在航空航天领域,轻量化始终是技术突破的核心方向。传统制造工艺中,脱模环节依赖的溶剂型脱模剂虽能实现基础功能,却带来VOC排放超标、表面缺陷率高、生产效率受限等痛点。水性脱模技术的崛起,以环保性与功能性双重突破,为飞行器减重与性能提升提供了革命性解决方案。

技术革新:从溶剂到水性的跨越
水性脱模剂以水为分散介质,通过纳米级乳化技术将活性成分均匀分散,形成致密稳定的隔离膜。相较于传统油性脱模剂,其核心优势体现在三个方面:
环境友好性:水性体系将VOC排放量降低90%以上,完全规避闪燃风险,符合欧盟REACH法规及中国"双碳"战略要求。某汽车企业一体化压铸产线实测显示,切换水性脱模剂后,车间非甲烷总烃浓度从120mg/m³降至15mg/m³。
表面质量控制:乳液粒径控制在0.6μm以下,确保涂层均匀性。在飞机蒙皮复合材料制造中,该技术使表面气孔率下降70%,大幅减少后续修补工序,间接实现结构减重。
工艺兼容性:免固化特性缩短模具准备时间80%,配合微量喷涂系统,单次涂覆可支持百次以上脱模循环,显著提升生产节拍。
减重机理:多维度效能提升
水性脱模技术通过三大路径实现减重目标:
材料利用优化:精准脱模减少边缘废料,在某型直升机旋翼部件生产中,材料利用率从82%提升至93%,单个部件减重达4.7kg。
结构简化:配合一体化压铸工艺,水性脱模剂解决超大型构件脱模难题。某新能源汽车后地板压铸件实现74个零件集成,减重30%的同时,脱模成功率保持99.2%。
性能补偿设计:低转移特性避免脱模剂残留对复合材料层间结合的影响,允许设计师减少3%-5%的冗余厚度。在卫星结构件制造中,该技术使碳纤维层板厚度从2.8mm优化至2.3mm,整体减重18%。
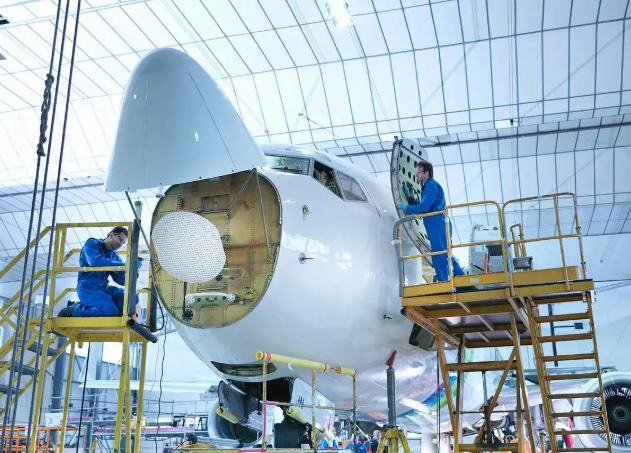
行业应用:从实验室到产线的突破
精密构件加工:纳米纤维素增强涂层在卫星光学仪器支架制造中实现亚微米级表面精度,替代传统石墨涂层,减重同时提升热控性能。
未来图景:智能与可持续的融合
技术演进呈现三大趋势:
响应型材料开发:温敏性脱模剂可依据模具温度自动调节润滑性,在-40℃至200℃宽温域内保持稳定,适配柔性生产线需求。
生物基原料替代:以淀粉衍生物为基础的第三代水性脱模剂已完成中试,生物降解率达92%,预计2028年实现商业化。
数字孪生集成:通过物联网传感器实时监测脱模剂膜厚与状态,结合AI算法预测模具维护周期,某试点产线已实现停机时间减少65%。
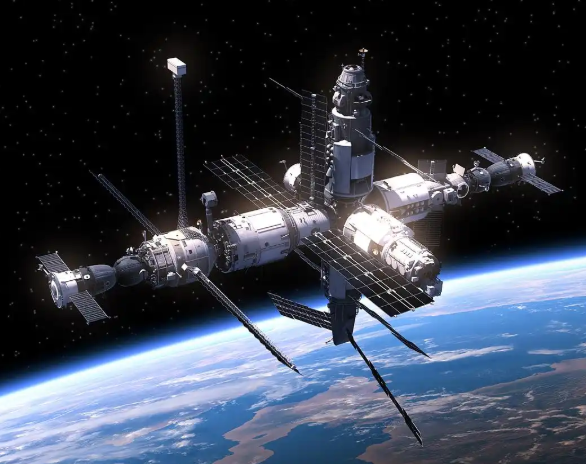
水性脱模技术不仅重构了制造工艺的环保底线,更通过材料科学、表面工程与智能控制的深度融合,为飞行器设计开辟了全新的减重空间。随着纳米改性、生物基材料等前沿技术的突破,这项绿色工艺将持续推动航空航天制造向更轻、更强、更可持续的方向演进。