在全球航空业追求更高效、更环保的发展目标下,热塑性复合材料凭借其独特的性能优势,正成为推动航空制造技术变革的关键力量。从机身结构到发动机部件,从制造工艺到回收利用,这种材料正在重塑航空领域的生产模式与应用边界。
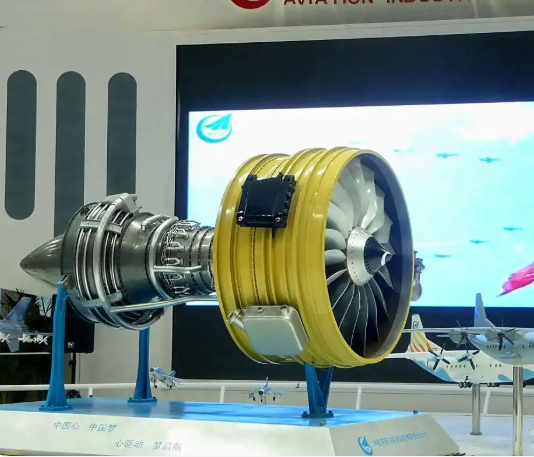
一、材料特性:轻量化与高性能的完美平衡
热塑性复合材料以热塑性树脂为基体,通过纤维增强技术制备而成,其核心优势在于密度低、强度高且可重复加工。数据显示,其密度仅为钢材的1/5至1/6,比强度却远超铝合金和传统热固性复合材料。例如,碳纤维增强热塑性复合材料(CFRT)的比强度可达167 MPa·cm³/g,而硬铝合金仅为100 MPa·cm³/g。这种特性使其在保证结构强度的同时,能显著降低部件重量。
耐热性与耐腐蚀性是另一大亮点。高性能品种可在150℃至250℃下长期工作,耐化学腐蚀性优于热固性材料,尤其适用于海洋和高温环境。此外,其线膨胀系数比未增强塑料低1/4至1/2,尺寸精度更高,导热系数与热固性材料相近,电性能还可通过添加导电填料进行设计。
最引人注目的是其环保特性。废料可通过熔融重塑实现100%回收,符合航空业减碳趋势。相比热固性材料难以降解的缺陷,热塑性复合材料在全生命周期管理中展现出显著优势。
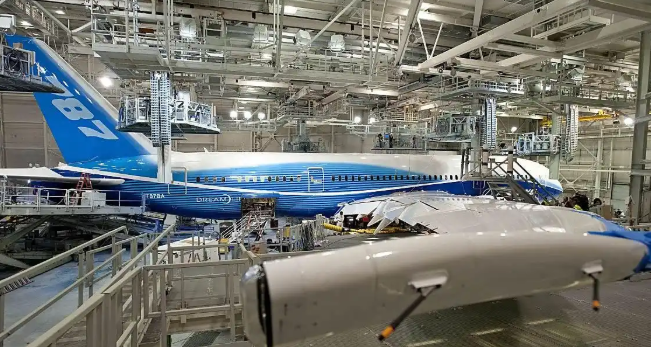
二、应用场景:从主承力结构到发动机部件的全面渗透
在航空主承力结构中,热塑性复合材料已实现突破性应用。空客A350的机身卡箍采用碳纤维织物增强聚苯硫醚(PPS)材料,减重30%的同时提升抗疲劳性能。湾流G650公务机的方向舵和升降舵则通过感应焊接工艺替代传统铆接,制造效率提升80%,500余架飞机已验证其可靠性。更引人注目的是空客“新A320”项目,其直径4米、长8米的筒体试验件全部采用热塑性复合材料制造,通过焊接工艺实现无金属紧固件装配,减少90%的制造步骤。
发动机领域的应用同样令人瞩目。航空发动机短舱进气道降噪声衬采用碳纤维增强聚醚酰亚胺(PEI)蜂窝结构,已在空客A380上商业化应用,有效降低噪音的同时提升结构效率。反推力装置则探索使用聚醚醚酮(PEEK)和聚醚酮酮(PEKK)基复合材料,满足短时耐高温需求。空客H-160直升机更将碳纤维增强PEEK应用于旋翼桨毂中央件,在减重50%的同时提高损伤容限。
