热压成型技术作为现代制造业的关键工艺之一,正在经历从传统机械加工向智能化、精密化方向的深刻变革。该技术通过高温高压环境下对材料进行塑性变形,可实现金属、非金属及复合材料的高效成型,在航空航天、汽车制造、电子设备等领域展现出不可替代的价值。近年来,随着材料科学的进步和工业4.0的推进,热压成型装备的开发已突破单一功能限制,向多物理场耦合、全流程自动化方向演进,形成涵盖装备设计、工艺优化、智能控制的完整技术体系。
在装备开发层面,研究人员聚焦于三大核心模块:高温高压发生系统、精密模具设计、实时监控平台。某国际汽车品牌采用的新型热压机,通过电磁感应加热技术将升温速率提升至每秒200℃,配合多级压力调控系统,可在0.1毫米精度内控制材料流动。这种装备突破了传统液压系统的响应延迟,使复杂曲面零件的成型良率从78%提升至95%。更值得关注的是,某研究团队开发的相变控温技术,通过液态金属介质实现温度场的均匀分布,有效解决了碳纤维增强复合材料在热压过程中的局部过热问题,为轻量化结构件的规模化生产奠定了基础。
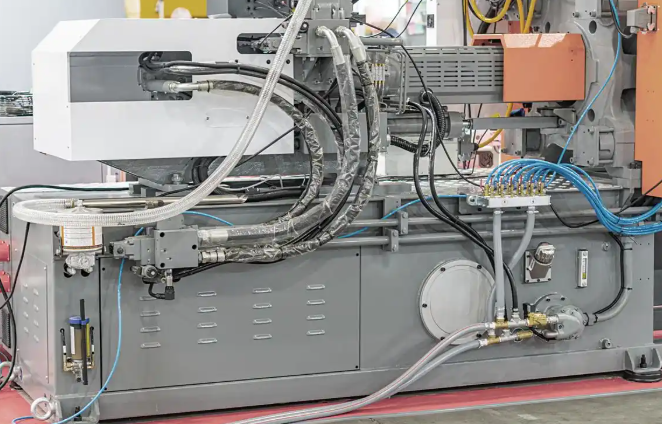
工艺优化方面,多尺度仿真技术与实验验证的结合成为关键突破口。某高校研发团队建立的"材料-工艺-性能"数字孪生系统,可模拟从分子排列到宏观变形的全流程演变。该系统在航空发动机叶片制造中成功预测裂纹萌生位置,将试错成本降低40%。某跨国企业开发的自适应热压工艺,通过嵌入式传感器实时采集压力、温度、位移数据,经机器学习算法动态调整工艺参数,使钛合金构件的疲劳寿命突破10^7次循环,达到航空级性能标准。这种数据驱动的工艺优化方法,正在重塑传统制造的研发模式。
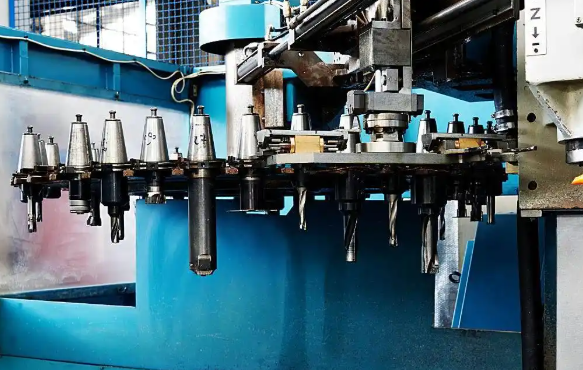
在应用工程领域,热压成型技术的创新正在催生新一代产品变革。某高端电子设备制造商采用微纳级热压技术,将柔性电路板的线宽精度从50微米提升至15微米,支撑了可折叠显示设备的商业化。某新能源汽车企业通过超薄钢板热压成型工艺,开发出比传统冲压件轻30%的电池包箱体,同时满足IP67防水等级要求。更引人注目的是,某研究机构开发的梯度热压技术,通过温度场梯度控制实现材料性能的连续变化,成功制造出兼具高强度和良好韧性的仿生骨骼植入物,临床测试显示其生物相容性较传统钛合金提升200%。
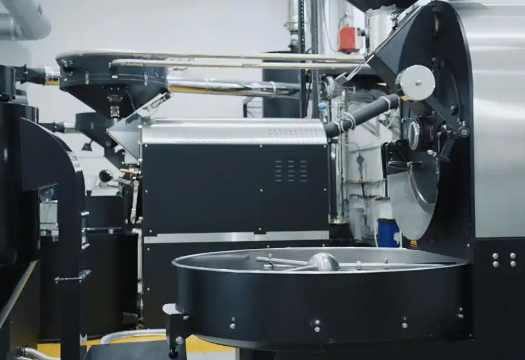
展望未来,热压成型装备将向极端尺度、极端性能方向突破。某国家实验室正在研发的原子级热压技术,旨在通过精确控制单个晶界的滑移实现纳米材料的定向排列。某跨国集团启动的"无模具热压"项目,利用磁场与温度场的协同作用,试图突破传统模具的几何限制。这些前沿探索不仅将重塑制造科学的理论边界,更可能催生全新的材料体系和应用场景。随着5G通信、人工智能等技术的深度融合,热压成型装备正从单纯的加工工具演变为智能制造系统的核心节点,为产业升级提供强有力的技术支撑。