在全球能源转型与"双碳"战略的驱动下,新能源汽车产业正经历从政策驱动向市场驱动的深刻变革。动力电池作为电动汽车的核心部件,其系统重量占整车比重达30%-40%,直接制约着续航里程与能效表现。传统金属材料在轻量化潜力与功能集成方面遭遇瓶颈,而复合材料凭借其可设计性强、比强度高、耐腐蚀性好等特性,成为突破技术壁垒的关键路径。当前研究聚焦于材料体系创新、结构优化设计及制造工艺升级三大维度,推动动力电池系统向更轻、更安全、更高效的方向演进。
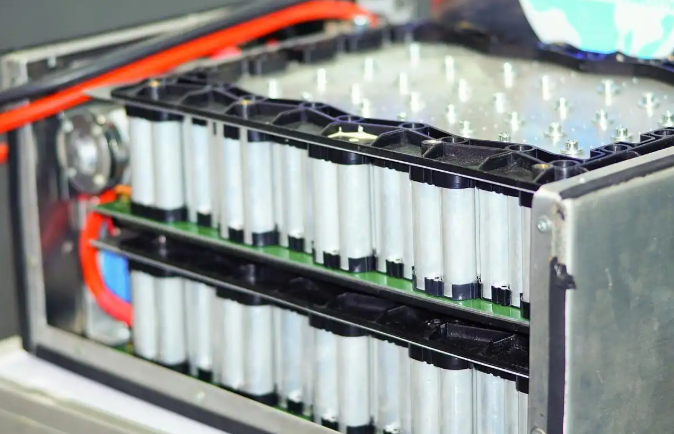
在材料应用领域,碳纤维增强复合材料(CFRP)与玻璃纤维增强复合材料(GFRP)形成差异化应用格局。CFRP以密度1.7g/cm³、抗拉强度超1700MPa的性能优势,在高端车型电池箱体中实现突破性减重。典型案例显示,采用CFRP的35L电池箱体壁厚仅2mm,重量较钢制箱体降低80%,同时承受200kg以上载荷。热塑性复合材料体系的突破尤为显著,如聚醚醚酮(PEEK)基CFRP在123MPa弯曲应力下仍保持结构完整性,500次循环后容量保持率达92%。玻璃纤维复合材料则通过短切纤维增强与混杂编织技术,在方形电池壳体中实现5MPa以上的粘接强度,配合环氧结构胶在-40℃至85℃温域内保持优异耐冲击性。新型基体材料开发方面,双酚A型环氧树脂经纳米二氧化硅改性后,耐化学腐蚀性能提升30%,在模拟海水环境中的疲劳寿命测试中,10^6次循环后强度保留率仍高于85%。
结构创新呈现多维度突破,夹芯结构与拓扑优化成为主流方向。热塑性复合材料蜂窝夹芯结构通过三维点阵芯材设计,使截面惯性矩提升40%,在120-180℃固化温度梯度下实现1.5m/min的拉挤速度。德国Fraunhofer研究所开发的连续纤维增强热塑性塑料(CFRTP)三明治结构,集成相变材料(PCM)实现热存储功能,在快速充电过程中可降低电芯温度梯度达40%。模块化设计理念在福特F-150Lightning皮卡中得以验证,铝挤压成型件与冲压件通过激光复合焊连接,在保证强度的同时使电池附加重量控制处于行业领先水平。功能集成方面,马勒公司研发的纤维增强塑料电池箱体将热管理模块嵌入结构层,采用电介质流体直接接触电芯的设计,在减少40%电池容量的同时实现快充能力提升,系统重量优势转化为续航里程增加。
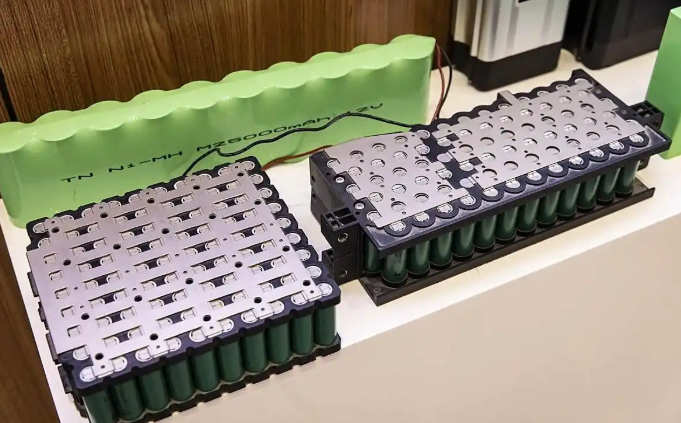
制造工艺升级呈现自动化与数字化融合趋势。真空灌注成型技术通过三维流场仿真模型,将树脂流动缺陷率从15%降至2%以下,在5000吨级化学品船液货舱改造项目中实现6块模块拼接装配,精度达±1mm。3D打印技术突破传统工艺局限,上海大学采用气溶胶喷射工艺制造的全固态电池(ASSB)电极,在10mg/cm²质量负载下实现160mAh/g比容量,离子电导率突破10^-3S/cm。激光烧结3D打印技术应用于Johnson Matthey电池组件生产,使年产能突破350万块,生产周期缩短60%。连接技术方面,丙烯酸结构胶在圆柱电池导电片粘接中实现低气味、耐疲劳性能优化,UV胶在方形电池底板固定中达到V0级阻燃标准,配合环氧保护胶形成多层级密封体系。
标准化建设与智能监测构成技术落地保障。国际标准方面,IEC62660系列标准覆盖单体性能测试到系统安全规范,ISO12405-4:2018将测试项拓展至动态工况参数评估。国内GB38031-2020强制性标准对热扩散安全性提出严苛要求,推动行业建立涵盖电性能、安全、寿命的三维评价体系。智能监测领域,光纤光栅传感器阵列嵌入复合材料结构,实时采集应变与温度数据,在某港口实际运行中成功预警3次裂纹扩展事件,将设备检修周期从6个月延长至18个月。人工智能与3D打印的深度融合,通过优化电极粒径设计减少离子扩散距离,使锂离子电池电化学性能提升20%以上。
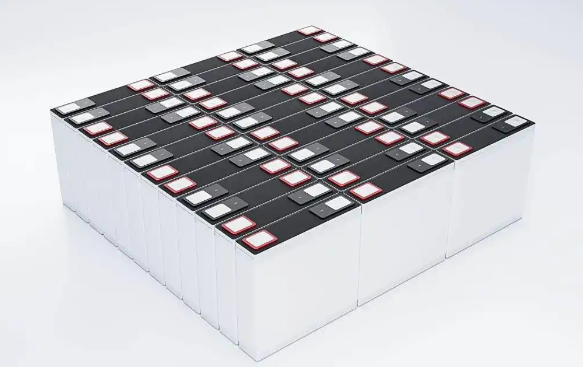
当前研究呈现三大趋势:一是多材料集成化,CFRP与铝合金的复合应用在宝马i系列中实现15%重量优化;二是制造智能化,自动铺带技术(AFP)在A350机翼制造中的成功经验正移植至电池箱体生产;三是回收体系化,热塑性复合材料熔融再加工技术使材料利用率提升至95%。这些进展不仅推动动力电池系统比能量密度突破300Wh/kg,更使整车能效提升12%,碳排放减少2000吨/年。随着15MW级海上风电机组与深空探测任务的推进,复合材料在极端环境下的应用研究持续深入,-60℃低温冲击强度已突破200kJ/m²,为构建更绿色、更智能的能源生态系统提供物质基础。