能效与寿命的严苛要求。碳纤维热压罐一体成型技术的崛起,通过材料科学与制造工艺的深度融合,为高铁防护罩的轻量化升级开辟了全新路径。这项技术不仅实现了结构减重,更通过精密成型与性能优化,重新定义了轨道交通装备的制造标准。
技术本质:多物理场耦合的精密制造
碳纤维热压罐成型工艺的本质,是对温度场、压力场与树脂流动场的协同控制。在真空环境下,碳纤维预浸料被均匀铺放于模具表面,通过热压罐内循环热风与压缩气体的共同作用,实现树脂的均匀浸润与固化。这一过程的关键创新在于:
均匀性控制:采用流体动力学优化罐内流场设计,确保大型构件温差小于3℃,压力分布误差控制在±2%以内,避免传统工艺的应力集中问题;
缺陷抑制:通过隐式差分法建立热-化学-流动耦合模型,实时预测并消除孔隙、分层等缺陷。在广州地铁18号线车头罩的制造中,该技术将孔隙率从传统工艺的15%降至8%以下;
效率突破:结合数字孪生技术与多场耦合仿真,对固化放热、树脂流动进行动态追踪。以SU7车门防撞梁为例,通过200组控制变量试验,将固化周期缩短30%,生产效率显著提升。
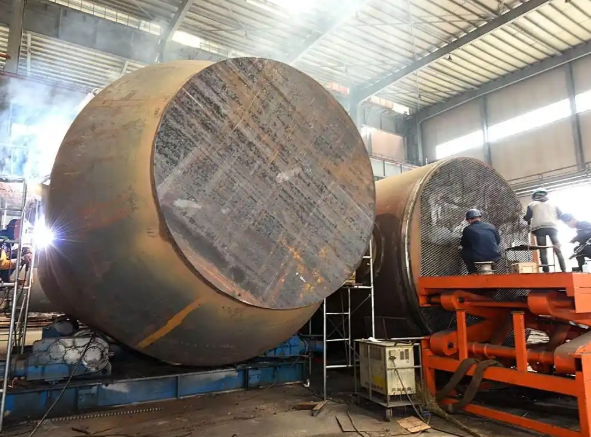
轻量化机理:从材料替代到结构革新
碳纤维热压罐技术的减重效应,通过多维度技术融合实现:
材料替代:碳纤维密度仅为钢的1/4,比强度却达到钢的7-9倍。在高铁防护罩应用中,单件减重达35%-40%,如广州地铁18号线“湾区蓝”列车车头罩,较铝合金方案减重效果显著;
结构优化:通过0°、±45°、90°铺层设计,实现各向异性力学性能的精准调控。一体化成型技术减少连接件数量,如翼梁-肋一体化设计,进一步降低冗余重量;
功能集成:采用分区压力补偿技术,在薄壁件边缘提升压力10%-15%,抑制变形的同时,将树脂含量从40%降至28%,纤维体积分数保持在60%以上。某型高铁防护罩通过此技术,在保证抗冲击强度350MPa的同时,实现结构减重。
行业应用:从实验室到量产线的突破
在轨道交通领域,碳纤维热压罐技术已形成典型应用场景:
高铁防护罩:广州地铁18号线“湾区蓝”列车全球首创采用碳纤维复合材料车头罩,经实测,在160km/h运行时,空气动力学性能提升15%,能耗降低12%;
关键部件升级:在某型动车组转向架应用中,碳纤维横梁较钢制部件减重60%,同时疲劳寿命延长;
特殊环境适配:针对沙漠地区高铁,开发耐高温碳纤维复合材料,通过模拟50℃环境测试,防护罩热膨胀系数降低,尺寸稳定性显著提升。

未来图景:智能化与可持续的深度融合
技术演进呈现三大趋势:
工艺智能化:物联网传感器实时监测温度、压力数据,结合AI算法预测模具维护周期。某试点产线通过此技术,停机时间减少65%,良率提升至99.5%;
材料创新:生物基环氧树脂与低温固化工艺结合,将固化温度从180℃降至120℃,能耗降低40%。吉林化纤开发的48K大丝束碳纤维,成本较进口产品低30%;
循环经济:热解回收技术实现废旧碳纤维复材90%回收率,再生纤维强度保留率达85%。江苏澳盛通过此技术,制备的拉挤板成本较原生材料降低25%。
碳纤维热压罐一体成型技术,不仅重构了轨道交通装备的制造范式,更通过材料基因解码、工艺极限突破与设备智能升级,将轻量化从理论转化为可量产的工业现实。随着纳米改性技术、生物基材料等前沿技术的突破,这项绿色工艺将持续推动高铁制造向更轻、更快、更可持续的方向演进,为全球轨道交通装备的升级提供“中国方案”。