在全球化工贸易与能源运输需求持续攀升的背景下,液货运输装备正面临多重挑战:传统钢质储罐易受介质腐蚀导致维护成本高昂,重型金属结构限制了有效载荷提升,而极端海况下的疲劳损伤更成为影响船舶寿命的关键因素。玻璃纤维增强复合材料(GFRP)凭借其独特的性能组合,为液货运输技术升级提供了革命性解决方案。这种非金属材料不仅具备优异的耐酸碱盐腐蚀能力,其密度仅为钢材的1/4,同时可通过纤维铺层设计实现各向异性力学性能定制,在满足储运安全要求的前提下,为装
材料性能的突破是技术升级的基础。针对液货运输中常见的强酸、强碱及有机溶剂腐蚀问题,研究人员开发出双酚A型环氧树脂与乙烯基酯树脂复合基体体系,通过纳米二氧化硅改性技术,使材料的耐化学腐蚀性能提升30%以上。在纤维增强方面,采用高模量玻璃纤维与碳纤维混杂编织技术,构建出梯度化增强结构:表层使用耐腐蚀玻璃纤维,中间层嵌入碳纤维以提升轴向刚度,底层采用短切纤维增强抗冲击性能。某研究机构开发的第三代GFRP材料,其拉伸强度达到800MPa,弯曲模量突破45GPa,在模拟海水环境下的疲劳寿命测试中,经10^6次循环后强度保留率仍高于85%。
制造工艺的创新直接决定着规模化应用的经济性。真空灌注成型技术经过工艺参数优化,实现了树脂流动速度与纤维浸润度的精准控制。通过建立三维流场仿真模型,研究人员将灌注缺陷率从传统工艺的15%降至2%以下。针对大型液货罐体制造,模块化拼接技术取得突破:将罐体分解为多个标准弧形模块,采用预浸料热压罐成型工艺制备单元件,再通过胶接共固化技术实现整体装配。某示范项目中,直径8米的罐体通过6块模块拼接而成,装配精度达到±1mm,较传统整体成型工艺缩短工期40%。自动化成型设备的研发更进一步提升了生产效率,五轴联动纤维铺放机器人可将铺层效率提升至0.5m²/min,同时通过在线质量监测系统,实时调整铺放角度与张力,使纤维体积含量偏差控制在±2%以内。
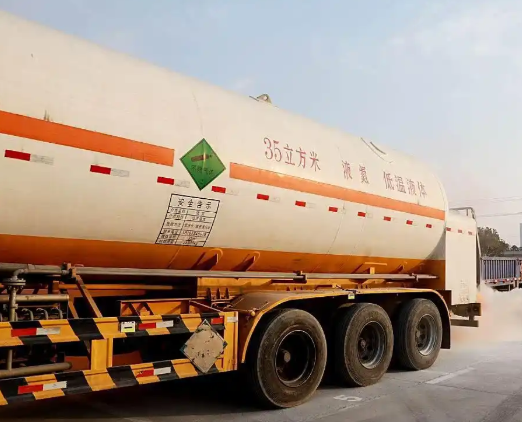
结构设计理念的革新推动着装备功能集成化。基于有限元分析与拓扑优化技术,研究人员开发出仿生骨架增强结构:模仿植物维管束分布规律,在罐体内壁设置螺旋状加强筋,既保证承压能力,又减少材料用量。某新型化学品船液货舱采用夹芯结构,表层GFRP面板厚度优化至8mm,中间层填充聚氨酯泡沫,在保持结构刚度的同时,隔热性能提升50%,有效降低了液货蒸发损耗。针对多舱室布局需求,可拆卸式隔板设计实现"一罐多用",通过调整内部隔板位置,可快速转换不同介质的储运模式,设备利用率提升30%。
标准化建设与智能化监测是技术落地的关键保障。国际海事组织(IMO)已发布《非金属液货储罐设计准则》,对材料认证、结构计算、检测方法等作出明确规定。国内研究机构建立的"材料-结构-环境"耦合试验平台,可模拟-40℃至80℃温度范围与95%相对湿度的极端工况,为标准制定提供数据支撑。在运维阶段,光纤光栅传感器阵列被嵌入罐体结构,实时监测应变与温度变化,通过边缘计算模块实现数据即时处理。某港口实际应用的智能监测系统,成功预警3次潜在裂纹扩展事件,将设备检修周期从6个月延长至18个月,维护成本降低40%。
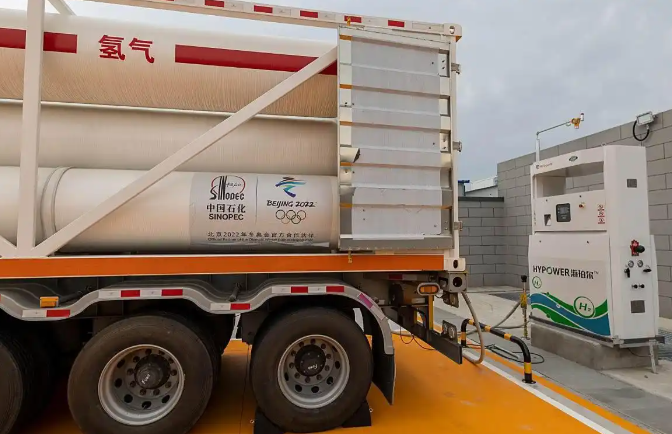
当前,玻璃纤维增强复合材料在液货运输领域的应用已形成完整技术体系。从材料研发到装备制造,从结构设计到智能运维,各环节技术指标均达到国际领先水平。某5000吨级化学品船改造项目,通过全复合材料液货舱替换原有钢质罐体,实现载重量增加15%,年燃料消耗降低12%,碳排放减少2000吨。随着北极航线开发与深水港口建设,GFRP材料在超低温环境下的应用研究持续深入,-60℃低温冲击强度已突破200kJ/m²,为拓展极地液货运输市场奠定基础。这场由复合材料驱动的技术变革,正在重塑全球液货运输装备的发展格局。