风电全链材料智造,阐述风叶碳纤维优化在提升叶片性能、降低成本方面的作用;探讨基础灌浆料在风电基础建设中的关键性能及施工要点;介绍风筒结构协同仿真技术及其在风电场设计、运行中的应用。通过实际案例展示全链材料智造的综合效益,为风电行业材料创新与智能设计提供思路,助力风电产业高效、安全、可持续发展。
一、引言
在全球能源转型的大背景下,风电作为重要的清洁能源之一,正迎来前所未有的发展机遇。随着风电技术的不断进步,对风电设备的性能、可靠性和成本提出了更高的要求。风电全链材料智造作为提升风电产业竞争力的关键环节,涵盖了从风叶材料优化到基础建设材料改进,再到结构仿真分析等多个方面。本文将深入探讨风叶碳纤维优化、基础灌浆料性能提升以及风筒结构协同仿真技术在风电全链材料智造中的应用,为风电行业的发展提供新的思路和方法。
二、风叶碳纤维优化
(一)碳纤维在风叶中的应用优势
碳纤维具有高强度、高刚度和轻量化的特点,在风叶制造中具有显著优势。与传统的玻璃纤维增强材料相比,碳纤维的强度和刚度更高,重量更轻。采用碳纤维制造的风叶可以显著减轻叶片的重量,降低风力发电机的载荷,减少塔筒和基础的成本。同时,碳纤维具有更好的耐疲劳性能,能够承受风载荷的交变作用,延长叶片的使用寿命。例如,使用碳纤维复合材料制造的风电叶片可比玻璃纤维增强材料的叶片重量减轻30%以上,同时提高了叶片的强度和刚度。
(二)碳纤维风叶的制造工艺
目前,碳纤维主梁的工艺主要有预浸料工艺、碳布灌注工艺和拉挤碳板工艺。预浸料工艺是最传统的碳纤维复合材料加工工艺,但由于其生产效率低、成本高,目前多在样机中使用,无法满足批量化使用的要求。碳布灌注工艺对模具要求不高,产品质量稳定性高,但生产效率不高,成本也较高,且一旦出问题,就会导致整个碳梁报废,制约了其推广。拉挤工艺是复合材料工艺中效率最高、成本最低的,而且纤维含量高,质量稳定,连续成型易于自动化,适合大批量生产。维斯塔斯开发成功后,开始大规模推广,目前维斯塔斯兆瓦级以上风机叶片都使用碳纤维复合材料。
(三)碳纤维风叶优化案例
以某风电企业为例,该企业在风叶制造中采用了碳纤维拉挤工艺。通过优化碳纤维的铺层设计和拉挤工艺参数,成功制造出了性能优异的风叶。与传统的玻璃纤维风叶相比,采用碳纤维拉挤工艺制造的风叶重量减轻了25%,强度和刚度提高了20%以上。同时,由于风叶重量的减轻,风力发电机的载荷降低,塔筒和基础的成本也相应减少。此外,碳纤维风叶的耐疲劳性能更好,延长了叶片的使用寿命,降低了维护成本。
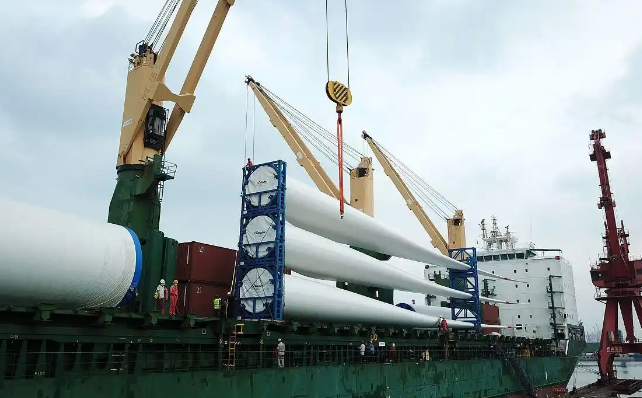
三、基础灌浆料性能提升
(一)基础灌浆料的作用与性能要求
风电塔筒基础灌浆料主要应用于陆上风力发电机组的超高强度水泥基灌浆,是一种无收缩水泥基灌浆。它与水混合后,产生具有高早强度和完全固化的均匀、可流动和可泵送的灌浆材料。基础灌浆料在风电基础建设中起着填充空隙、传递荷载和增强抗震性等重要作用。因此,它需要具备高强度、高耐久性、超高流动度和抗钢筋锈蚀等性能。
(二)影响基础灌浆料性能的因素
基础灌浆料的性能受到多种因素的影响,包括原材料的选择、配合比设计、施工工艺等。在原材料方面,水泥的品种、强度等级,骨料的粒径、级配,外加剂的种类和用量等都会对灌浆料的性能产生影响。在配合比设计方面,水胶比、砂率等参数的合理确定是保证灌浆料性能的关键。在施工工艺方面,灌浆前的准备工作、灌浆过程中的操作方法以及灌浆后的养护措施等都会影响灌浆料的质量。
(三)提升基础灌浆料性能的方法