内饰与次结构部件的轻量化转型也在加速。座椅骨架、门内板等部件通过玻璃纤维增强聚丙烯(PP)或尼龙实现减重20%-40%,某型客机内饰采用连续纤维增强热塑性复合材料后,整体重量降低25%,且具备更好的耐候性。

三、工艺创新:焊接技术与自动化成型的突破
热塑性复合材料的加工工艺革新是推动其应用的关键。感应焊接、电阻焊接等技术已成熟应用于主承力结构,例如空客A320筒体试验件通过焊接实现无铆钉装配,焊接强度达到母材的95%以上。更先进的原位聚合注射浸渍成型(In situ T-RTM)技术将成型周期缩短至60-120秒,成本降低40%,已在汽车制动踏板等部件中实现批量生产。
自动化成型技术同样取得显著进展。连续纤维增强热塑性复合材料(CFRT)的自动铺带技术结合3D打印,可制造复杂曲面结构,如发动机挂架肋板。某企业开发的冷隔膜模压成型技术,通过红外加热和惰性气体加压,实现高精度部件的一次成型,已应用于直升机外壳制造。
四、挑战与未来:认证、成本与应用扩展
尽管优势显著,热塑性复合材料的推广仍面临挑战。新材料认证周期长是主要障碍,例如焊接结构的认证需建立统一测试标准,欧洲已推进相关认证体系。成本优化方面,通过规模化生产(如东丽TC1225 CF/LM PAEK带材)和国产预浸料突破,高端制品成本已降低30%,但进一步普及仍需技术突破。
未来应用前景广阔。到2030年,航空发动机中热塑性部件质量占比预计达5%,2040年提升至25%,重点扩展至风扇外壳、分流环等冷端部件。俄罗斯联合发动机制造集团(UEC)已在开发热塑性材料的模压与焊接工艺,计划用于PD-14、PD-8等新一代发动机。更值得期待的是,连续增强纤维熔融沉积3D打印与自动铺带技术的结合,将推动复杂结构的一体化成型,而材料循环再生利用技术的成熟,将进一步强化其环保优势。
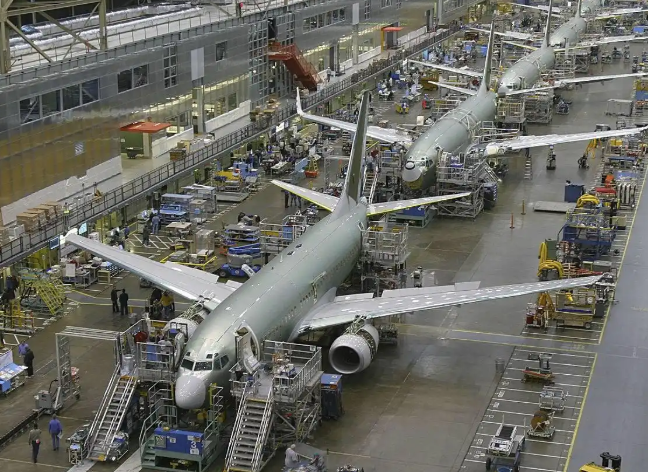
五、结语:重塑航空制造的未来
热塑性复合材料正以革命性的姿态改变航空制造的格局。从机身到发动机,从制造到回收,其轻量化、高性能和环保特性为行业提供了全新解决方案。随着工艺的持续创新和成本的逐步降低,这种材料有望在更多领域实现规模化应用,推动航空业向更高效、更可持续的方向发展。未来,热塑性复合材料不仅是技术的突破,更是航空制造理念的一次深刻变革。