在航空航天领域,轻量化与高强度始终是材料科学追求的核心目标。碳纤维增强复合材料凭借其比强度高、耐腐蚀、可设计性强等特性,已成为制造飞机机翼、卫星结构件、火箭壳体等关键部件的首选材料。而将这些高性能材料转化为精密构件的核心工艺——热压罐成型技术,正是支撑大国重器腾飞的“隐形锻造术”。
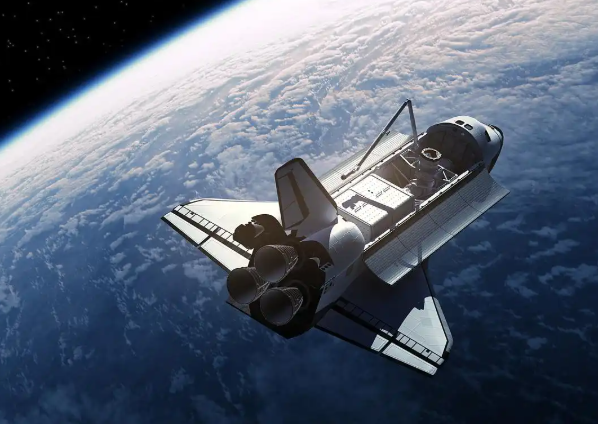
工艺原理:高温高压下的分子交响曲
热压罐工艺的本质是通过精确控制温度、压力与真空环境,实现复合材料预浸料的固化成型。其流程可概括为:将碳纤维预浸料按设计铺层贴合于模具表面,经真空袋密封后置于密闭罐体内,通过循环热气流加热与气体加压,使树脂基体在均匀温压场中完成交联反应。这一过程需满足三大核心条件:
温度均匀性:罐内温差需控制在±3℃以内,通过导流板设计与智能温控系统,确保树脂固化反应同步进行。
压力均布性:采用气体加压方式,压力通过真空袋均匀传递至制件表面,法向压力差小于0.01MPa,有效压缩纤维间隙并排除气泡。
真空辅助性:真空系统维持袋内负压状态,配合透气毡等辅材,使低分子挥发物充分排出,孔隙率可控制在1%以下。
某型飞机机翼蒙皮的制造中,热压罐通过三阶段压力控制:初始低压促进树脂横向流动填充纤维间隙,中压阶段压缩气泡,最终高压抑制树脂收缩,使层合板孔隙率从1.2%降至0.5%,疲劳寿命提升3倍。
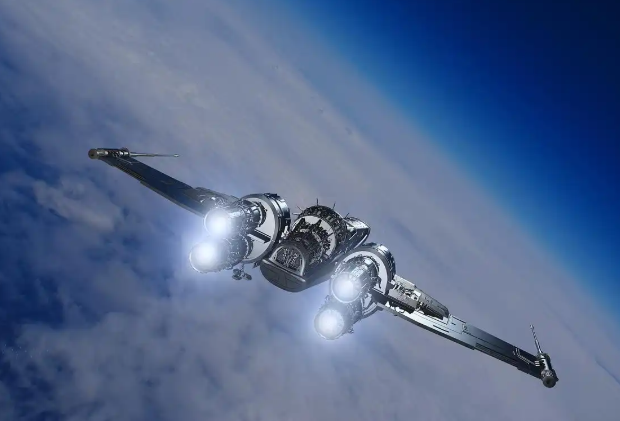
关键设备:精密控制的“炼器炉”
现代航空航天级热压罐已发展为集机械、热工、控制于一体的复杂系统。以某企业交付的Φ5m×11m超大型热压罐为例,其技术特性包括:
温度控制:采用分布式光纤传感网络,实时监测罐内200个测温点,通过PID算法动态调节加热功率,确保温度场均匀性。
压力系统:配备三级增压装置,最大工作压力达1.3MPa,压力控制精度达0.01MPa,配合真空系统可实现真空度≤1kPa。
