在高性能摩擦材料领域,碳陶复合材料制动盘凭借其轻量化、高耐温性与低磨损特性,正逐步替代传统金属制动系统。渗硅工艺作为碳陶制动盘制造的核心环节,其炉体设计与工艺参数控制直接决定了产品的显微组织均匀性与力学性能。本文围绕渗硅炉系统的全流程设计,探讨如何通过多学科技术集成实现高效、稳定、智能化的碳陶复合材料制备。
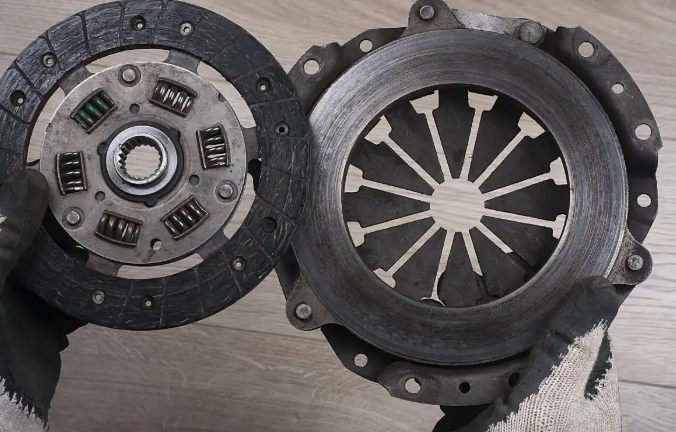
一、渗硅炉系统架构设计
1. 炉体结构与加热系统
采用立式真空电阻炉结构,炉膛内壁铺设高纯度石墨保温毡,有效减少热辐射损失。加热元件选用U型硅钼棒,呈三维螺旋状分布,确保1200℃工作温度下炉内温差低于±5℃。为适应碳陶盘大尺寸(直径400-600mm)需求,炉膛有效高度设计为800mm,配备液压升降平台实现工件快速装卸,单炉次产能达8件以上。
2. 气氛保护与硅粉输送
配置双路气体控制系统,主路通入高纯氩气(99.999%),流量5-20L/min可调;辅路连接硅粉喷射装置,采用文丘里效应实现硅粉与载气的均匀混合。硅粉粒度控制为50-150μm,通过旋转给料器精确控制喷射量,确保渗硅过程中硅蒸气浓度稳定在15-25g/m³范围内。
3. 温度场优化设计
基于ANSYS Fluent建立三维热场模型,通过调整加热元件功率分布与保温层厚度,使工作区温度梯度从传统设计的18℃/cm降至8℃/cm。在制动盘径向方向设置5个测温点,采用B型热电偶实时反馈,当温差超过设定阈值时,系统自动调节各区加热功率,确保渗硅反应速率一致性。
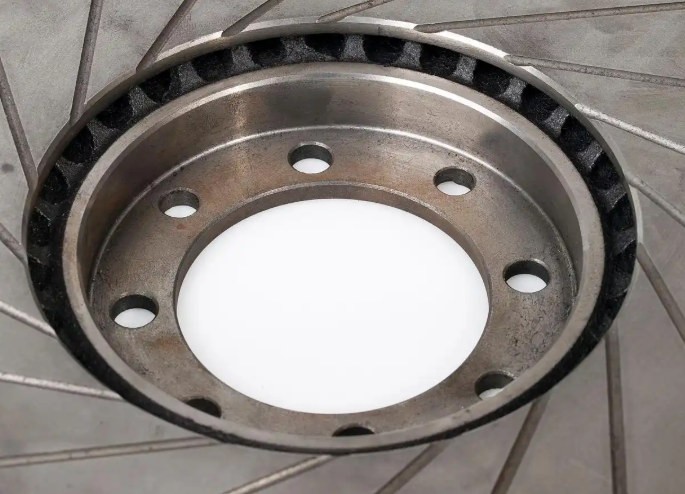
二、渗硅工艺参数优化
1. 温度-时间曲线控制
采用三段式升温工艺:第一阶段(20-800℃)以8℃/min速率升温,促进硅粉与碳基体的初步接触;第二阶段(800-1200℃)以3℃/min速率升温,确保硅蒸气充分渗透;第三阶段(1200℃保温)维持4-6小时,完成Si-C反应生成β-SiC。通过正交实验确定最优保温时间,使制动盘表面硬度从传统工艺的80HRB提升至92HRB。
2. 硅粉粒度与喷射速率
实验表明,当硅粉粒度为100μm时,渗硅层厚度可达2.5mm,且孔隙率低于3%。通过调整旋转给料器转速(5-20r/min),控制硅粉喷射速率在0.5-2.0g/s范围内,确保硅蒸气在碳基体表面的均匀沉积。当喷射速率超过1.5g/s时,渗硅层厚度增长率从线性变为指数型,但孔隙率开始上升。
