航空航天领域对复合材料轻量化、高强度、高可靠性的需求,推动环氧树脂基碳纤维预浸料技术向多尺度结构设计与界面增强方向突破。本文从碳纤维表面改性、纳米增强体调控、树脂基体增韧及成型工艺优化等维度,系统阐述界面增强机制与多尺度协同作用,结合航空级预浸料制备案例,提出基于分子动力学模拟与工艺参数耦合优化的技术路径,为新一代航空复合材料开发提供理论支撑。
碳纤维表面多尺度改性技术
1. 化学接枝与氧化处理
氧化法:通过气相氧化(如氟/氧混合气处理)或液相氧化(浓硝酸溶液浸泡)在碳纤维表面引入羧基、羟基等活性基团,提高润湿性。
化学接枝:采用氨基封端萘二酰亚胺(NDI)或聚乙烯亚胺(PEI)等分子接枝,实现碳纤维与环氧树脂的化学键连接。例如,接枝分子量为600的PEI可使界面剪切强度提升38.9%,弯曲强度提升36.7%。
2. 纳米增强体复合改性
碳纳米管(CNTs)接枝:CNTs通过π-π堆积和羧基-氨基反应锚定于碳纤维表面,形成“铆钉”状结构,显著增强机械锁合作用。当CF-PEI与CNT-COOH质量比为2:1时,界面剪切强度(IFSS)提升74.1%,弯曲强度提升55.2%。
氧化石墨烯(GO)锚定:GO片层以“直立”形态分布于碳纤维表面,形成中等模量界面层,有效传递载荷并分散应力。当CF-PEI与GO质量比为40:1时,界面性能最优,GO片层间距可控至纳米级。
3. 晶须化与纳米纤维界面相
氯化芳纶纳米纤维(Cl-ANF)涂层:通过浸涂工艺在等离子体处理后的碳纤维表面形成致密纳米纤维网络,利用范德华力、氢键及π-π堆积增强界面结合。实验表明,Cl-ANF界面相使IFSS提升79.8%,短梁剪切强度(SBS)提升33.7%,且不损伤纤维拉伸强度。
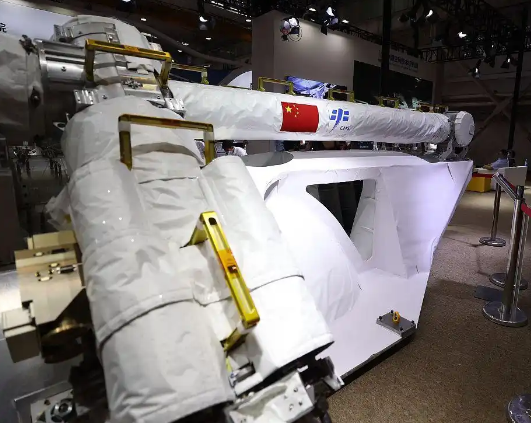
环氧树脂基体增韧与流变调控
1. 反应型互穿网络增韧
采用核壳橡胶粒子或热塑性树脂与环氧树脂共混,形成交联互穿网络结构。例如,增韧剂含量为10%时,复合材料冲击后压缩强度(CAI)达330 MPa,断裂韧性提升40%,玻璃化转变温度(Tg)仅下降6℃。
2. 流变性能优化
通过活性稀释剂(如丁基缩水甘油醚)降低树脂黏度,改善纤维浸渍效果。例如,将黏度从5000 mPa·s降至1500 mPa·s,可显著减少预浸料孔隙率。
多尺度成型工艺协同优化
1. 界面调控与熔融浸渍协同
增容剂法:利用增容剂促进碳纤维与热塑性树脂的相容性,例如,通过添加增容剂使界面剪切强度提升显著。
结晶行为调控:在碳纤维表面诱导形成横晶结构,增强界面黏结。例如,通过控制温度和时间,使横晶层厚度增加,界面强度提升。
2. 航空级预浸料制备案例
T800碳纤维/环氧树脂体系:纤维面密度120 g/m²,树脂含量38%,拉伸强度2800 MPa,适用于机翼蒙皮。
东丽T1100G/3960树脂体系:拉伸强度6.3 GPa,模量310 GPa,应用于空客A350机身。

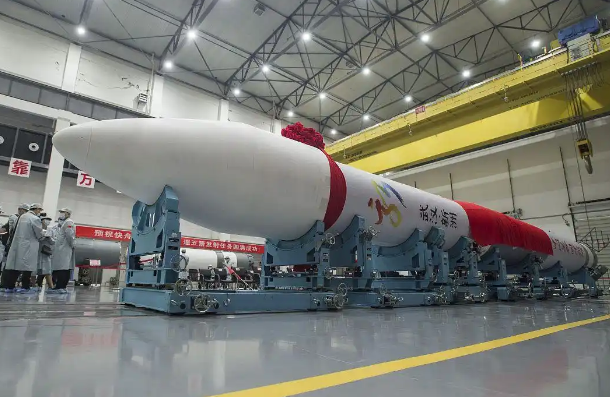
界面增强机制与表征技术
1. 多尺度界面模型
机械互锁理论:通过表面粗糙度设计增强纤维与树脂的机械嵌合。
化学键理论:利用接枝官能团与树脂基体形成共价键。
过渡层理论:在纤维与树脂间引入中等模量界面层,缓解应力集中。
2. 微观表征技术
X射线光电子能谱(XPS):分析表面化学组成。
扫描电子显微镜(SEM):观察界面形貌与失效模式。
原子力显微镜(AFM):测量表面粗糙度与弹性模量梯度。
结论与展望
面向航空航天装备的环氧树脂基碳纤维预浸料技术,需通过多尺度改性、基体增韧与工艺协同优化,实现界面性能与整体力学性能的同步提升。未来研究方向包括:
生物基增容剂开发:利用可再生资源替代传统增容剂,降低环境影响。
数字孪生技术:通过工艺模拟优化预浸料孔隙率与纤维分布均匀性。
自修复界面设计:引入动态共价键或超分子相互作用,赋予复合材料损伤自修复能力。
通过多学科交叉与技术创新,环氧树脂基碳纤维预浸料将在航空发动机叶片、深空探测器结构件等极端工况领域发挥更大潜力,推动航空航天装备向更轻、更强、更智能的方向发展。