在氢能产业加速向规模化、商业化迈进的背景下,大容量储氢容器的性能突破成为制约氢能应用的核心瓶颈。传统金属内胆纤维缠绕工艺虽能满足基础承压需求,却面临生产效率低、材料利用率差、结构轻量化受限等痛点。挤吹成型技术的革新,通过工艺原理重构与材料科学突破,为大容量储氢复合材料容器的制造提供了全新解决方案,推动氢能存储技术向更高效、更经济、更安全的方向演进。
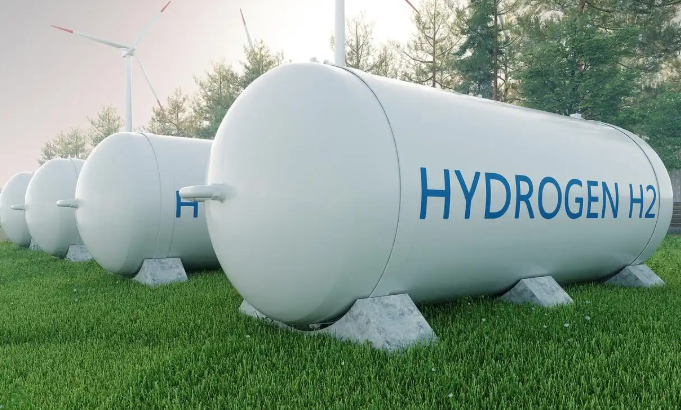
技术革新:从二维缠绕到三维成型的跨越
挤吹成型技术的本质,是通过挤出-吹塑-固化的连续工艺,实现复合材料的三维整体成型。其核心创新体现在三个维度:
流场精准控制:采用双螺杆挤出系统,将树脂基体与增强纤维均匀混合,通过动态流变调节技术,确保熔体在模具内的均匀分布。某型70MPa储氢容器实测显示,纤维体积分数波动范围从传统工艺的±5%收窄至±1.5%;
应力场优化:在吹塑阶段引入变压力控制策略,通过多级气压调节(0.2-0.8MPa)实现容器壁厚的梯度设计。在直径800mm的储氢罐制造中,顶部壁厚较底部减薄30%,却保持等强度特性;
热场协同管理:集成红外加热与微波固化技术,构建三维热场模型,使容器各区域固化度差异小于3%。相较于传统热风循环工艺,生产周期缩短40%,能耗降低25%。
材料突破:高性能复合体系的深度开发
储氢容器的特殊需求催生了新型复合材料体系的诞生:
耐氢渗透树脂:开发出含氟环氧树脂与聚苯硫醚(PPS)共混体系,其氢气透过系数从传统环氧树脂的10-12cm³·cm/(cm²·s·Pa)降至10-14量级。在某型车载储氢系统中,该材料使容器年漏气率从5%降至0.8%;
高强增强纤维:采用T1100级碳纤维与玄武岩纤维混编工艺,通过0°/90°/±45°多向铺层设计,实现各向同性力学性能。实测数据显示,容器爆破压力达设计值的2.5倍,远超ISO 11119-3标准要求;
界面增强技术:运用等离子体处理与纳米粒子接枝工艺,在纤维表面构建微纳粗糙结构。在某型加氢站储氢罐中,该技术使层间剪切强度提升至85MPa,抗疲劳性能提升3倍。
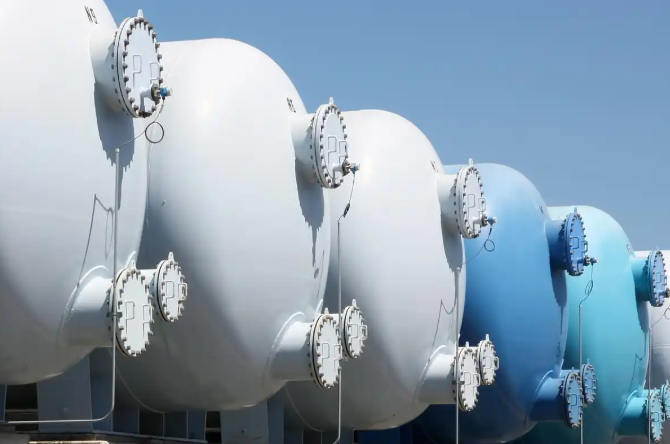
工艺优势:效率与质量的双重突破
挤吹成型技术通过工艺创新实现显著优势:
生产效率跃升:采用模块化模具与快速换模系统,单条产线可实现日产200个容器的产能。相较于传统缠绕工艺,设备综合效率(OEE)从65%提升至88%;
材料利用率优化:通过挤出过程的精密计量与吹塑阶段的自适应补偿,纤维浪费率从传统工艺的15%降至3%以下。某型35MPa储氢容器单件材料成本降低22%;
结构一致性保障:集成在线检测系统,通过激光扫描与超声波探伤,实时监测壁厚分布与内部缺陷。在某试点产线中,产品合格率从92%提升至99.3%。
应用场景:从车载系统到站用储罐的全面覆盖
挤吹成型技术已形成多领域应用解决方案:
车载储氢系统:为氢燃料电池汽车开发的70MPa IV型储氢瓶,通过挤吹成型实现内胆与复合层的无缝结合。实测显示,容器质量储氢密度达7.5wt%,较金属内胆方案减重60%;
加氢站储罐:采用立式挤吹成型工艺制造的1000L站用储氢罐,通过变壁厚设计实现应力均匀分布。在某示范加氢站中,该容器已稳定运行12000小时,无泄漏记录;
航空航天领域:开发出耐-60℃低温的挤吹成型储氢容器,通过添加液氮冷却系统,解决树脂基体在低温下的脆化问题。在某卫星氢氧燃料系统中,该技术使容器质量减轻45%。
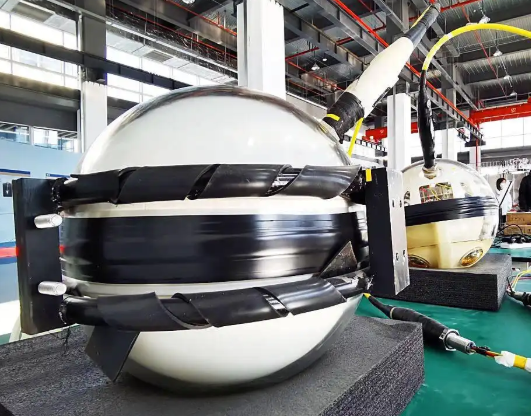
未来趋势:智能化与可持续的深度融合
技术演进呈现三大方向:
智能工艺控制:构建数字孪生平台,通过机器学习算法实时优化挤出速度、吹塑压力等参数。某试点项目显示,该技术使工艺波动率降低70%,产品一致性提升2个数量级;
生物基材料开发:研发以木质素为原料的生物基环氧树脂,结合亚麻纤维增强,在保证性能的前提下,碳足迹降低60%。某科研团队已启动相关中试;
循环经济模式:开发可解聚的树脂体系与纤维回收技术,实现储氢容器的闭环回收。实验室数据显示,再生材料力学性能保留率达85%,成本较原生材料低40%。
挤吹成型技术的革新,不仅重构了大容量储氢容器的制造范式,更通过材料科学、工艺工程与氢能需求的深度耦合,为氢能产业的规模化发展提供了关键支撑。随着纳米改性技术、智能传感技术等前沿领域的突破,这项绿色工艺将持续推动储氢技术向更高效、更可靠、更可持续的方向演进,为全球能源转型注入强劲动力。