在轻量化材料革命的浪潮中,热塑性树脂基碳纤维预浸料凭借其可回收性、高强度及耐腐蚀等特性,正逐步成为航空航天、汽车制造及新能源领域的关键基础材料。其工业化生产技术的突破,不仅推动了复合材料制造工艺的革新,更构建起从原料制备到终端应用的全产业链技术体系。
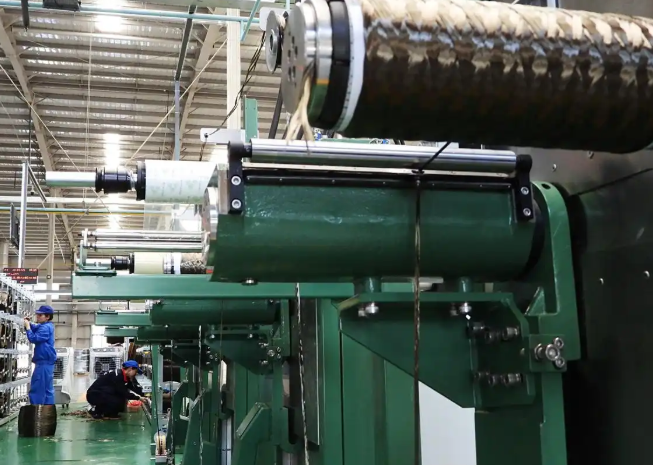
技术原理与工艺体系
热塑性预浸料的制备本质是实现碳纤维与树脂基体的均匀浸润与结构稳定化。当前主流工艺可分为预浸渍法与后浸渍法两大类,其中熔融浸渍法通过双螺杆挤出机将树脂加热至熔融态,借助动态接触实现纤维束的充分浸润。例如,PEEK树脂在360-380℃熔融状态下,通过优化模具结构与纤维分散程度,可制备出孔隙率低于1.33%的高性能预浸带。悬浮热熔法则采用粉末流化技术,将微米级树脂颗粒均匀包裹纤维束,经加热熔融后实现短流程浸渍,该工艺已实现PEEK、PPS预浸料的规模化生产,树脂含量精度可控在±2%以内。
在工艺创新层面,自动铺放原位固结技术通过激光加热(400-420℃)与压辊加压(10-15N)的协同控制,实现了铺放与固化的一体化。德国DLR研究所采用该技术成功制备8米长机身蒙皮,层间剪切强度突破68MPa。国内研究则通过优化激光功率(6kW)与压辊压力(1500N),使CF/PPS复合材料的层间结合度达85%,性能接近热压罐成型水平。此外,3D打印技术借助熔融沉积(FDM)与选择性激光烧结(SLS),在医疗植入体等定制化领域展现出独特优势,双喷头技术使CF/PA6打印件拉伸强度提升至110MPa。
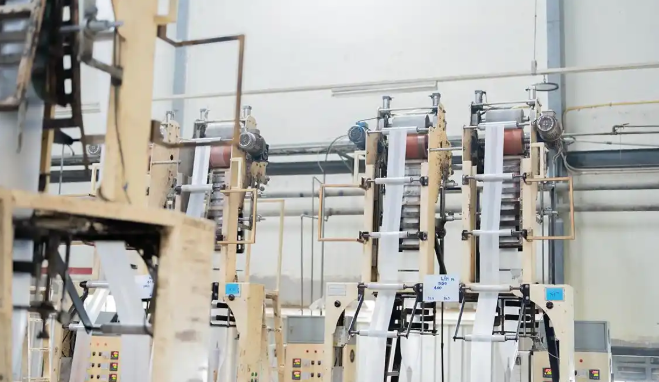
质量控制与工艺优化
预浸料的质量控制贯穿生产全流程。外观检测要求纤维平行密排,无交叉松散,树脂分布均匀且无固化颗粒。物理性能方面,单位面积质量(ρAP)与含胶量(R)需通过纤维展开系统与在线称重装置实现闭环控制,某研究机构开发的分散剂复配技术使悬浮液稳定时间延长至50分钟,纤维体积分数稳定在60%以上。成型工艺性能则通过凝胶时间(120-180秒)、树脂流出量(5-8%)及挥发分含量(<0.5%)等参数监控,采用红外光谱与热重分析联用技术,可实时检测树脂降解程度。
熔融动力学调控成为工艺优化的核心。温度场精准控制(±5℃)通过嵌入式热电偶与循环测温系统实现,压力匹配(0.3-0.8MPa)则结合有限元模拟优化模具流道设计。界面改性方面,某团队开发的等离子体处理技术使碳纤维表面能提升至72mN/m,结合硅烷偶联剂使用,使CF/PEEK层间剪切强度提升23%。
产业化应用与经济效益
在航空航天领域,热塑性预浸料已应用于空客A350的货舱地板与垂尾结构,较传统热固性材料减重18%,成本降低22%。汽车工业中,纳磐新材料开发的CF/PPS预浸带应用于新能源汽车动力电池包外壳,在-40℃至150℃温域内保持尺寸稳定,冲击强度达85kJ/m²。某主机厂采用热塑性预浸料制造电机端盖,通过模压成型(310-330℃加热温度、9MPa压力)实现孔隙率控制<1%,生产节拍缩短至45秒/件。
市场数据印证了技术突破的产业价值。2024年全球预浸料市场规模达131亿美元,其中热塑性预浸料复合年增长率达11.9%,预计2032年突破268亿美元。某咨询机构报告显示,采用悬浮热熔法与自动铺放技术的生产线,设备综合效率(OEE)提升至85%,单位能耗较传统工艺降低40%。
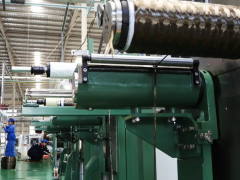
技术挑战与发展趋势
尽管取得显著进展,热塑性预浸料工业化仍面临多重挑战。高性能树脂体系开发方面,PEKK等新型树脂的熔融黏度仍高达500Pa·s,需通过支化改性与纳米填料复合实现流变性能优化。某研究团队开发的超支化PEEK树脂,在380℃时黏度降至180Pa·s,浸渍效率提升3倍。设备国产化方面,精密浸渍模具与激光加热系统的进口依赖度仍达65%,某企业通过3D打印技术制造的梯度孔隙模具,使纤维分散均匀性提升40%。
未来技术发展将呈现三大趋势:一是智能制造深度融合,基于数字孪生的虚拟调试技术已在空客MFFD项目试点,使实际生产中的调整次数减少70%;二是循环经济模式创新,某团队开发的化学回收技术可将废旧CF/PEEK预浸料分解为高纯度纤维与树脂单体,回收率达92%;三是多材料集成制造,某研究所开发的混杂纤维预浸料,通过碳纤维与玻璃纤维的层间梯度分布,使复合材料冲击后压缩强度(CAI)提升至320MPa。
这项技术的突破,不仅重塑了复合材料制造的工艺边界,更通过全产业链的协同创新,为高端制造业的转型升级提供了关键支撑。随着技术成熟度的持续提升,其应用范围必将从航空航天向轨道交通、新能源装备等领域加速拓展,最终实现材料性能、生产效率与环境效益的完美统一。