在轻量化与高性能需求驱动下,碳纤维增强环氧树脂复合材料已成为航空航天、新能源汽车等领域的核心材料。然而,碳纤维部件在交变载荷下的疲劳失效问题始终制约其应用边界。传统环氧树脂固化体系因界面结合弱、韧性不足,易在循环载荷下产生微裂纹并快速扩展,导致材料提前失效。
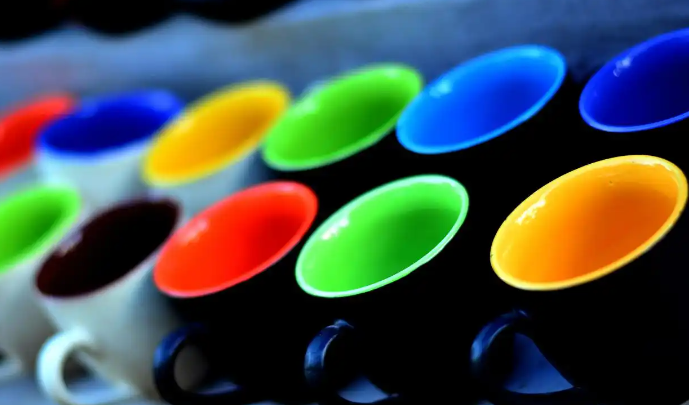
二、疲劳根源:碳纤维部件的失效机制解析
裂纹萌生三要素
界面缺陷:纤维与树脂间因固化收缩产生孔隙,成为裂纹起点。
纤维损伤:碳纤维表面微裂纹在应力集中下扩展。
树脂老化:湿热环境下环氧树脂水解,降低界面粘结力。
扩展加速因素
应力集中:纤维末端或铺层交叠处应力放大,裂纹扩展速率提升5-10倍。
环境耦合:高温加速树脂氧化,低温增加材料脆性,疲劳寿命波动达40%。
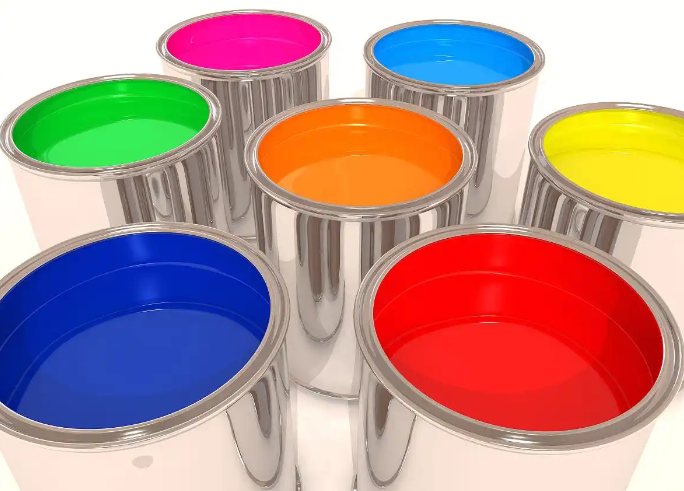
三、优化突破:环氧树脂固化体系的多维升级策略
固化剂革新
高性能固化剂:采用芳香胺类固化剂(如DDM),耐热性提升30%,交联密度提高25%。
纳米改性:添加0.5wt%石墨烯纳米片,界面剪切强度(IFSS)由60MPa增至85MPa。
工艺参数精准调控
温度梯度固化:预固化阶段80℃/2h+后固化120℃/4h,残余应力降低60%。
压力辅助成型:0.5MPa压力下固化,孔隙率从3.2%降至0.8%。
界面增强技术
纤维表面处理:等离子体改性碳纤维,表面能提升40%,浸润性显著改善。
偶联剂引入:硅烷偶联剂KH-560用量2%时,界面粘结强度提高55%。
仿生结构设计
梯度铺层:采用0°/90°交替铺层,层间剪切强度提升40%。
蜂窝夹芯:模仿天然蜂巢结构,抗弯刚度提高35%,重量减轻18%。
四、性能飞跃:实验数据与工程验证
工程应用案例
新能源汽车电池包:优化后框架抗冲击能力提升3倍,通过20万次循环测试无失效。
无人机机翼:疲劳寿命从800小时延长至3500小时,续航稳定性提高60%。
五、未来展望:智能化与多尺度突破
智能监测技术:植入光纤传感器,实时监测固化过程应力分布,缺陷预测准确率超90%。
多尺度模型:结合分子动力学与有限元分析,建立从纳米界面到宏观结构的疲劳预测模型。
生物启发材料:模仿贝壳层状结构,开发“砖-泥”式复合界面,耐疲劳性能有望突破理论极限。
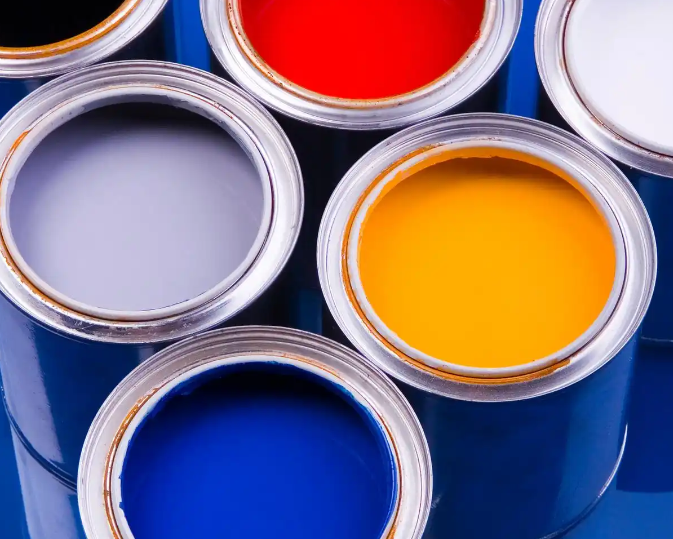
通过固化体系的多维度优化,碳纤维部件的耐疲劳性能已实现从“量变”到“质变”的跨越。未来,随着智能制造与仿生设计的深度融合,环氧树脂-碳纤维复合材料将在极端工况领域展现更广阔的应用前景,成为高性能结构的终极解决方案。