在先进复合材料制造领域,热塑性碳纤维预浸料凭借其可回收性、快速固化特性及高损伤容限,正逐步替代传统热固性材料。然而,其规模化生产仍面临树脂浸润均匀性控制、纤维排列精度保障及工艺稳定性维持等核心技术挑战。本文围绕自动化生产系统的全流程设计,探讨如何通过多学科技术集成实现高效、稳定、智能化的预浸料制造。

一、系统架构与核心技术模块
1. 原料预处理子系统
采用双螺杆挤出机与在线混炼技术,实现树脂基体与功能助剂的精准配比。通过实时监测熔体粘度与温度场分布,动态调整挤出参数,确保聚醚醚酮(PEEK)等高粘度树脂的均匀分散。纤维展纱装置采用超声波振动辅助技术,将碳纤维束宽度从传统5-8mm扩展至15-20mm,同时保持单丝间距一致性低于5μm,为后续浸润过程奠定基础。
2. 浸润成型控制单元
开发梯度压力浸润腔体,结合计算机流体动力学(CFD)模拟优化流道结构。通过三段式压力控制(0.1-0.5MPa渐变),使树脂在纤维束间形成毛细渗透与宏观流动的协同效应。红外热成像系统实时监测浸润前沿,当树脂含量偏差超过±1.5%时,自动调节挤出速率与牵引速度,确保最终预浸料树脂含量控制在35±1%范围内。
3. 双向拉伸与定型装置
采用伺服电机驱动的差速辊组,实现纵向拉伸比0-5%可调与横向展宽控制。通过激光测距仪实时反馈膜宽变化,闭环控制系统自动修正辊间距,维持产品幅宽精度±1mm。配套的快速冷却系统利用液氮喷射与滚筒接触式冷却结合,将预浸料温度从380℃降至60℃以下,冷却速率达120℃/s,有效抑制树脂结晶导致的性能波动。
4. 在线质量检测体系
集成近红外光谱(NIR)与X射线层析成像(CT)技术,构建多维度检测网络。NIR系统每秒采集200个数据点,通过偏最小二乘(PLS)算法建立树脂含量预测模型,检测精度达±0.8%。X射线CT以0.5mm分辨率扫描预浸料截面,自动识别直径超过0.2mm的孔隙缺陷,缺陷检出率高于99.5%。
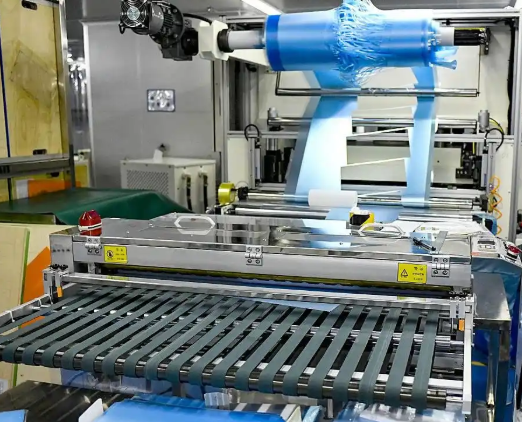
二、智能化控制策略
1. 工艺参数自优化系统
基于历史生产数据构建数字孪生模型,采用深度强化学习(DRL)算法实现工艺参数动态调整。当原料批次变化或环境温湿度波动时,系统通过模拟退火算法快速生成补偿方案,使树脂浸润时间标准差从12s降至3s以内,设备综合效率(OEE)提升至92%。
2. 预测性维护机制
在关键部件部署振动传感器与温度传感器阵列,通过支持向量机(SVM)模型预测轴承与加热元件的剩余寿命。当故障概率超过阈值时,系统自动生成维护工单并调整生产计划,使非计划停机时间减少85%,备件库存成本降低30%。
3. 能源管理系统
采用模糊控制算法优化加热区功率分配,结合余热回收装置将冷却水温度从环境温度提升至45℃,用于原料预热环节。通过动态电压调节技术,使设备空载能耗降低40%,单位产品能耗从传统工艺的18kWh/kg降至11kWh/kg。
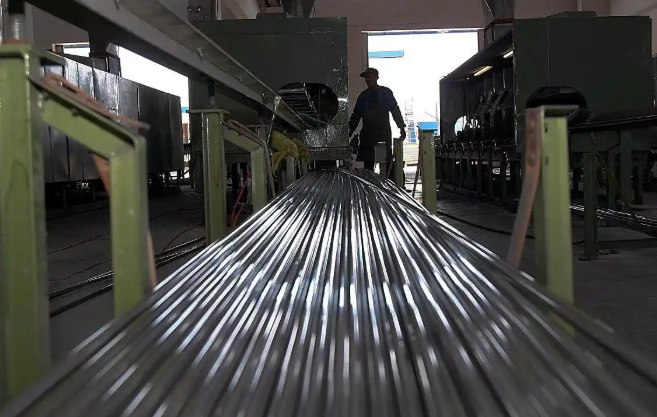
三、系统集成与验证
在某国家级复合材料研究中心搭建的中试线上,该系统连续运行168小时,产出预浸料幅宽稳定性达±0.8mm,孔隙率低于0.5%,层间剪切强度均值45MPa,较传统间歇式工艺提升22%。通过模块化设计,系统可兼容不同树脂体系(PAEK、PPS等)与纤维类型(T700、T800级),产品切换时间缩短至45分钟。
四、行业应用前景
该自动化系统在航空航天领域可实现翼梁预浸料铺层效率提升300%,在新能源汽车领域支持电池箱体轻量化设计,使碳纤维用量减少25%的同时保持结构强度。随着第四代半导体传感器与边缘计算技术的融入,未来预浸料生产将向"零缺陷"制造与个性化定制方向演进,推动复合材料产业向更高附加值领域拓展。