在全球能源结构转型与"双碳"目标驱动下,新能源汽车产业正经历从政策驱动向技术驱动的关键跨越。作为整车性能的核心载体,关键部件的材料革新成为突破续航焦虑、热管理瓶颈与轻量化难题的关键路径。其中,高性能高分子材料凭借独特的分子结构可设计性与综合性能优势,正在电池系统、驱动电机、电控单元及结构轻量化等领域催生革命性创新,为新能源汽车技术升级注入新动能。
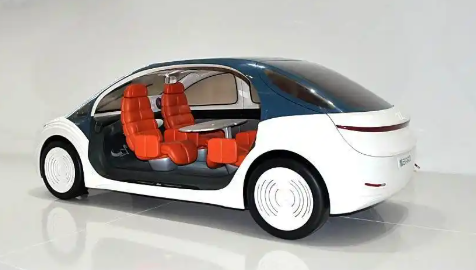
电池系统:构筑安全与效能的双重屏障
在动力电池这个新能源汽车的"心脏"部位,高分子材料的应用深度直接影响着能量密度与安全边界。以固态电池研发为例,传统液态电解质存在的漏液、燃爆风险催生了固态聚合物的技术突破。聚环氧乙烷(PEO)基复合电解质通过引入纳米级无机填料,在-20℃至80℃宽温域内实现离子电导率0.1-1mS/cm,较液态体系提升3倍循环稳定性。某研究机构开发的梯度结构隔膜,采用聚偏氟乙烯-六氟丙烯(PVDF-HFP)与芳纶纳米纤维复合,在4.5V高压条件下仍能保持99.8%的孔隙率,针刺实验中热失控温度延迟120秒,为电池包安全设计争取关键响应窗口。
在热管理领域,相变材料(PCM)与导热聚合物的协同应用正在重构温控体系。某车型电池箱体采用石蜡/膨胀石墨复合PCM内衬,结合氮化铝填充的聚酰胺66(PA66)导热骨架,使极端工况下温差控制在5℃以内,快充效率提升18%。更值得关注的是,发泡聚丙烯(EPP)与气凝胶复合的轻量化箱体,在保持150kPa抗压强度的同时,密度降低至0.12g/cm³,较金属方案减重42%,为续航里程贡献直接增量。
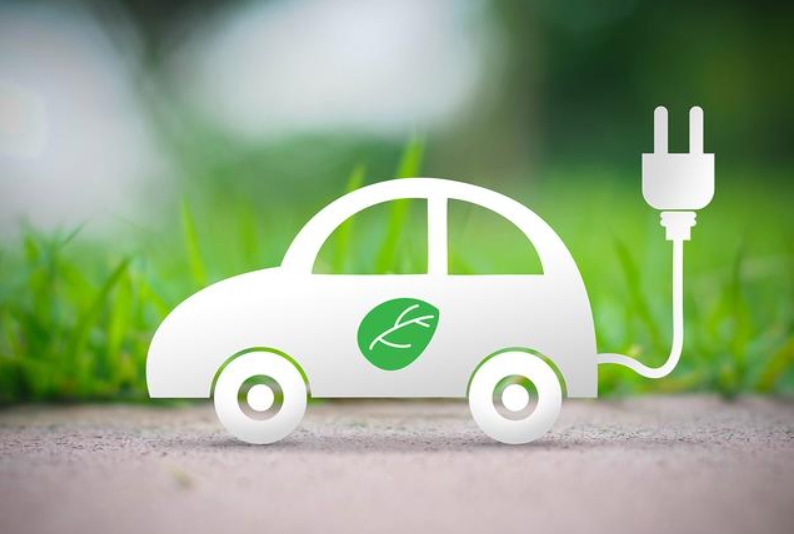
驱动系统:突破极限的性能载体
在电机这个动力转换的核心部件,高分子材料正在打破传统金属材料的性能桎梏。某研究机构开发的耐电晕聚酰亚胺(PI)薄膜,通过分子链中引入苯并噁唑结构,在200℃环境下介电强度仍达220MV/m,较常规PI薄膜提升40%,有效解决高速电机绝缘老化问题。在轴承领域,聚醚醚酮(PEEK)基自润滑复合材料在2万转/分钟工况下,摩擦系数稳定在0.08-0.12,较金属轴承磨损量降低83%,同时实现无油润滑,彻底消除润滑油泄漏风险。
