3、面芯界面性能表征
轻质夹芯结构优异性能依赖于良好的面芯界面,粘接缺失或过弱会影响面板与芯层间的剪应力传递,脱粘区域甚至会扩散到整个面芯界面造成夹芯结构整体失效,因此有必要考察复合材料夹芯结构的面芯界面性能。一方面,可以通过研究夹芯结构在剪切、侧向压缩和弯曲等工况下的宏观力学性能,对比面芯界面脱粘失效是否先于其他失效模式出现,来定性表征面芯界面性能;另一方面,由于面芯界面的脱粘通常表现为裂纹扩展,也可采用临界应变能释放率来定量表征面芯界面性能,常见的表征方法包括:双悬臂梁 (Double cantilever beam, DCB)、含裂纹夹芯梁 (Cracked sandwich beam,CSB)、混合模式弯曲 (Mixed mode bending MMB) 和双悬臂梁-非均匀弯矩 (Double cantilever beam-uneven bending moment,DCB-UBM),各类试样如图 16 所示。预置裂纹通常在制备过程中通过面板和芯层间植入聚四氟乙烯薄膜来实现。加载过程中需要记录载荷位移曲线与裂纹扩展过程,最终经过计算可得到临界应变能释放率。双悬臂梁方法和含裂纹夹芯梁方法分别对应 I 型 (张开型) 和 II 型 (滑移型) 裂纹加载方式,混合模式弯曲方法和双悬臂梁-非均匀弯矩方法能够表征结构在 I 型和 II 型两种裂纹加载方式下的面芯界面性能。笔者自主设计并搭建了电阻焊接平台,制备了电阻焊接热塑性波纹夹芯结构,图 17 所示的侧压实验结果表明:与热板焊接试件发生面芯脱粘相比,采用电阻焊接后结构发生整体承载优势,在中部发生断裂,面芯界面表现出较高连接强度。该工作证实了电阻焊接方法增强面芯界面的可行性。
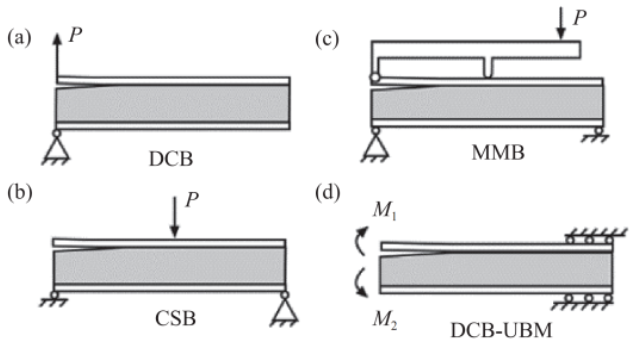
图16脱粘夹芯试样[57]:(a) 双悬臂梁 (DCB);
(b) 混合模式弯曲 (MMB);(c) 含裂纹夹芯梁 (CSB);
(d) 双悬臂梁-非均匀弯矩 (DCB-UBM)
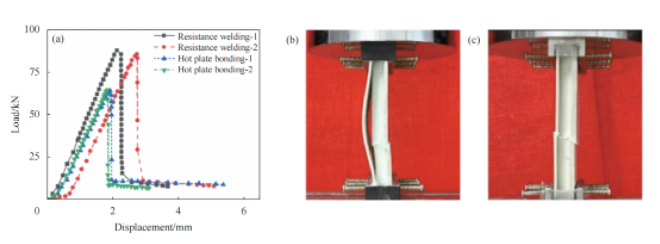
图17 (a) 侧压载荷位移曲线对比;(b) 热板焊接波纹夹芯
结构失效模式;(c) 电阻焊接波纹夹芯结构失效模式
4、应用
热塑性复合材料夹芯结构因其轻质高强、高韧性可回收的特性,已在航空、汽车、风电等领域取得应用。本文重点综述了热塑性复合材料夹芯结构的面芯熔融连接方法,因此本部分相应介绍熔融连接热塑性复合材料夹芯结构的典型应用。Meyer等受捕蝇草结构启发,在胞元间引入柔性铰链设计出了压力促动多孔结 构 (Pressure actuated cellular structures, PACS),推导了最小促动压力下的最佳胞元厚度,借助面芯共编成型制备出可适用于航空变形副翼的热塑性复合材料夹芯结构。采用风洞测试和有限元方法考察了结构刚度,结构在不同气动载荷下可保持结构完整性,能够实现目标载荷下翼型的高速可控驱动 (图18(a))。热塑性蜂窝夹芯板已在电动汽车集成地板 (图18(b)) 和货车车厢上应用,能够大幅降低车辆整体质量,降低油耗。Brádaigh等借助 pCBT 树脂高流动特性,采用真空热压方法整体制备了目前最大的一体成型全热塑性复合材料风电叶片 (图18(c)),该叶片长12.6 m,重500 kg,纤维体积含量50vol%,可供250 kW 风力发电机使用。
