在全球节能减排趋势的推动下,汽车轻量化已成为行业技术升级的核心方向。热塑性复合材料凭借其高强度、低密度、可回收等特性,正逐步取代传统金属材料,成为驱动汽车轻量化革命的关键力量。从新能源汽车续航提升到燃油车能效优化,热塑性复合材料的应用不仅重塑了汽车制造工艺,更催生了材料科学领域的创新浪潮。然而,技术突破与产业化落地之间仍存在显著鸿沟,如何平衡性能提升与成本控制,成为制约行业发展的核心命题。
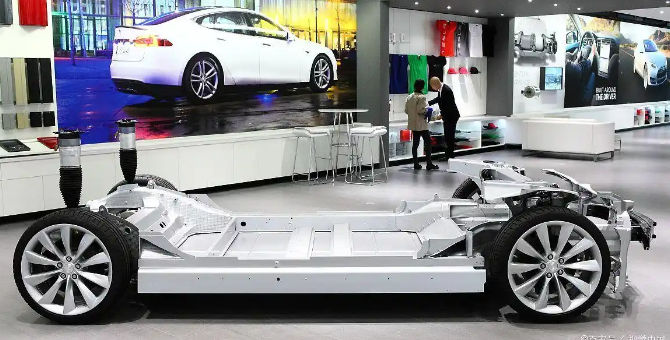
技术突破:材料性能与成型工艺的双重革新
热塑性复合材料的性能突破主要体现在纤维增强技术与基体材料创新两大领域。以连续碳纤维增强聚醚醚酮(CF/PEEK)为例,该材料通过将碳纤维的强度与PEEK树脂的耐热性结合,实现了拉伸强度超过2000MPa、耐温性达260℃的突破。这种材料在汽车悬挂系统、电池包壳体等关键部件的应用中,可减重40%以上,同时满足碰撞安全标准。此外,玻璃纤维增强聚丙烯(GFRTP)通过优化纤维分布方向,在保持成本优势的同时,将弯曲模量提升至12GPa,已广泛用于汽车前端框架、座椅骨架等部件。
成型工艺的革新则进一步释放了材料的性能潜力。模压成型技术通过精准控制纤维铺层角度,实现了复杂结构件的一次成型。例如,采用长纤维增强热塑性塑料(LFT)模压工艺制造的汽车踏板,在保证刚性的同时,将重量从传统钢制件的2.8kg降至1.1kg。而注塑成型技术则通过微发泡工艺,在保险杠等大型部件中形成微孔结构,既保持了抗冲击性能,又实现了15%的减重效果。
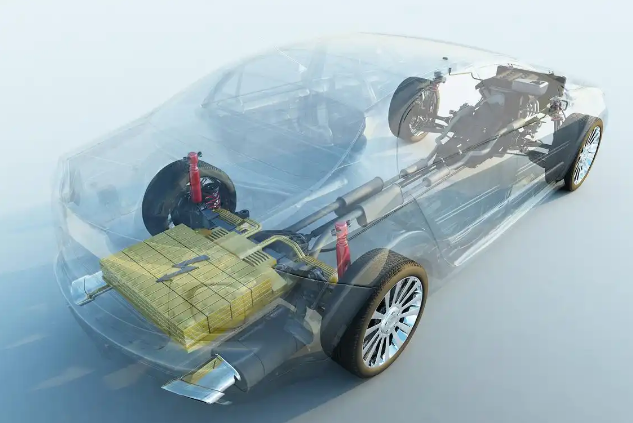
产业化挑战:成本、工艺与市场的三角博弈
尽管技术优势显著,热塑性复合材料的产业化进程仍面临多重挑战。材料成本是首要瓶颈。以CF/PEEK为例,其原料价格高达每公斤800元,是钢制件的20倍以上。尽管通过回收再利用技术可将材料损耗率从30%降至10%,但初期投资成本仍让多数车企望而却步。此外,成型工艺的复杂性也制约了规模化生产。模压成型设备单台投资超千万元,且对模具精度要求极高,导致小批量生产时单件成本居高不下。
市场接受度则是另一大障碍。汽车行业对材料性能的验证周期长达3-5年,而热塑性复合材料的耐久性数据积累尚不充分。例如,在高温高湿环境下,GFRTP的蠕变性能仍需进一步验证。此外,维修体系的滞后也影响了市场推广。当前,采用热塑性复合材料的部件损坏后,多需整体更换,维修成本是传统金属件的3倍以上。
破局之路:协同创新与场景深耕
面对产业化挑战,行业正探索多维度解决方案。在材料端,通过开发连续纤维增强热塑性预浸带(TFP),将纤维含量从40%提升至60%,同时降低熔体黏度,使注塑成型周期缩短40%。在工艺端,自动化铺丝技术与在线监测系统的结合,将成型良品率从85%提升至98%。例如,某研发机构通过引入AI视觉检测系统,实时修正纤维铺层偏差,使A柱加强件的疲劳寿命达到钢制件的1.2倍。
场景化应用则为产业化提供了突破口。在新能源汽车领域,热塑性复合材料在电池包下箱体的应用已实现商业化。通过采用夹芯结构设计,在保持IP67防护等级的同时,将重量从25kg降至12kg,续航里程提升6%。而在商用车领域,CMT片材制造的客车骨架,使整车减重30%,运营成本降低15%。这些场景的成功验证,正逐步打消车企对材料可靠性的疑虑。
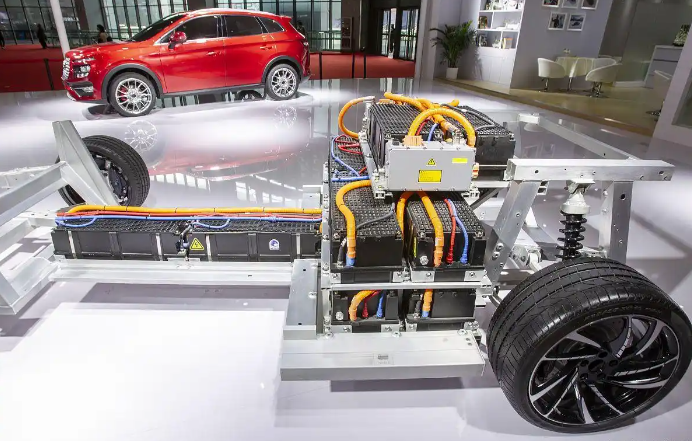
结语:从实验室到量产线的跨越
热塑性复合材料的轻量化革命已进入深水区。技术层面,材料性能与成型工艺的持续突破,为产业化奠定了基础;产业层面,成本优化与场景深耕的协同推进,正加速技术落地。据预测,到2030年,全球汽车用热塑性复合材料市场规模将突破500亿元,年复合增长率达18%。然而,要实现这一目标,行业仍需在材料回收体系、标准制定、产业链协同等方面深化合作。唯有打破技术、成本与市场的三角困局,热塑性复合材料才能真正引领汽车轻量化的未来。