在高端制动领域,碳陶复合材料凭借其卓越的热稳定性成为突破性能极限的关键。这种由碳纤维增强碳化硅基体制成的材料,在赛车、高速列车乃至航空航天领域展现出传统金属刹车盘无法比拟的优势。其核心在于通过精密的材料设计与工艺优化,实现了在2000℃极端温度下的结构稳定与性能可控,为现代交通工具的制动系统带来了革命性变革。
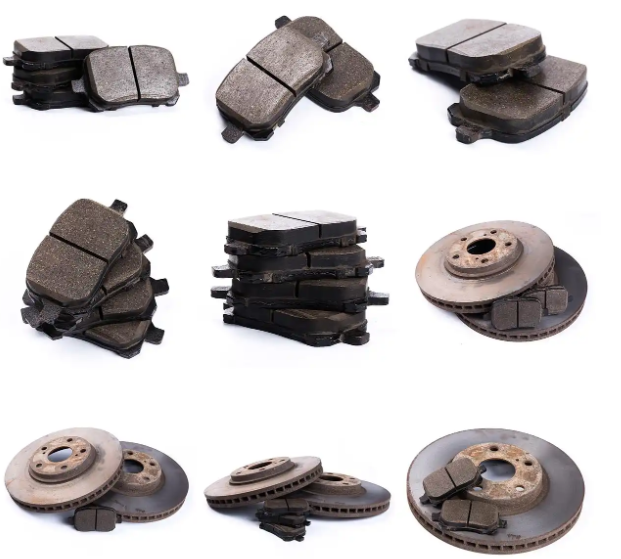
热稳定性机理:微观结构与高温行为的博弈
碳陶制动材料的热稳定性源于其独特的组成与相变机制。材料以碳纤维为骨架,碳化硅(SiC)为基体,辅以少量残余硅元素。在高温环境下,SiC基体通过主动氧化生成致密的二氧化硅(SiO₂)保护层,有效隔绝氧气向材料内部渗透。这种自生成氧化膜的机制,使材料在1200℃以上仍能维持稳定的化学状态。而碳纤维在超高温(>1500℃)时虽可能发生被动氧化生成CO/CO₂气体,但通过热解碳界面涂层的保护,可显著延缓这一过程。
氧化反应的动力学行为呈现温度依赖性。中低温(<1200℃)条件下,氧气通过材料内部孔隙与裂纹扩散,形成扩散控制的氧化机制;高温(>1200℃)时,SiC的快速氧化转为反应控制,生成的SiO₂层厚度随温度升高而增加,形成动态保护屏障。实验数据显示,在1300℃环境下,碳陶刹车盘的摩擦系数仍能稳定在0.38±0.02,较传统钢盘提升30%,验证了其优异的抗氧化能力。
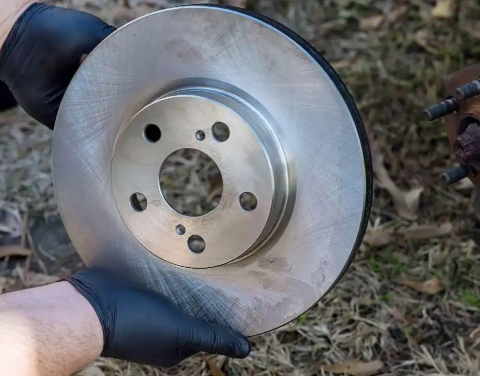
热应力演化是另一关键因素。碳纤维的热膨胀系数(CTE≈1×10⁻⁶/℃)与SiC基体(CTE≈4×10⁻⁶/℃)的显著差异,在高温下会产生径向热应力。这种应力若未得到有效控制,可能导致界面脱粘或微裂纹扩展。通过梯度结构设计,表面采用高SiC含量层(>80%)增强抗氧化性,内部逐步增加碳纤维体积分数(至45%),可平衡强度与韧性,同时通过热解碳界面相缓解CTE失配应力。
工程优化策略:从纳米改性到系统集成
为进一步提升热稳定性,工程领域采用了多维度优化策略。纳米改性技术通过引入纳米SiC颗粒或氧化锆(ZrO₂)相,利用弥散强化机制提升基体耐温性;添加石墨烯或碳纳米管,构建三维导热网络,使热扩散系数提升至8×10⁻⁶m²/s,有效降低局部热点温度。某型新能源汽车升级碳陶刹车后,峰值制动温度降低200℃,连续20次急刹无热衰减,正是这一技术的直接体现。
梯度结构设计是另一创新方向。通过调整材料组分的空间分布,表面形成高SiC含量的抗氧化层,内部逐步过渡到高碳纤维含量的增韧层。这种设计不仅提升了材料的整体性能,还通过热解碳界面相的缓冲作用,将氧化损伤累积对剩余强度的影响降低。实验表明,采用梯度结构的碳陶刹车盘,在“中等高”温度条件下的剩余强度保留率较传统设计提升25%。
抗氧化涂层体系的应用进一步强化了热稳定性。表面沉积碳化硅或氮化硅(Si₃N₄)涂层,厚度≥50μm,形成物理屏障隔绝氧气;侧边涂覆碳化钨(WC)涂层,厚度>0.8mm,防止高速摩擦导致的边缘氧化。某型赛车升级碳陶刹车后,在连续3公里急弯下坡测试中,摩擦系数从0.42降至0.28,而碳陶刹车仍能维持稳定值,涂层技术功不可没。
制造工艺的优化同样关键。反应熔渗(RMI)工艺在1450℃下使液态硅渗透碳纤维预制体,形成致密SiC基体;结合热压烧结(HP)与化学气相渗透(CVI),消除微观孔隙,提升材料密度至2.2g/cm³。这种工艺不仅增强了材料的机械性能,还通过减少内部缺陷,降低了高温下的应力集中风险。
应用案例与未来挑战
碳陶制动材料的工程价值已在多领域得到验证。特斯拉Model S Plaid赛道实测显示,升级后的碳陶刹车系统在连续20次急刹中性能无衰减,100km/h急刹制动距离较普通碟刹缩短2.3米。在高铁领域,某型高速列车采用碳陶刹车盘后,制动系统维护周期延长,粉尘排放量降低85%,符合欧盟颗粒物排放标准。
然而,技术突破仍面临挑战。低温摩擦性能优化需通过石墨烯改性提升-20℃环境下的稳定性;成本控制需开发连续碳纤维增强陶瓷基复合材料的近净成型工艺,目标将材料成本降低40%;系统集成则需研发与电子机械制动系统的深度耦合方案,实现制动能量回收效率最大化。
从实验室到商业化,碳陶制动材料正通过热稳定性机理的深入解析与工程优化技术的持续创新,重新定义制动系统的性能边界。这种材料不仅为高端交通工具提供了安全保障,更通过轻量化与耐久性的提升,推动着整个交通行业向更高效、更环保的方向演进。