在航空航天、新能源汽车、风电能源等高端制造领域,复合材料因其轻量化、高强度、耐腐蚀等特性已成为不可替代的关键材料。然而,复合材料的连接技术长期面临“强度与效率难以兼顾”“异种材料兼容性差”等瓶颈,传统机械连接与胶接工艺逐渐无法满足现代工业对高性能、高可靠性的需求。近年来,以激光焊接、感应焊接、超声波焊接为代表的先进焊接技术,通过工艺创新与智能化升级,不仅实现了复合材料连接的高效自动化,更赋予其导电、传感、自修复等附加功能,为复合材料的大规模应用开辟了新路径。
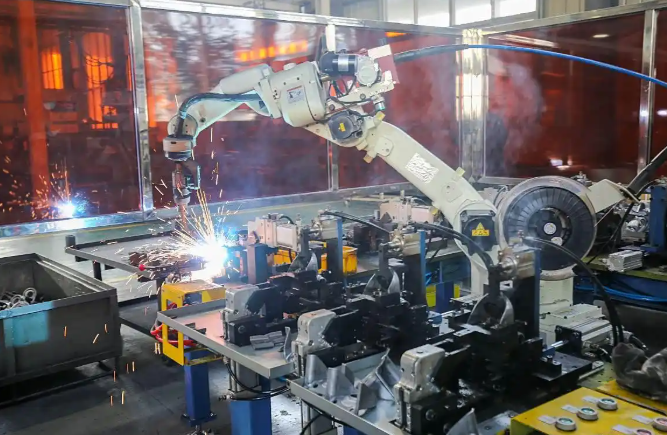
技术革新:从热固性到热塑性的连接突破
复合材料连接技术的突破首先源于对材料特性的深度适配。传统热固性复合材料因固化后不可重塑,焊接难度大,而热塑性复合材料凭借可熔融再加工的特性,成为先进焊接技术的首选对象。以感应焊接为例,该技术通过电磁感应加热金属网嵌入层,使热塑性基体在局部熔融后实现分子级结合,接头的抗拉强度可达母材的90%以上。某研究机构开发的碳纤维增强聚醚醚酮(PEEK)感应焊接工艺,在120秒内即可完成2米长风电叶片主梁的连接,较传统胶接工艺效率提升5倍,且无需使用挥发性有机化合物(VOC)排放的胶黏剂。
更引人注目的是激光焊接技术的突破。针对热固性复合材料,科研团队创新性地采用“透射式激光焊接”工艺,通过调整激光波长与碳纤维排布角度,使激光能量选择性被纤维吸收,在避免基体过热的同时实现深层穿透焊接。某航空项目采用该技术后,飞机尾翼蒙皮与骨架的连接强度较铆接提升40%,重量减轻25%,且焊接过程全程无粉尘产生,符合航空制造的绿色化趋势。
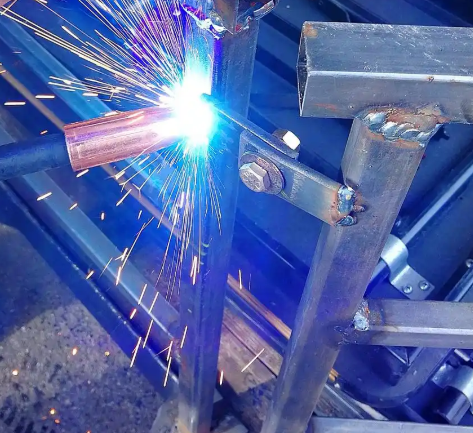
自动化升级:机器人与AI重塑生产范式
先进焊接技术的落地离不开自动化装备的支撑。在某新能源汽车电池箱体生产线,六轴机器人搭载高精度激光焊接头,通过3D视觉系统实时扫描复合材料箱体的曲面轮廓,自动生成焊接路径,单班次可完成80套箱体的密封焊接,良品率达99.5%。更智能的是,AI算法可基于历史数据预测焊接变形量,通过动态调整激光功率与焊接速度,将变形量控制在0.2毫米以内,彻底解决了复合材料焊接易变形的行业难题。
超声波焊接的自动化应用同样令人瞩目。在风电叶片制造中,超声波焊接系统与自动铺带机协同工作,在铺放碳纤维预浸料的同时,通过超声波振动使树脂瞬间熔融,实现层间即时粘接。这种“铺放-焊接”一体化工艺将叶片制造周期从7天缩短至48小时,且焊接能量输入精准可控,避免了传统热压罐工艺的高能耗问题。某风电企业测算,采用该工艺后,单条生产线年减排二氧化碳达1200吨。
功能化拓展:从结构连接到智能集成
先进焊接技术的价值不仅在于连接本身,更在于其赋予复合材料的功能化潜力。某研究团队在焊接过程中嵌入银纳米线导电网络,使复合材料接头同时具备结构连接与电信号传输功能。在航空发动机叶片中,这种“导电焊接接头”可实时监测裂纹扩展,通过电阻变化预警结构失效,将传统被动检测转变为主动预防,显著提升飞行安全性。
更前沿的探索聚焦于自修复功能。某项目通过在热塑性复合材料中预埋微胶囊,当焊接接头因疲劳产生微裂纹时,微胶囊破裂释放修复剂,在后续焊接过程中与基体反应实现裂纹愈合。实验数据显示,经三次自修复循环后,接头强度仍保持初始值的85%,为复合材料的长寿命设计提供了全新思路。
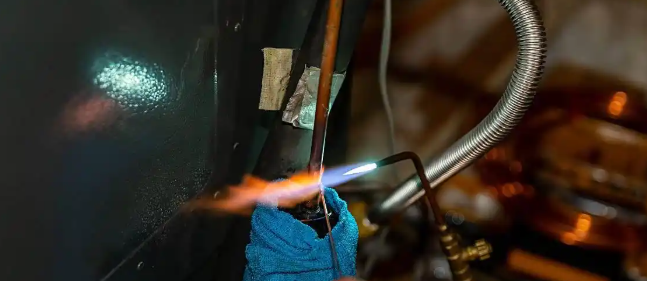
未来展望:智能化与多材料兼容的深度融合
随着数字孪生、元宇宙等技术的渗透,焊接工艺的智能化水平将进一步提升。某实验室正在构建“焊接数字孪生系统”,通过高精度传感器采集焊接过程中的温度、应力数据,结合机器学习模型实时优化工艺参数,最终实现“一材一策”的定制化焊接。同时,针对碳纤维、玻璃纤维、芳纶纤维等多材料复合体系的兼容性需求,科研人员正开发“多模态焊接平台”,通过切换激光、感应、摩擦等多种能源模块,实现异种复合材料的高效连接。
从风电叶片的千米级主梁到航空发动机的毫米级精密部件,先进焊接技术正在重新定义复合材料的应用边界。它不仅解决了传统连接的效率与可靠性矛盾,更通过功能化集成推动复合材料从“结构材料”向“智能材料”跃迁。可以预见,在自动化与功能化的双轮驱动下,复合材料焊接技术将成为高端制造领域实现“双碳”目标与数字化转型的关键支撑。