在新能源汽车产业高速发展的背景下,电池盒作为动力电池系统的核心防护部件,其量产效率、结构强度与轻量化水平直接影响整车续航、安全性能及制造成本。传统开模成型工艺因树脂挥发、纤维分布不均等问题,难以满足电池盒高强度、高气密性及复杂结构的一体化成型需求。而树脂传递模塑(RTM)快速闭模成型技术结合模具热流道优化设计,通过精准控制树脂流动路径与固化过程,实现了电池盒的高效、高质量量产,成为行业技术升级的关键路径。
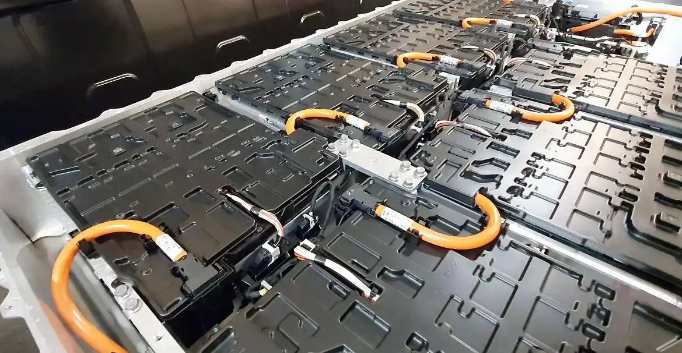
一、RTM快速闭模成型技术:工艺原理与核心优势
RTM技术通过将低黏度树脂在闭合模具中低压注入纤维预制体,经浸润、固化后脱模得到成品。相较于传统手糊成型或热压罐工艺,其核心优势体现在以下方面:
工艺效率与质量提升
闭模设计减少污染:全封闭模具环境避免树脂挥发,减少VOC排放,同时确保纤维含量稳定在50%-70%,显著高于开模工艺的30%-40%。
复杂结构一体化成型:以特斯拉Model 3电池盒为例,其采用HP-RTM工艺(高压树脂传递模塑),通过双面钢模与热流道系统,实现含金属嵌件、散热通道的复杂结构一次成型,生产周期缩短至传统SMC工艺的1/3。
力学性能优化:宝马i3电池盒采用T-RTM(热塑性RTM)工艺,在树脂注入阶段同步原位聚合PA6基体,使电池盒弯曲强度达450MPa,较SMC材料提升30%,且耐热性突破180℃。
材料与成本优势
树脂体系多元化:支持环氧、聚氨酯、酚醛等多种树脂体系,适配不同性能需求。例如,蔚来ES6电池盒采用阻燃型环氧树脂,通过热流道动态控温,使树脂凝胶时间误差控制在±5秒内,废品率降低至2%以下。
模具寿命与复用性:德国某企业开发的乙烯基酯模具树脂系统,在连续生产18,000模次后仍保持表面精度±0.05mm,单模成本较铝合金模具降低40%。
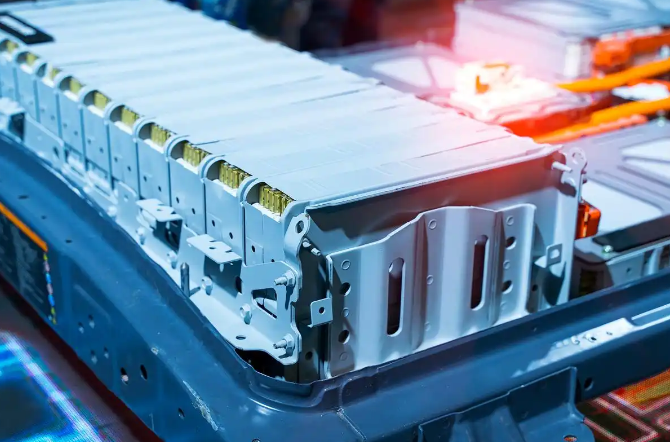
二、模具热流道优化设计:关键技术突破与实施路径
热流道系统通过集成加热元件与流道布局优化,实现树脂温度、压力及流速的精准调控,是RTM工艺量产化的核心保障。
热流道结构设计创新
分区控温技术:针对电池盒厚度不均(如2.5-10mm)的特点,采用多区域独立加热流道。例如,德国宇航中心开发的电池盒模具,通过74个嵌入式传感器实时监测树脂黏度变化,结合PID算法动态调整各区温度,使树脂在厚壁区(10mm)与薄壁区(2.5mm)的固化时间差缩小至15秒内,避免局部过固化或欠固化。
螺旋叶片驱动系统:某专利技术通过在流道内设置横向与竖向螺旋叶片,强制树脂混合并加速浸润。实验数据显示,该设计使树脂填充时间缩短40%,同时纤维冲刷缺陷率从8%降至0.5%。
密封与排气系统优化
动态密封技术:采用“Z”型截面硅胶密封圈,通过模具开合时的弹性变形实现动态密封。宝马iX3电池盒模具应用此技术后,密封寿命提升至1,200模次,较传统被动密封方案延长3倍。
真空辅助排气:在模具型腔边缘设置微孔排气通道,结合真空泵将气体压力抽至-0.095MPa以下。特斯拉4680电池盒模具通过此设计,使制品孔隙率从3.2%降至0.8%,电绝缘性能提升2个数量级。