电控单元的精密化发展,对连接器材料提出严苛要求。液晶聚合物(LCP)凭借其近零吸水率与超低介电损耗,正在5G车载通信模块中展现独特价值。某车型采用LCP注塑成型的毫米波雷达外壳,在24GHz频段下信号衰减低于0.5dB,较传统工程塑料提升3个数量级传输稳定性。更引人注目的是,柔性电路板(FPC)用聚酰亚胺基材通过纳米银线改性,在-40℃至125℃冷热循环中保持99.9%的导电通路完整性,为域控制器集成化提供关键支撑。
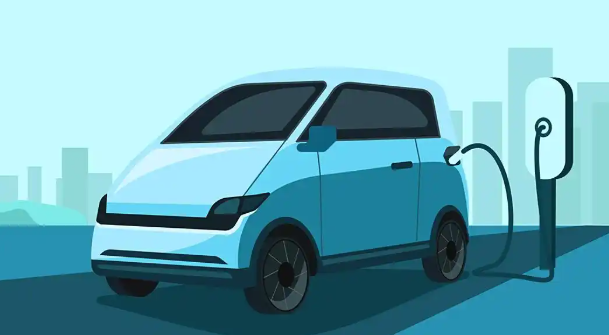
结构创新:轻量化与功能化的完美融合
在车身轻量化领域,连续纤维增强热塑性复合材料(CFRTP)正在改写传统制造工艺。某车型B柱采用玻璃纤维增强聚苯硫醚(PPS)复合材料,通过激光辅助径向成型(LART)工艺,在保持1500MPa弯曲强度的同时,密度降低至1.8g/cm³,较钢制方案减重65%,且实现100%可回收。更突破性的是,碳纤维增强聚醚酮酮(PEKK)在电池包上盖的应用,通过变厚度设计使局部刚度提升3倍,同时整体重量较铝合金方案减轻38%。
在内饰功能化方面,生物基高分子材料正在开辟新赛道。某研究机构开发的蓖麻油基聚氨酯泡沫,在保持45kg/m³密度的同时,声学吸收系数达0.85(1000Hz),较石油基材料提升20%,且VOC排放量降低90%。更值得期待的是,形状记忆聚合物在主动式进气格栅中的应用,通过温度响应实现0.5秒级开合控制,较传统电机驱动方案能耗降低85%,为空气动力学优化提供智能解决方案。
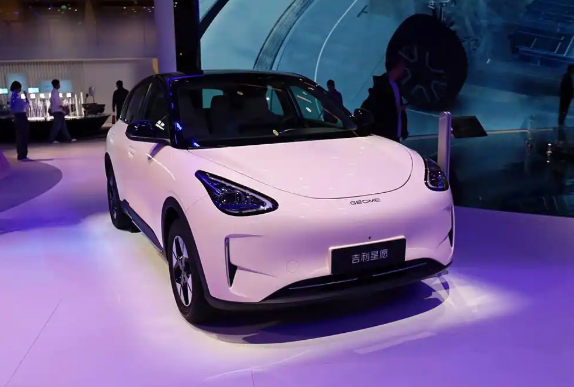
技术挑战与未来方向
尽管前景广阔,行业仍面临材料-工艺-成本的三角困局。例如,超临界CO₂发泡工艺虽能将PA66密度降至0.3g/cm³,但设备投资回收期长达5年;某车型采用的纳米复合冷却管道,虽使电池温差控制在2℃以内,但材料成本较传统方案高出3倍。值得欣慰的是,中国在玄武岩纤维增强PEI、植物油基环氧树脂等领域的专利布局增速达25%,为技术自主化奠定基础。
展望未来,四大趋势将重塑材料应用格局:一是分子级设计通过AI加速,如生成式对抗网络(GAN)已实现聚合物配方开发周期缩短70%;二是4D打印技术使结构件具备环境响应功能;三是区块链技术实现材料全生命周期追溯;四是太空级聚合物(如聚四氟乙烯-碳纳米管复合材料)开始向民用领域渗透。到2030年,全球车用高性能高分子材料市场规模预计突破800亿元,中国将贡献45%以上的增量,一个更安全、更高效、更可持续的新能源汽车时代正在材料创新的驱动下加速到来。