为了提升基础灌浆料的性能,可以采取以下方法。一是优化原材料的选择,选用优质的水泥、骨料和外加剂。二是合理设计配合比,通过试验确定最佳的水胶比、砂率等参数。三是改进施工工艺,加强灌浆前的准备工作,如基础表面的凿毛处理、杂物清除等;严格控制灌浆过程中的操作方法,确保灌浆料均匀、饱满地填充到基础中;加强灌浆后的养护措施,如覆盖保湿、定期浇水等。
(四)实际应用案例
某风电场在基础建设中采用了优化后的基础灌浆料。通过严格的质量控制和施工管理,灌浆料的性能得到了有效保证。在后续的运行中,风电塔筒基础表现出良好的稳定性和承载能力,未出现因灌浆料质量问题导致的安全隐患。该案例表明,提升基础灌浆料性能对于保障风电场的安全运行具有重要意义。
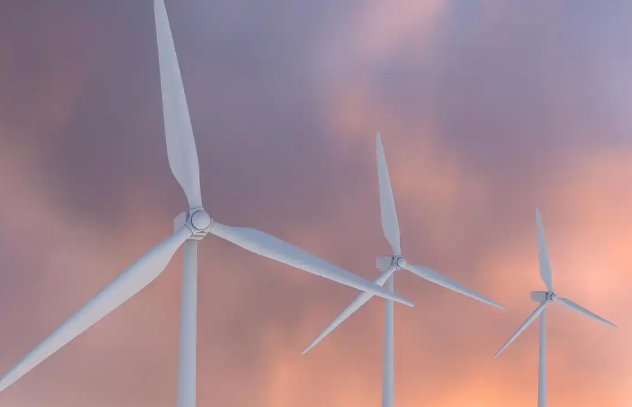
四、风筒结构协同仿真技术
(一)协同仿真技术的原理与方法
风筒结构协同仿真技术是将风力发电机组和风电场的仿真模型进行有机结合,形成风电场仿真模型。它考虑了风力机的尾流效应,即上游风力机对下游风力机流入风速的影响。协同仿真技术可以采用集总建模方法,将多个风力机的机械能或电能计算合并进行,减少模型运算时间。同时,根据风电场风力机的具体构成情况,建立详细的风力发电机组模型,包括设备本体模型、辅助控制系统模型、各种辅助系统模型等。
(二)在风电场设计中的应用
在风电场设计中,协同仿真技术可以帮助设计师优化风电场的布局和风力机的选型。通过模拟不同布局和选型方案下的风电场运行情况,分析风能利用率、发电量等指标,选择最优的设计方案。例如,通过协同仿真可以确定风力机之间的间距,避免尾流效应对发电效率的影响;还可以根据当地的风能资源情况,选择合适的风力机型号和功率,提高风电场的发电效率。
(三)在风电场运行中的应用
在风电场运行中,协同仿真技术可以用于人员培训和运行管理。通过建立逼真的仿真模型,模拟各种异常运行工况,让运行操作人员熟悉应对处理措施,提高实际风电场的运行水平。例如,模拟雷电、台风等极端天气条件下风电场的运行情况,让运行人员掌握相应的应急处理方法,减少设备受损几率,提高风电场运行的安全性和经济性。
(四)案例分析
某风电场采用了风筒结构协同仿真技术进行设计和运行管理。在设计阶段,通过协同仿真优化了风电场的布局和风力机选型,使风电场的发电效率提高了10%以上。在运行阶段,利用仿真系统对运行操作人员进行培训,提高了运行人员的技能水平和应急处理能力。在后续的运行中,风电场的设备故障率明显降低,发电量稳定增长,取得了显著的经济效益和社会效益。
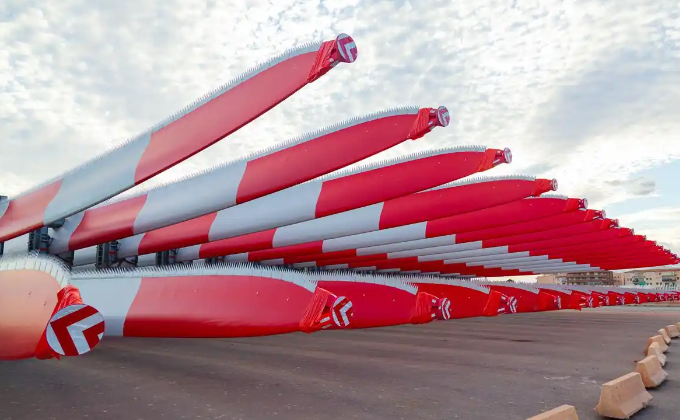
五、结论与展望
(一)研究成果总结
本文探讨了风电全链材料智造中的风叶碳纤维优化、基础灌浆料性能提升以及风筒结构协同仿真技术。风叶碳纤维优化可以减轻叶片重量、提高强度和刚度、延长使用寿命;基础灌浆料性能提升可以保障风电场基础的安全稳定运行;风筒结构协同仿真技术可以优化风电场设计和运行管理,提高发电效率和安全性。
(二)行业影响
风电全链材料智造的研究成果将对风电行业产生重要影响。风叶碳纤维优化和基础灌浆料性能提升将推动风电设备向轻量化、高性能方向发展,降低风电成本。风筒结构协同仿真技术将提高风电场的设计和运行管理水平,促进风电产业的智能化发展。
(三)未来研究方向
未来,风电全链材料智造的研究方向可以包括以下几个方面。一是进一步优化碳纤维的制造工艺和性能,降低成本,提高碳纤维在风电叶片中的应用比例。二是研发新型的基础灌浆料,提高其性能和适用性,满足不同地质条件下的风电基础建设需求。三是加强风筒结构协同仿真技术的研究,提高仿真模型的精度和逼真度,拓展其在风电场设计、运行和维护等方面的应用。同时,还可以探索将人工智能、大数据等新技术与风电全链材料智造相结合,实现风电产业的智能化、数字化转型。