在全球能源转型与“双碳”目标驱动下,海上风电作为清洁能源的“主力军”,正经历着前所未有的技术革新与产业升级。其中,风电叶片作为核心部件,其制造技术的突破直接关系到整个行业的发电效率与成本竞争力。近年来,随着新型复合材料的研发与应用,海上风电叶片制造正迈向轻量化、高强度、耐腐蚀的新阶段,而规模化生产技术的成熟更推动这一创新成果加速落地,为深远海风电开发注入强劲动力。
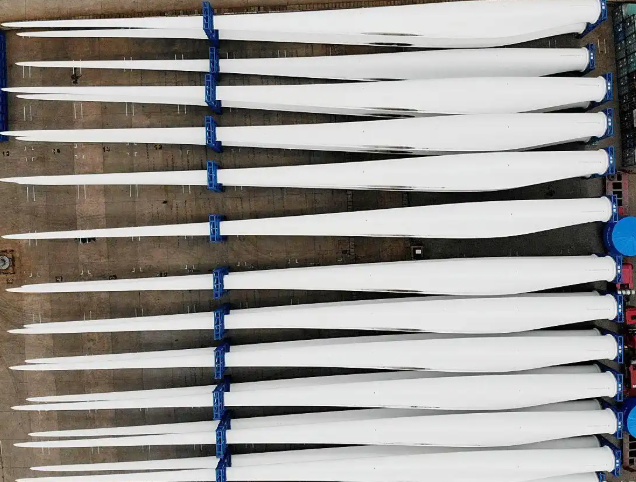
技术突破:复合材料重塑叶片性能边界
传统风电叶片多采用玻璃纤维增强复合材料,但随着风机单机容量向15兆瓦甚至20兆瓦级跃升,叶片长度突破120米,对材料的性能提出了更严苛的要求。新型复合材料的出现,尤其是碳纤维增强复合材料与高性能树脂基体的结合,为叶片制造带来了革命性变化。以某研究机构研发的碳纤维主梁叶片为例,其采用真空灌注成型工艺,通过优化纤维排布与树脂浸润,使叶片重量较传统玻璃钢叶片降低20%以上,同时抗疲劳性能提升3倍,可承受25年全生命周期的复杂海洋环境考验。更值得注意的是,这种材料在低温、高盐雾的恶劣条件下仍能保持结构稳定性,有效解决了传统叶片因腐蚀导致的寿命缩短问题。
工艺革新:从实验室到产业化的跨越
新型复合材料的优势需通过先进的制造工艺才能转化为实际生产力。在江苏盐城的一座现代化工厂内,123米长的超长叶片正通过拉挤成型与真空灌注技术实现规模化生产。拉挤工艺将碳纤维预浸料制成标准化型材,再通过叠层灌注形成主梁结构,使纤维体积含量提升至60%,结构强度提高40%;而真空灌注系统则通过多通道同步注胶,确保树脂分布均匀性达98%以上,彻底解决了传统手糊工艺易产生的气泡缺陷。更关键的是,国产碳纤维产能的突破使原材料成本较进口产品降低40%,结合碳玻混杂技术,叶片主梁成本下降25%,为规模化应用扫清了经济性障碍。
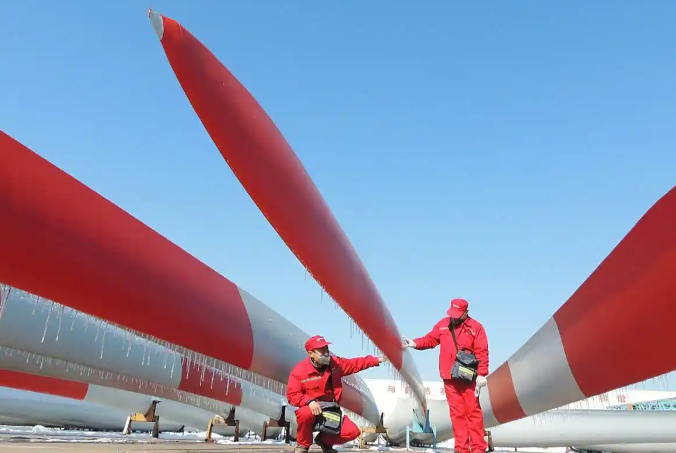
规模化效应:成本下降与效率提升的双赢
随着生产线的自动化升级,叶片制造效率实现质的飞跃。某企业通过引入智能铺层机器人与在线检测系统,使单班次叶片产量从传统的0.5支提升至2支,良品率从85%攀升至98%。这种效率提升直接反映在项目经济性上:以广东阳江的17兆瓦漂浮式风电项目为例,采用新型复合材料叶片后,单机年发电量达6800万千瓦时,可满足4万户家庭年用电需求,而叶片采购成本较五年前下降35%。更深远的影响在于,规模化生产推动了全产业链协同创新——从碳纤维原料供应商到叶片模具制造商,再到风电整机厂商,一个覆盖材料、装备、运维的完整产业生态正在形成。
绿色未来:可回收材料引领循环经济
在追求性能与成本的同时,行业正将目光投向叶片的全生命周期管理。某研究团队成功开发出可回收热塑性树脂叶片,通过化学解聚技术实现95%的材料回收率,彻底改变了传统环氧树脂叶片“填埋难、焚烧污”的困境。更令人振奋的是,木制风电叶片原型已在德国陆上风电场完成测试,这种以层压单板木材为原料的叶片不仅可100%回收,还通过免模具生产工艺降低了30%的制造成本。这些创新预示着,未来的风电叶片将在性能、成本与环保之间实现完美平衡。
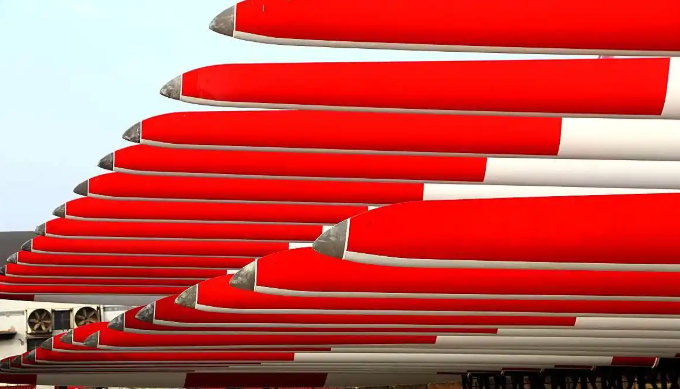
站在2025年的时间节点回望,新型复合材料的规模化应用已成为海上风电产业升级的关键转折点。它不仅解决了超大型叶片“轻量化”与“高强度”的矛盾,更通过工艺革新与成本控制,让海上风电真正实现“平价上网”。随着广东、江苏等省份深远海项目的加速推进,一个万亿级的蓝色能源市场正在崛起,而新型复合材料正是托起这一市场的“隐形翅膀”。