在全球高性能材料需求持续攀升的背景下,芳纶纤维复合涂层凭借其优异的力学性能与功能特性,成为航空航天、防弹防护、交通运输等领域的核心材料。然而,表面惰性导致的界面结合力弱、工艺适应性差等问题,长期制约其性能极限的突破。近年来,通过表面改性、结构设计及工艺创新,芳纶纤维复合涂层的力学性能实现显著提升,为高端制造领域提供了关键材料支撑。
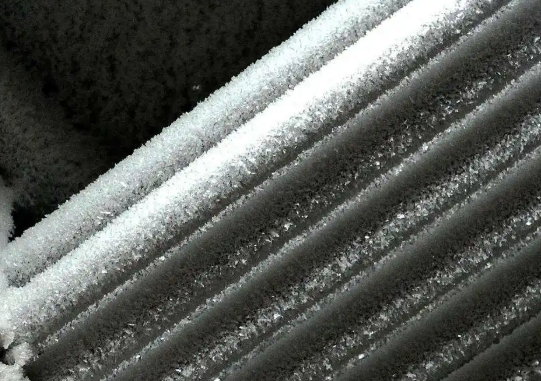
表面改性技术:从惰性到活性的跨越
芳纶纤维的分子链结构赋予其高强高模特性,但也导致表面化学活性低、与基体材料浸润性差。针对这一痛点,研究者开发了物理与化学协同的改性策略。物理改性方面,等离子体技术通过高能粒子轰击纤维表面,形成微纳级粗糙结构,同时引入极性基团。例如,氮气等离子体处理芳纶帘线后,其与橡胶的黏合强度提升40%,且高功率、长时间处理可进一步优化效果。化学改性则聚焦于分子层面的功能化,直接氟化技术通过氟/氮混合气与纤维表面反应,生成C—F、—COOH等活性基团,使杂环芳纶与环氧树脂的界面剪切强度(IFSS)从38.5MPa提升至51.0MPa。更先进的催化氟化策略通过引入Fe³⁺络合剂,选择性调控氟化位点,在保持纤维本体强度99.3%的同时,使界面拔出强度提高36%。
结构设计:刚柔并济的界面优化
除表面改性外,研究者通过结构设计实现界面性能的突破。四川大学团队开发的“刚-柔互锁”多孔结构,利用异氰酸酯与苯并咪唑N—H基团反应,在纤维表面形成聚脲包裹的微纳结构。这种结构既保留聚脲的柔韧性以分散应力,又通过环氧树脂填充增强刚性,使单纤维拔出实验的剪切强度提升115.9%,剪切韧性更是提高493.2%。此外,聚酰胺微球的分形结晶结构通过共价键连接纤维与树脂,使层压板层间剪切强度增加100.5%,冲击韧性提升13.5%。有限元模拟证实,这种结晶微球结构能有效传递界面应力,避免集中导致的失效。
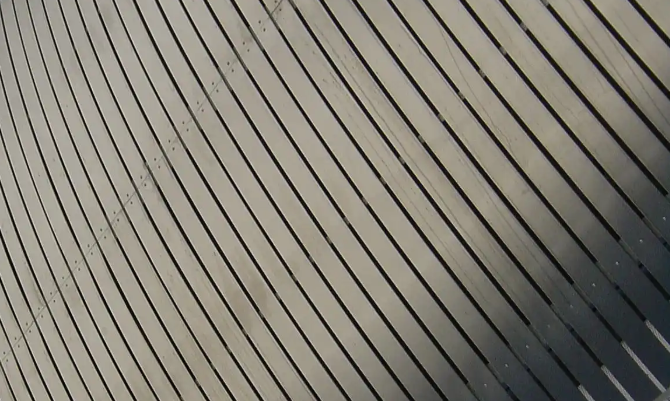
工艺创新:从实验室到产业化的突破
制备工艺的优化对复合涂层性能至关重要。表面涂层技术通过浸渍硅烷、聚氨酯等树脂,愈合纤维表面缺陷并增强浸润性。例如,采用环氧改性RFL胶乳的一浴法处理芳纶,静态黏合性能显著提升,且一次浸渍工艺效率优于传统二次浸渍。在纤维长径比控制方面,研究发现当长径比约为220时,复合材料力学性能达到最优——此时纤维既能有效传递应力,又避免因过长导致的纠缠与分散性下降。此外,等离子体接枝聚合技术通过两阶段反应,先形成活性中心,再引发单体聚合,使改性后的芳纶增强乙烯基复合材料拉伸强度提升30%。
应用验证:从防弹装甲到航空航天
改性技术的突破直接推动芳纶复合涂层在高端领域的应用深化。在防弹防护领域,杂环芳纶与钢铝复合的装甲板可抵御700mm厚反坦克导弹攻击,而软质防弹衣通过引入聚乙烯纤维,在保持防弹性能的同时减重50%。航空航天领域,芳纶复合材料用于制造飞机次结构件,如机舱门窗、整流罩等,减重30%的同时提升耐热性至300℃。交通运输方面,芳纶帘线替代石棉用于轮胎骨架,耐磨性提升2倍,且在高温下仍能保持尺寸稳定。
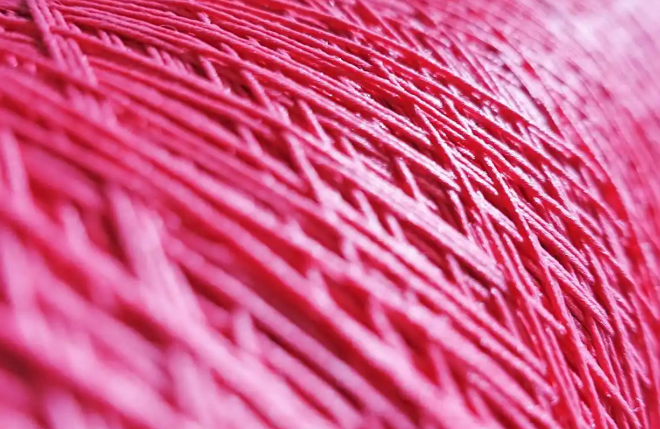
挑战与未来:性能、环保与智能化的平衡
尽管进展显著,芳纶复合涂层仍面临技术瓶颈与市场挑战。改性工艺的高成本(如氟化设备投资大)制约规模化应用,需通过催化氟化等策略降低能耗。环保需求推动非水介质染色、生物基树脂基体等绿色技术的发展。未来,结合AI优化纤维排列、嵌入传感器实现自监测功能,或通过4D打印赋予材料环境响应特性,将进一步拓展芳纶复合涂层的应用边界。
芳纶纤维复合涂层的力学性能增强研究,通过表面改性、结构设计、工艺创新的三维突破,正推动材料科学向更高性能、更环保、更智能的方向演进。随着技术的持续迭代,这一“高性能纤维之王”将在更多领域释放其潜在价值。