热流道材料与制造工艺
高导热复合材料应用:模具流道壁采用石墨烯增强铝合金(导热系数达320W/m·K),较传统6061铝合金提升60%。某企业实测显示,该材料使树脂固化时间缩短25%,能耗降低18%。
增材制造一体化成型:通过金属3D打印技术直接制造含复杂流道的模具。例如,某电池盒模具采用SLM工艺,将流道与冷却水道集成于单一部件,减少装配误差,同时使模具重量减轻35%。

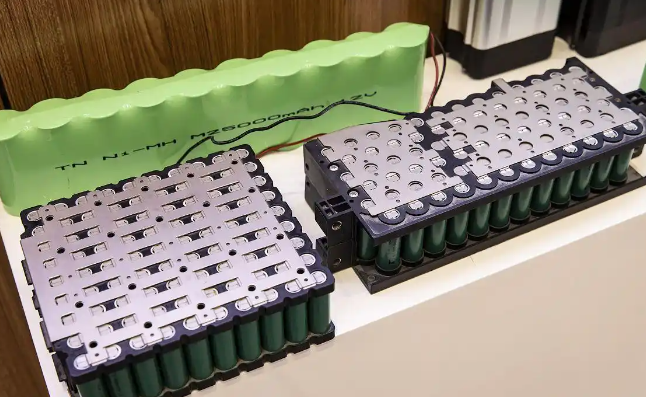
三、量产化应用案例与性能验证
动力电池包集成化应用
特斯拉4680电池盒:采用HP-RTM工艺与热流道优化模具,实现单体电芯数量从2,170个减少至960个,系统能量密度提升至330Wh/kg。通过流道仿真优化,使电池盒在2.5mm薄壁区的树脂填充速度达120g/s,较传统工艺提升3倍。
宁德时代CTP 3.0电池箱:结合T-RTM工艺与模块化热流道设计,将电池包与底盘一体化成型。热流道系统通过分区控温,使不同电芯模块的固化时间同步误差控制在±2秒内,箱体抗冲击强度达120kJ,满足IP69K防护等级。
性能验证与标准化进展
机械性能测试:某第三方机构对HP-RTM工艺生产的电池盒进行振动、冲击及挤压测试,结果显示其在Z轴方向承受15g冲击后无泄漏,挤压变形量达25%时无起火,远超GB/T 31467.3标准要求。
热管理优化:蔚来ET7电池盒通过热流道设计集成液冷流道,使电池模组温差从传统风冷的8℃缩小至2℃以内,高温快充效率提升15%,同时流道压力损失降低至0.05MPa,冷却液泄漏风险趋近于零。

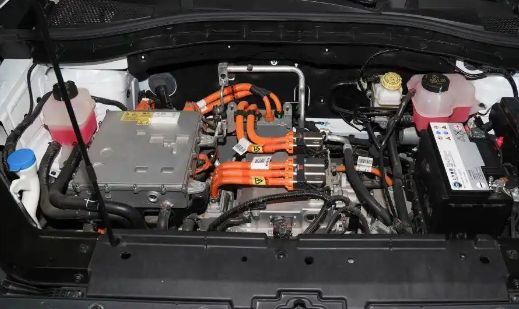
四、挑战与未来发展方向
技术瓶颈与解决方案
大型构件浸渍不均:针对长度超1.2m的电池盒,可通过多注入口协同控制与超声波辅助浸润技术解决。某研究显示,结合28kHz超声波振动,可使树脂在纤维中的渗透率提升40%。
热流道能耗优化:采用热管技术回收固化余热,将模具预热能耗降低30%。某企业实测数据显示,该技术使单件电池盒生产能耗从12kWh降至8.5kWh。
未来技术趋势
AI驱动的工艺闭环控制:通过集成机器视觉与深度学习算法,实时分析树脂流动前沿位置,动态调整热流道参数。某项目已实现孔隙率预测精度达92%,生产效率提升22%。
生物基树脂与可回收模具:开发基于亚麻纤维与生物基环氧树脂的RTM体系,结合3D打印砂型模具,使电池盒碳足迹降低40%。宝马集团计划2030年前将此类技术应用于其全系电动车型。
结语
RTM快速闭模成型与模具热流道优化设计的结合,为新能源汽车电池盒的规模化生产提供了技术可行性。通过工艺参数的精准调控与模具设计的智能化升级,该方案不仅解决了传统工艺的效率低、质量不稳定等问题,更推动了电池系统向轻量化、高安全、长寿命方向发展。随着材料科学与数字孪生技术的进一步融合,RTM工艺有望在2025年后成为新能源汽车核心部件制造的主流技术,助力全球汽车产业实现碳中和目标。