美国国家可再生能源实验室 Murray等采用真空辅助树脂传递模塑 (Vacuum assisted resin transfer molding, VARTM) 和二次连接方法成功制备了基于 Elium®树脂体系的热塑性复合材料风电叶片,该叶片长 9 m,在常温下仅用 3 h 即可固结完成,大大降低了时间和能耗成本。由于该工作中叶片各部分采用环氧树脂粘接而成,粘接与固化过程耗时与结构 成型相当,因此Murray等进一步探讨了采用熔融连接的可行性,以GE 公司 56.9 m 型号的风电叶片为对象,采用电阻焊接方法制备了总长为 5 m 的玻璃纤维增强Elium®复合材料叶尖 (图19)。叶尖部分布置了雷电保护系统,实验结果表明在考核工况下电阻焊接界面保护完好。

图18 (a) 可变形副翼;(b) 车用地板;(c) 风电叶片
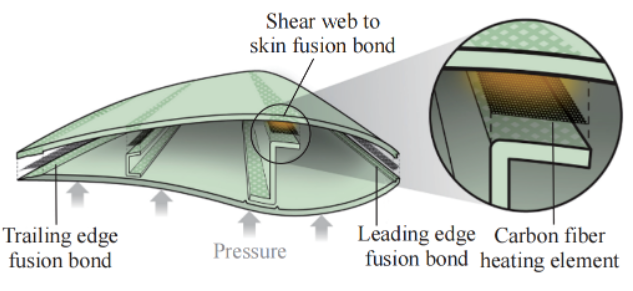
图19 风电叶片各部分电阻焊接示意图
Thomas在 PET 中添加质量分数为 0.01wt%~ 5wt% 的 石 墨 烯 纳 米 片 (Graphene nano-patelet,GNP) 和质量分数为 5wt% 的非连续碳纤维,采用共混造粒与螺杆挤出技术生产了增强型 3D 打印线材,其导电性能和力学性能相较于原有 PET 树脂均有大幅提高。最终 3D 打印出热塑性复合材料蜂窝夹芯结构,成功作为机壳应用于立方微卫星 (Cubic microsatellite)。
面对热塑性复合材料夹芯结构面芯连接的难题,学术和工业界的研究者们针对不同材料体系和结构形式,提出了多种不同技术成熟度的熔融连接技术方法,取得了一定应用。基于研究和应用现状的总结分析,从以下角度对熔融连接热塑性复合材料夹芯结构的发展趋势进行如下展望:
(1) 采用多步法时,面板和芯层可以独立成型,材料和工艺选择相对灵活。而一步法会受到材料、工艺和面芯连接形式等诸多因素的限制。芯层采用模具支撑能够避免芯层在受热受压时局部变形,但一定程度上又阻碍了热塑性夹芯结构的大批量制备。目前连续热压具有大批量、低成本制备的潜力,但纯树脂芯层的力学性能相对较低。对于纤维增强热固性复合材料,Wei等开发出了复合材料蜂窝裁折工艺,有效提高了全热固性复合材料蜂窝夹芯结构的面芯界面强度,提升了结构力学性能。而对于纤维增强热塑性复合材料,预浸料常温下刚度较大,其批量化制备工艺有待于进一步探索。
(2) 电阻焊接、超声焊接、感应焊接产热可控、可长距离连续焊接,具有熔融连接热塑性复合材料大批量制备的潜力。国内外学者在制备工艺、产热机制、性能测试等方面开展了前期的研究工作,现有研究主要是依赖于大量实验结果确定工艺窗口,数值模拟方法并未考虑焊接工艺过程的热力耦合,下一步需要开展大尺寸热塑性复合材料夹芯结构批量化制备的研究工作。
(3) 连续纤维 3D 打印技术可以通过调节工艺参数实现复合材料性能的可控制造,所开发的3D 打印多重界面强化方法能够改善复合材料界面结合强度,也实现了复合材料构件低成本快速制造。目前应用构型主要为波纹、蜂窝夹芯结构,其拓扑构型可看成特定外形沿平面法线拉伸而成。而对于轮廓引导线不与平面垂直、引导线为曲线、其他复杂构型夹芯结构,以及新型材料体系,在批量应用前需要突破相应的连续纤维复合材料增材制造工艺过程控制技术。
(4) 面芯共编技术能够实现三维编织复合材料夹芯结构一体化成型。形成编织预制体后有两种工艺途径可供选择,分别是模压成型和液体成型。模压成型适用于增强体纤维和基体纤维混编体系,在芯层孔隙中需要填充可拆卸模具或是增强材料 (比如泡沫)。液体成型 (如 VARTM) 则依赖于树脂的高流动特性,同时需要根据结构几何构型合理设置出入浇口和流道,选择合理的工艺参数以实现更好的树脂浸润效果,在大尺寸风电叶片成型方面有着广阔的应用前景。