在航空航天、汽车制造及新能源领域,轻量化与高性能材料的融合已成为技术突破的关键方向。热塑性复合材料凭借其可回收性、高强度及耐腐蚀等特性,正逐步替代传统金属材料,而智能感应焊接技术的成熟,则为这类先进材料的规模化应用提供了核心支撑。该系统通过电磁感应原理与智能化控制技术的深度融合,实现了复合材料连接工艺的精准化、高效化转型。
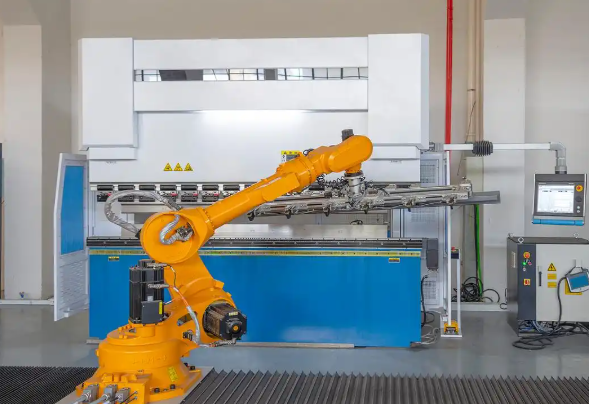
技术原理与系统架构
热塑性复合材料智能感应焊接系统的核心在于利用电磁感应效应实现非接触式加热。当高频交流电通过导电线圈时,会在焊接区域产生时变磁场,促使碳纤维增强层压板中的导电纤维产生涡流,从而快速加热聚合物基体至玻璃化温度或熔点以上。相较于传统电阻焊需插入加热元件的方式,感应焊接通过闭环控制的磁场分布,能够实现对复杂曲面及异形结构的均匀加热。例如,德国航空航天中心在空客A320后压力舱壁项目中,采用碳纤维焊接元件与感应加热技术,成功将8个碳纤维增强聚苯硫醚(PPS)部件通过7条1.5米长的焊缝连接,焊接强度经测试达到静态层间剪切强度(SLS)稳定高值,技术成熟度(TRL)达到5级。
系统智能化体现在多模态传感与AI算法的集成应用。焊接过程中,红外热像仪实时监测焊接界面温度分布,光纤传感器捕捉压力变化数据,结合机器视觉系统对焊缝形貌进行动态分析。这些数据输入至基于生成对抗网络(GANs)的AI模型,通过对比历史工艺参数与缺陷模式,实时调整线圈功率与机器人行进速度。在荷兰Fokker公司为湾流G650飞机方向舵生产的案例中,该系统通过闭环控制将焊接缺陷率降低至0.3%,较传统工艺提升40%效率。

工艺创新与质量控制
连续超声波焊接技术的突破进一步拓展了系统应用场景。德国航空航天中心开发的机器人焊接系统,通过末端执行器搭载超声焊极,在Z型桁条焊接中实现两层材料覆盖与第三层薄条的精准叠加。该工艺结合AI算法对振动幅度、频率及焊接时间的优化,使碳纤维增强聚醚酰亚胺(PEI)的搭接剪切强度提升50%。值得注意的是,输入能量需严格控制在1000焦耳以内,以避免接头孔隙化——这一临界值通过深度学习模型实现动态预警。
在电阻焊接领域,静态与连续两种工艺的协同应用成为趋势。中国航空制造技术研究院开发的航空用高性能热塑性复合材料焊接技术,通过电流-电压双参数监控,结合气动千斤顶压力控制系统,在焊接桥接区域实现±2%的尺寸精度控制。该技术已应用于某型直升机主承力结构件,经无损检测验证,焊缝密封性达到航空标准要求。
行业应用与经济效益
航空航天领域的应用最具代表性。在H2020 TOD研究项目中,采用碳纤维织物增强PPS材料焊接的飞机舱门,较传统金属结构减重12%,成本降低18%。法国ISW集团开发的移动基座感应焊接系统,通过红外摄像机监测焊接头速度与温度分布,在DEWTECOMP项目演示中,成功实现20mm×25mm焊接区域的精准控温,表面温度误差控制在±5℃以内。这种技术已被雷神技术公司应用于曲面面板焊接,配合光纤温度传感技术,使焊接界面温度均匀性提升30%。
汽车工业的轻量化需求推动该技术向民用市场渗透。君华股份展示的CF/PEEK缠绕铺丝设备,通过激光辐射与感应焊接的组合工艺,实现新能源汽车电机转子部件的高效生产。据测算,采用该系统的生产线较传统工艺单件成本降低22%,生产节拍缩短至45秒/件。在2025年JEC World展会上,多家企业展出的长纤维增强接骨板医疗器件,通过直接成型与感应焊接技术,将生产效率提升3倍,产品合格率突破99%。
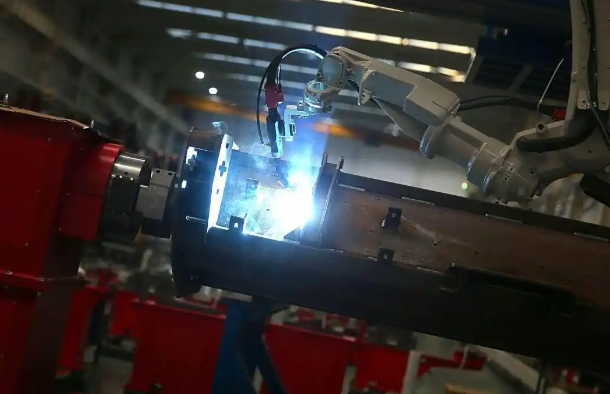
技术挑战与发展趋势
尽管取得显著进展,该领域仍面临材料兼容性与工艺复杂性的挑战。热塑性复合材料与金属的异种材料焊接需解决热膨胀系数差异问题,当前研究聚焦于过渡层设计与上浆剂改性。南京航空航天大学开发的界面增强技术,通过纳米粒子改性使碳纤维与PEEK的界面剪切强度提升35%。此外,复杂曲面构件的焊接均匀性控制仍是技术难点,中国复合材料工业协会正在制定《热塑性复合材料感应焊接工艺规范》,拟通过标准化推动技术普及。
展望未来,工业4.0与AI技术的融合将加速系统智能化升级。基于数字孪生的虚拟调试技术已在空客MFFD项目中试点,通过仿真模型预测焊接变形量,使实际生产中的调整次数减少70%。边缘计算与物联网的结合,则使焊接设备能够实时接入云端工艺数据库,实现全球范围内的参数优化共享。随着低烟尘焊材与自保护药芯焊丝的普及,该技术有望在2030年前实现焊接过程零有害排放,推动复合材料制造向绿色低碳转型。
这项技术的突破,不仅重塑了复合材料连接工艺的边界,更通过智能化与绿色化的双重驱动,为高端制造业的转型升级提供了关键支撑。随着技术成熟度的持续提升,其应用范围必将从航空航天向轨道交通、新能源装备等领域加速拓展。