在碳纤维复合材料(CFRP)的制造过程中,模压成型工艺因其高效、稳定的特点而得到广泛应用。然而,该工艺在成型过程中往往会产生残余应力,同时纤维取向的控制也对最终产品的性能有着至关重要的影响。本文将就碳纤维复材模压成型工艺中的残余应力消减与纤维取向调控进行深入探讨。
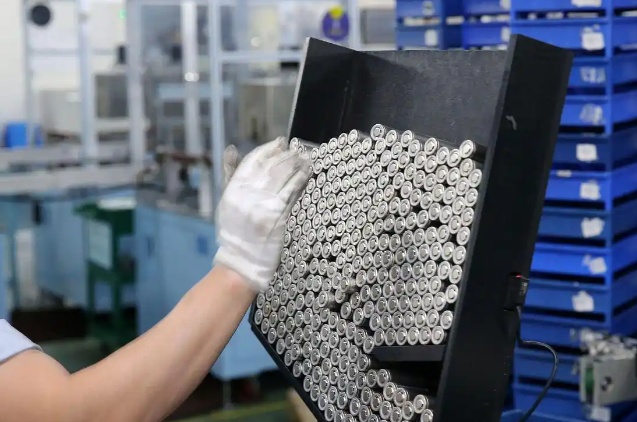
残余应力消减的重要性
残余应力是材料在成型过程中由于不均匀变形或温度变化而产生的内部应力。在碳纤维复材模压成型中,由于碳纤维与树脂基体之间的热膨胀系数差异,以及成型过程中的压力、温度等工艺参数的变化,都可能导致残余应力的产生。这些残余应力不仅会影响产品的尺寸稳定性,还可能降低其力学性能,甚至导致产品在使用过程中出现开裂、变形等问题。
残余应力消减方法
振动时效:振动时效是通过振动使工件内部产生交变应力,与原有的残余应力相叠加,使局部材料发生屈服效应,从而释放残余应力。对于碳纤维复材模压成型产品,振动时效可以在一定程度上消减其残余应力,提高尺寸稳定性。
优化工艺参数:通过调整模压成型过程中的温度、压力、保温时间等工艺参数,可以减小成型过程中的不均匀变形,从而降低残余应力的产生。例如,采用合理的升温速率和保温时间,可以使树脂基体充分固化,减少内应力的产生。
后处理工艺:在模压成型后,采用适当的后处理工艺,如热处理、表面处理等,也可以进一步消减残余应力。热处理可以通过改变材料的内部组织结构,释放残余应力;表面处理则可以通过改善材料表面的应力状态,提高产品的整体性能。
纤维取向调控的重要性
纤维取向是碳纤维复材性能的关键因素之一。不同的纤维取向会导致材料在力学性能上的显著差异。例如,沿纤维方向的拉伸强度远高于垂直于纤维方向的拉伸强度。因此,在模压成型过程中,精确控制纤维取向对于获得高性能的碳纤维复材产品至关重要。
纤维取向调控方法
模具设计:模具的设计对纤维取向有着直接的影响。通过合理设计模具的型腔形状、尺寸和分型面等,可以引导纤维在成型过程中按照预定的方向排列。例如,采用具有特定形状的芯模或型腔,可以使纤维在成型过程中自然形成所需的取向。
铺层设计:铺层设计是调控纤维取向的重要手段。通过合理安排预浸料的铺层顺序、角度和层数等,可以实现纤维在三维空间内的精确取向。例如,采用交叉铺层、角度铺层等方式,可以优化材料的力学性能,提高其各向同性或各向异性。
工艺控制:在模压成型过程中,工艺参数的控制也对纤维取向有着重要影响。例如,通过控制压力的大小和分布,可以使纤维在成型过程中受到均匀的挤压和流动,从而保持其预定的取向。同时,合理的升温速率和保温时间也可以确保树脂基体在固化过程中不会破坏纤维的取向。
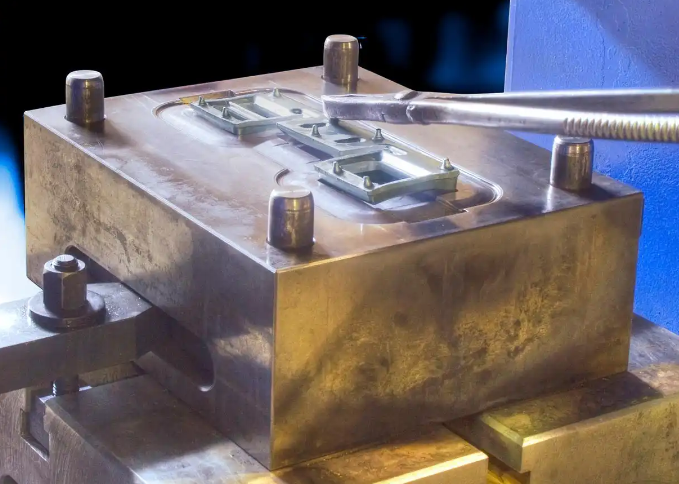
碳纤维复材模压成型工艺中的残余应力消减与纤维取向调控是确保产品质量和性能的关键环节。通过采用振动时效、优化工艺参数和后处理工艺等方法,可以有效消减残余应力;通过模具设计、铺层设计和工艺控制等手段,可以精确调控纤维取向。未来,随着技术的不断进步和创新,碳纤维复材模压成型工艺将更加完善,为高性能碳纤维复材产品的制造提供更加有力的支持。