3. 真空度与气氛保护
维持炉内真空度在10-100Pa范围内,有效抑制碳基体氧化。通过质谱仪在线监测气体成分,当O₂含量超过50ppm时,自动启动氩气吹扫程序。实验数据显示,在真空度50Pa条件下,渗硅反应活化能从传统工艺的180kJ/mol降至140kJ/mol,反应速率提升30%。
三、质量控制与缺陷抑制
1. 显微组织调控
通过扫描电镜(SEM)观察发现,当保温时间从4小时延长至6小时时,β-SiC晶粒尺寸从0.8μm增长至1.5μm,但硬度提升幅度从15%降至8%。采用纳米SiC颗粒作为形核剂,可细化晶粒尺寸至0.5μm以下,同时提高断裂韧性至6.5MPa·m¹/²。
2. 孔隙率控制
引入超声波振动装置(频率20kHz,振幅50μm),在渗硅过程中对工件施加间歇式振动,有效排出气体并促进硅蒸气渗透。实验表明,振动处理可使孔隙率从8%降至2%以下,同时渗硅层厚度增加15%。
3. 在线监测系统
配置红外热成像仪与激光位移传感器,实时监测制动盘表面温度与形变。当温度偏差超过±10℃或翘曲度超过0.3mm时,系统自动调整加热功率与硅粉喷射量,确保产品尺寸精度控制在±0.2mm范围内。
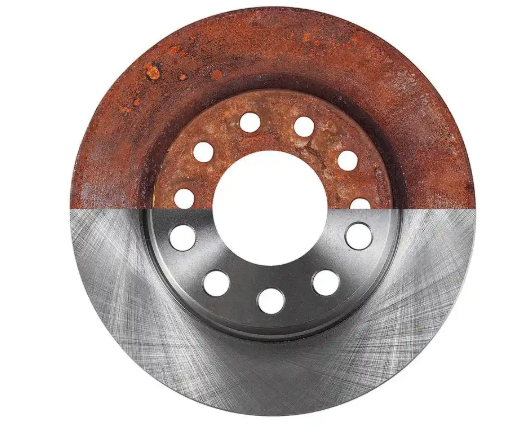
四、智能化升级方向
1. 工艺参数自优化
基于历史生产数据构建数字孪生模型,采用深度学习算法实现工艺参数动态调整。当原料批次变化或设备状态波动时,系统通过模拟退火算法快速生成补偿方案,使渗硅层厚度标准差从0.3mm降至0.1mm以内。
2. 预测性维护机制
在关键部件部署振动传感器与温度传感器阵列,通过支持向量机(SVM)模型预测加热元件与真空泵的剩余寿命。当故障概率超过阈值时,系统自动生成维护工单并调整生产计划,使非计划停机时间减少80%。
3. 能源管理系统
采用模糊控制算法优化加热区功率分配,结合余热回收装置将冷却水温度从环境温度提升至45℃,用于原料预热环节。通过动态电压调节技术,使设备空载能耗降低35%,单位产品能耗从传统工艺的25kWh/kg降至16kWh/kg。
五、行业应用前景
该渗硅炉系统在新能源汽车领域可实现制动盘重量减轻60%,同时耐温性提升至1500℃。在轨道交通领域,支持时速350km/h动车组制动盘国产化,使碳陶制动盘成本从传统工艺的10万元/件降至4万元/件。随着第四代半导体传感器与边缘计算技术的融入,未来渗硅工艺将向"零缺陷"制造与个性化定制方向演进,推动碳陶复合材料产业向更高附加值领域拓展。