在高端制造领域,碳纤维因其轻质高强、耐腐蚀等特性成为航空航天、汽车、风电等行业的核心材料。然而,其生产过程中高达30%的原材料浪费率以及废弃物难以降解的特性,正成为制约产业可持续发展的瓶颈。近年来,全球科研机构与企业通过技术创新,在碳纤维无损再生领域取得突破性进展,不仅实现了材料性能的“全保留”,更推动循环经济模式向高附加值方向升级。
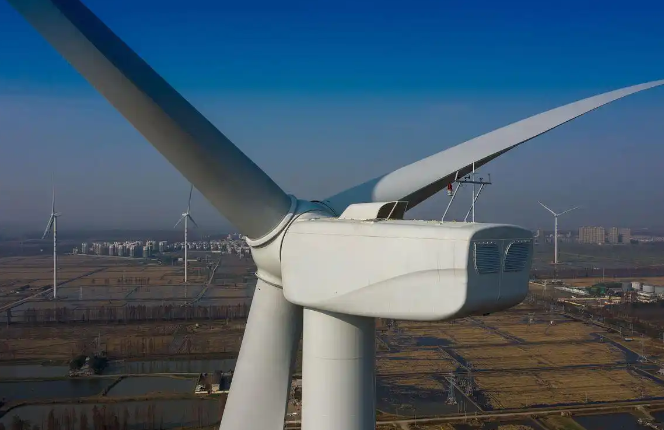
一、技术突破:从“降级利用”到“全性能再生”
传统碳纤维回收技术存在显著局限性。例如,机械粉碎法通过物理研磨将废弃复合材料转化为粉末,但树脂残留导致产品仅能作为填充物或燃料,附加值极低;热解法虽能分解树脂,但高温环境易破坏纤维结构,导致强度损失超过40%;溶剂溶解法虽可回收纤维,但高温高压条件或腐蚀性溶剂的使用带来安全隐患与成本压力。
针对上述痛点,新一代无损再生技术实现三大革新:
化学回收法:通过可降解热固性树脂基体,在特定催化剂作用下实现树脂的温和解聚。例如,基于动态共价键的环氧树脂体系,可在180℃下解聚为可再聚合单体,回收纤维强度保持率达95%以上。
微波辅助热解:利用微波选择性加热特性,在惰性气体环境中将树脂分解为气体与液体产物,纤维损伤率较传统热解降低60%。
超临界流体萃取:以超临界二氧化碳为溶剂,在35℃、15MPa条件下溶解树脂,回收纤维表面残留树脂量低于0.5%,且无需后续清洗工序。
研发的移动式再生设备集成AI视觉识别系统,可实时分析进料特性并生成数据表,确保回收材料性能可追溯。该设备已实现航空航天级再生碳纤维的量产,其3D打印模具在强度、疲劳寿命等指标上与原生材料无显著差异。
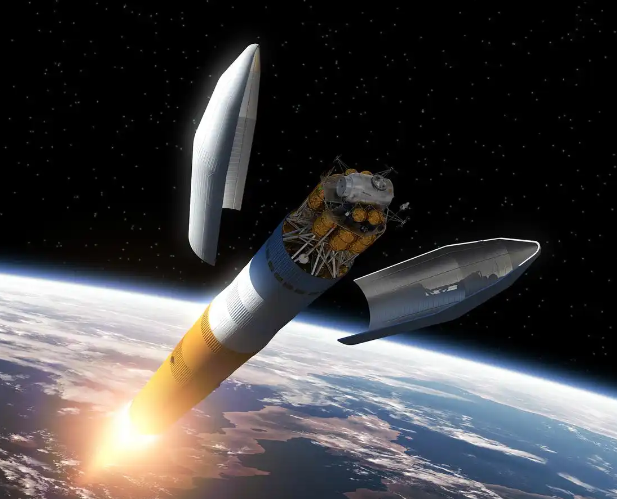
二、应用场景:从高端制造到民生领域全覆盖
再生碳纤维的性能突破正推动其应用场景向多元化拓展:
航空航天领域:TPAC与TPRC联合开发的再生碳纤维复合材料,已应用于飞机次承力结构件,如整流罩、扰流板等。数据显示,使用再生碳纤维可使部件重量降低15%,燃油效率提升8%,且生产周期缩短30%。
汽车工业:宝马i系列车型中,10%的碳纤维部件采用闭环回收工艺。以i3电动汽车为例,其车顶回收碳纤维的使用使车身减重12公斤,续航里程增加5%。
体育用品:Fairmat公司利用AI与机器人技术,将再生碳纤维制成定制化芯片,应用于高端自行车、滑雪板等。经1000次疲劳测试验证,其抗冲击性能较传统材料提升20%。
建筑领域:美国复合材料回收技术中心开发的交叉层压木材,通过将热改性木材与再生碳纤维结合,实现强度提升30%,且具备抗腐烂、防白蚁特性。

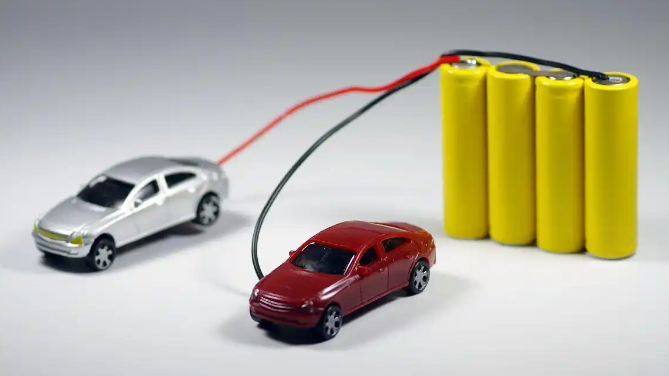
三、政策与市场:全球循环经济体系的协同推进
碳纤维再生技术的突破离不开政策与市场的双重驱动。中国在“十四五”规划中明确提出,到2025年废旧物资循环利用率需达85%,并设立专项资金支持再生材料研发。例如,中国资源循环集团有限公司的成立,标志着国家级资源回收平台正式运行,其年处理能力达50万吨,涵盖风电叶片、退役飞机等碳纤维废弃物。
国际层面,欧盟《循环经济行动计划》要求,到2030年新车再生材料占比需达25%,报废车辆材料回收率达85%。在此背景下,全球碳纤维再生市场规模预计将以12.3%的年复合增长率增长,2030年有望突破百亿美元。
四、挑战与展望:从技术突破到产业生态构建
尽管技术取得突破,碳纤维再生仍面临三大挑战:
成本与效率:当前再生碳纤维生产成本较原生材料高30%-50%,需通过规模化生产与工艺优化降低能耗。
标准体系:缺乏统一的性能分级标准,导致再生材料在高端领域的应用受限。
产业链协同:需建立从废弃物回收、再生加工到终端应用的闭环体系,避免“再生材料-原生材料”的逆向替代。
未来,随着AI、物联网等技术的深度融合,碳纤维再生将向智能化、精准化方向发展。例如,通过区块链技术实现材料全生命周期追溯,或利用数字孪生优化再生工艺参数。在此过程中,碳纤维再生不仅是材料技术的革新,更是循环经济模式从“线性利用”向“闭环共生”转型的关键实践。