模具适配:采用碳纤维增强复合材料模具,其热膨胀系数与制件匹配度达95%,结合蜂窝夹层结构,在保证刚度的同时降低自重40%。
这种设备可同时容纳多个大型构件,单次固化周期虽长达72小时,但通过快速固化树脂体系与数字孪生技术优化,已将工艺开发周期压缩。
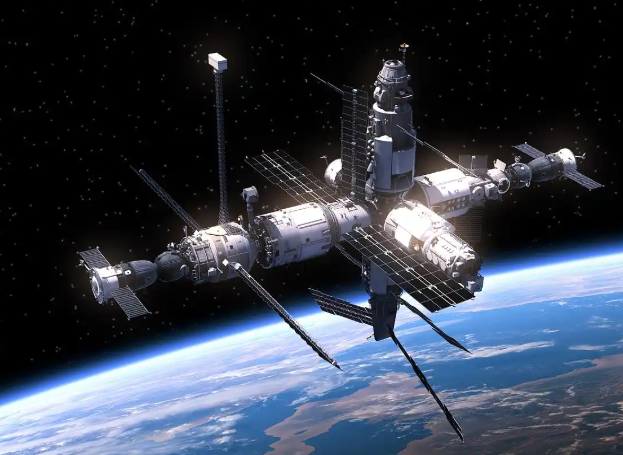
技术挑战与突破方向
尽管热压罐工艺在航空航天领域占据主导地位,但其发展仍面临三大瓶颈:
能耗与成本:传统工艺单次固化能耗高,辅材消耗大。通过开发超临界CO₂辅助成型技术,利用其低黏度高扩散特性,可使树脂浸润时间缩短,同时降低能耗。
尺寸限制:超大型构件制造受限于罐体容积。采用分区冷却与模块化模具设计,可实现机身整体成型,避免分段连接导致的强度损失。
缺陷控制:孔隙率与残余应力直接影响构件性能。引入微波局部加热系统,可在30分钟内将孔隙率修复至0.3%以下;而激光诱导修复技术则能精准处理微米级裂纹。
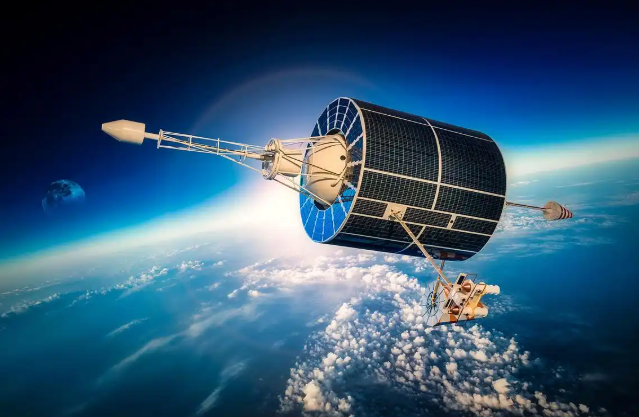
未来展望:智能与绿色的双重变革
随着材料科学与数字技术的融合,热压罐工艺正朝两个维度演进:
智能化升级:构建工艺知识图谱,整合材料数据库与缺陷图谱库,通过贝叶斯优化算法快速锁定最优参数组合。某型卫星结构件制造中,该系统使试错成本降低。
绿色化转型:开发生物基环氧树脂与可回收热塑性复合材料,结合VOC废气处理系统,使碳排放降低。某企业研发的自修复树脂,通过微胶囊化技术实现裂纹自主修复,延长构件使用寿命。
从飞机机翼到深空探测器,热压罐工艺以毫米级的精度控制,铸就着航空航天器的“钢筋铁骨”。这项融合了热力学、流体力学与材料科学的复合技术,不仅是当前高端制造的核心支撑,更在数字孪生与绿色材料的赋能下,持续拓展着人类探索宇宙的边界。